VulcanForms Announces Capital Raise of $355 Million and Pioneers Industrial-Scale Digital Manufacturing Infrastructure
-Next generation manufacturing facilities use breakthrough 100-kilowatt laser additive manufacturing technology, automated machining, integrated robotics, and a proprietary digital thread -VulcanForms serves leading defense, aerospace, medical, and semiconductor companies, supplying precision engineered components and assemblies
VulcanForms, a MIT-born company that builds and operates advanced digital manufacturing infrastructure, announced today it has raised $355 million and is valued at over $1 billion. VulcanForms' investors include Eclipse Ventures, Stata Venture Partners, Fontinalis Partners, D1 Capital Partners, Standard Investments, Atlas Innovate, Boston Seed Capital, Industry Ventures, and the Simkins Family. The company also revealed its first two digital production facilities, in Devens, MA and Newburyport, MA, capturing the full value chain for precision metal components and assemblies.
VulcanForms is enabling its customers in critical industries to accelerate innovation, and to shift away from dependence on overseas manufacturing. The Devens' facility, VulcanOne, is powered by a fleet of VulcanForms' proprietary 100-kilowatt class laser powder bed fusion additive manufacturing systems, which will total over 2 megawatts of laser capacity. The Newburyport facility focuses on automated precision machining and assembly operations. Merging these technologies with a digital thread, VulcanForms offers groundbreaking, U.S.-based digital manufacturing infrastructure to its customers.
Manufacturing must catalyze innovation and sustainable economic growth in the United States
Manufacturers perform nearly 60% of U.S. private sector R&D, and every dollar spent on manufacturing contributes an additional $2.79 to the U.S. economy, a higher multiple than that of any other industry. Manufacturing has raised the standard of living, quality of life, and life expectancy of virtually everyone alive today. It has driven innovation like no other industry. Yet, manufacturing employment in the U.S. has dropped over 40% since 1980, while wages and capital investment have been largely stagnant. Responsible for this catastrophic development is decades of offshoring, displacing critical manufacturing know-how, and infrastructure to other countries. In many cases this enabled access to lower-cost labor and expanded global trade, but ultimately hollowed out the domestic innovation ecosystem. While millions of manufacturing jobs were eliminated, supply chains became increasingly sensitive to geopolitical dynamics.
Today, offshored manufacturing is not coming back in its analog form. Digital-first production technologies, including additive manufacturing, enable more innovative, resource efficient, and resilient supply chains. VulcanForms is pioneering an integrated production system enabling digital technologies to deliver sustainable, high growth impact at scale.
"By scaling advanced digital manufacturing, we can create a new era of U.S. innovation and economic growth," said VulcanForms Co-Founder, President & CEO Martin C. Feldmann. "We've recognized a game-changing opportunity when additive manufacturing technology is scaled for industrial production and is seamlessly integrated with automated machining and robotics. VulcanForms has built the physical infrastructure and digital workflows to deliver this full-stack manufacturing solution at unprecedented speed, precision, quality, and scale. Our technologies combined with our team of engineering and operations leaders from Google, General Electric, Pratt & Whitney, Precision Castparts, IPG Photonics, Faro Technologies, Schlumberger, Alcoa, Autodesk, among others enable our customers to innovate, grow and deliver sustainable impact faster."
Building the future of manufacturing - Delivering today
VulcanForms' customers include leading companies in the aviation, space, defense, medical, semiconductor, and other critical industries. For instance, the company supplies over a dozen U.S. Department of Defense programs, including the F35 Joint Strike Fighter and Patriot Air Defense System, has delivered thousands of components for the semiconductor industry, and is enabling innovation in medical implants. By combining its breakthrough technology, a data- and simulation-based digital thread, and operational excellence, VulcanForms' integrated approach allows its customers to innovate faster and produce more without the need to make major capital investments and implement new manufacturing technologies from scratch.
"VulcanForms brings forth metal additive manufacturing as a scalable industrial process, and as a cornerstone of breakthrough digital production systems," said VulcanForms Co-Founder John Hart, also a Professor of Mechanical Engineering at MIT. "Integrated digital production facilities are critical infrastructure which will accelerate domestic and global innovation and draw top talent to the manufacturing sector."
VulcanOne - The world's highest throughput laser metal additive foundry
The VulcanOne facility in Devens, MA combines VulcanForms' proprietary AM technology with a digital thread, spanning advanced simulation, in-process sensing, and machine learning algorithms that ensure the highest level of quality and precision. In full, VulcanOne will be powered by a fleet of VulcanForms' 100-kilowatt class laser printing systems, representing 2 megawatts of laser power, a capital investment exceeding $100M, and more than 100 new manufacturing jobs on site. VulcanForms also seamlessly integrates additive production at scale with heat treatment, precision machining, assembly, and inspection. To this end, the company has expanded its capabilities through the acquisition of Arwood Machine Corporation in Newburyport, MA. This end-to-end approach enables VulcanForms to deliver engineered components and assemblies, designing and operating a digital-first process chain tailored to each customer's needs.
"There is a fundamental shift in the ways manufacturers need to adapt to global supply chain challenges and the increasing demands for product design flexibility. VulcanForms' full stack approach to deliver an engineered solution, combining advanced additive and subtractive technologies merged through a digital thread will revitalize U.S. manufacturing and hardware innovation," said Greg Reichow, Partner at Eclipse Ventures and Director of VulcanForms. "The technologies that enable this agile workflow will dramatically impact the way products are imagined, designed, built, and delivered for decades to come."
About VulcanForms
VulcanForms builds and operates advanced digital infrastructure enabling the world's critical industries to innovate, grow, and deliver sustainable impact. Founded in 2015 by Martin C. Feldmann and Professor John Hart, of MIT, VulcanForms invented and commercialized the world's first industrially scalable laser metal additive manufacturing (AM) solution and pioneered integrated digital production systems. The company has grown to over 300 employees and has attracted world class engineering, operations, and commercial leaders from Google, General Electric, Pratt & Whitney, Precision Castparts, IPG Photonics, Faro Technologies, Schlumberger, Alcoa, Autodesk, among others. VulcanForms' investors include Eclipse Ventures, Stata Venture Partners, Fontinalis Partners, D1 Capital Partners, Standard Investments, Atlas Innovate, Boston Seed Capital, Industry Ventures, and the Simkins Family. For more information, visit www.vulcanforms.com/.
Featured Product
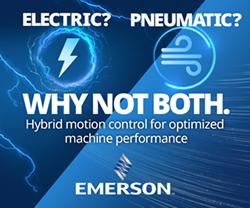