Protolabs launches Consultative Design Service for Injection Moulding
One of the world’s leading digital manufacturers is offering engineers a critical ‘missing link’ that will help them find the best manufacturable solution for their parts.
One of the world's leading digital manufacturers is offering engineers a critical ‘missing link' that will help them find the best manufacturable solution for their parts.
Protolabs, which supports thousands of companies in the UK and Europe every year, has launched a new injection moulding Consultative Design Service that will tap into the critical thinking and problem solving of its 200-strong team of engineers.
Already known for its automated design for manufacturing analysis via its digital quoting platform, the new offer has the potential to help clients across numerous industries optimise performance of its components, reduce manufacturing costs and shorten lead times.
Samuel Guest, Protolabs Product Manager for Injection Moulding, commented: "Our quoting platform is well-known in industry and allows you to upload your CAD and check whether it can be injection moulded - it even suggests alterations that would make it better and save money.
"The advantage is that you will receive your report and quote back within a couple of hours. It's a really fast way of checking that your design is practical for production."
The new complementary service allows you to take advantage of Protolabs' engineering experience in injection moulding to help optimise your solution.
Samuel continued: "Whilst the quoting platform will check that your design is possible, you may also need the critical thinking of a person to find the best solution. There may be other alternatives that save you money or provide better functionality.
"By understanding what it is that you hope to achieve, we can become part of your team to provide that link between design and manufacturing. We are not a design engineering consultancy but can offer design for manufacturing advice. And that's the link that is often missing.
"There are so many variables in design, product development and manufacturing that you do sometimes need to understand the nuances. A simple redesign of a part may, for example, perform the same and save you money through more efficient production, it may speed up delivery for your manufacturing line or improve its functionality.
"Sometimes it may be worth reconsidering the material you select for your part. Understanding your needs means we can provide you with the benefit of our expertise and help transform your injection moulded parts in the process."
The Consultative Design Service allows companies to choose what sort of advice they need. They can continue to use the digital quoting platform by uploading their CAD as many times as they like to check and recheck their designs.
Alternatively, they can take advantage of the company's extended offer by contacting their account manager after they have uploaded their CAD and received their first automated design for manufacturability analysis and quote.
Samuel concluded: "Protolabs makes full use of the digital thread provided by CAD to help automate product development and manufacturing. This makes it faster, more responsive, and repeatable. When you combine the advantages of automation with the critical thinking of humans you have a really powerful proposition. Our new service enables industry to blend the benefits of both to better match their needs."
For more information about Protolabs' new Consultative Design Service, please visit www.protolabs.co.uk/resources/blog/consultative-design-analysis-prepares-parts-for-production/
Featured Product
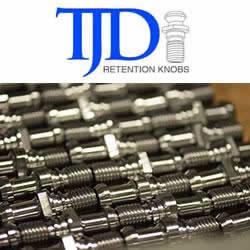
T.J. Davies' Retention Knobs
Our retention knobs are manufactured above international standards or to machine builder specifications. Retention knobs are manufactured utilizing AMS-6274/AISI-8620 alloy steel drawn in the United States. Threads are single-pointed on our lathes while manufacturing all other retention knob features to ensure high concentricity. Our process ensures that our threads are balanced (lead in/lead out at 180 degrees.) Each retention knob is carburized (hardened) to 58-62HRC, and case depth is .020-.030. Core hardness 40HRC. Each retention knob is coated utilizing a hot black oxide coating to military specifications. Our retention knobs are 100% covered in black oxide to prevent rust. All retention knob surfaces (not just mating surfaces) have a precision finish of 32 RMA micro or better: ISO grade 6N. Each retention knob is magnetic particle tested and tested at 2.5 times the pulling force of the drawbar. Certifications are maintained for each step in the manufacturing process for traceability.