While so much of the occupational health and safety (OHS) industry these days is about being proactive and recognizing and then hopefully eliminating hazards before they can even become an issue, accidents do still happen. And when they do, everyone needs to be prepared.
4 Easy Steps to Successful Incident Management
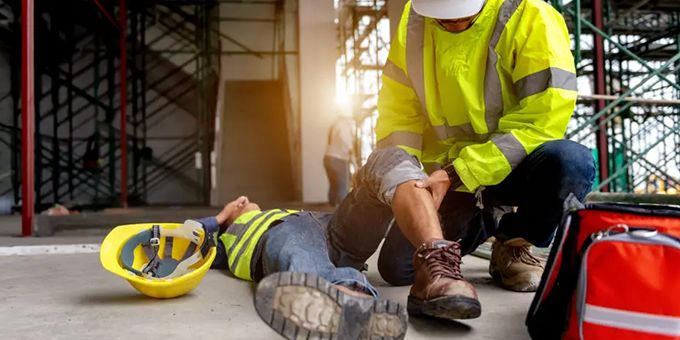
Article from | Safety Skills
While so much of the occupational health and safety (OHS) industry these days is about being proactive and recognizing — and then hopefully eliminating — hazards before they can even become an issue, accidents do still happen. And when they do, everyone needs to be prepared.
This means understanding what needs to be reported, how, and to whom. Complete and accurate reporting ensures the incident is resolved properly. It also helps to show where additional training or safety precautions may be needed.
Unfortunately, not all companies have clear and consistent incident management procedures. There are certain steps that must be taken and all employees should receive training in this area. After all, you never know who might be involved in an incident, and therefore who might need to make the official report.
Report the Incident
For our purposes, let’s define what exactly an “incident” is. In OHS, an incident describes an unplanned event resulting in any type of injury or illness to a person, or property or environmental damage.
An incident can also include near-misses, which are events that don’t result in an injury but could have. These, along with safety observations, should also be reported because it is just as important to learn from potential incidents.
The initial report of an on-the-job incident should be fairly straightforward. Unfortunately, not all companies have an incident reporting form (IRF) ready and available, and those that do may fail to train all employees on how to fill out the form they do have.
The exact IRF used might not be identical from company to company, but there is some information that should be included no matter what, such as detailing the job activity that was taking place, the working conditions at the time and listing all employees that were involved.
Begin the Investigation
This next step, logically, builds off the IRF. The initial incident report includes information only from the perspective of the reporter. During the investigation, that information needs to be corroborated and substantiated.
For some incidents, this step will be fairly quick, while other times the investigation may be more complex and time consuming. It all depends on the details of the incident in question — the more persons affected or the greater the damage done, the longer investigation will likely take.
Some things the investigator will be doing include:
- Documenting all involved personnel
- Detailing any property or environmental damages
- Gathering witness statements
- Providing photos or videos of the scene
Don’t be discouraged by the potential complexity of this step. It is crucial for the details of any incident to be documented clearly and accurately. Otherwise, the next steps of the incident management process will likely not be accurate either and, therefore, potentially not even useful.
Conduct an Analysis
The third step is to analyze the findings of the investigation through a root cause analysis (RCA). There are dozens of RCA methods in use today, but the most common, especially in the health and safety industry, are the fishbone diagram and the five whys.
A fishbone diagram, also known as an Ishikawa diagram or a cause-and-effect diagram, is helpful when conducting a root cause analysis because it makes it easy to visually group potential causes (of the incident) into different categories.
There are three main models used within a fishbone diagram:
- The 4 Ss
- Surroundings, suppliers, systems, skill
- The 6 Ms
- Manpower, method, machine, material, mother nature, measurement
- The 8 Ps
- Product, price, place, promotion, people, process, physical evidence, performance
Completing a fishbone diagram can help you dig through all the causal factors that contributed to the incident and decide which are significant (those that you can control) and which are not significant (those that you cannot control).
In theory, only the significant factors are the ones you should really worry about. After all, if it is something you cannot control, it is probably something that doesn’t have an actionable item to take to avoid a similar incident in the future.
While a fishbone diagram helps to determine potential causal factors, the five whys serve to find the hidden causes of those significant factors. This root cause analysis technique is as straightforward as it sounds: For each signification factor, repeat the question “Why?” Each answer forms the next question, and after “five whys” the base cause should be clear.
This may sound silly, but many of us use the five whys method daily, without even thinking about. For example, maybe one day you went outside and your car wouldn’t start. It is likely you conducted your own root cause analysis and didn’t realize it.
The problem is that the car wouldn’t start.
- Why? The battery is dead.
- Why? The alternator is not working.
- Why? The alternator belt is broken.
- Why? The alternator belt is old and needed to be replaced.
- Why? The vehicle was not correctly maintained and routinely serviced.
Now, completing the five whys for factors of an on-the-job incident may take a little more brainstorming than this, but finding the root cause may very well be this simple.
And once you have determined why something happened, you are ready to decide how to try and prevent it from happening again.
Create Next Steps
The ultimate purpose of the initial report, the investigation and the multi-step analysis is to identify any corrective and preventive actions (CAPAs) needed to prevent similar incidents from happening in the future.
First, you need to understand what CAPAs actually are. A corrective action is reactive and is intended to fix the situation in question. For instance, if an overhead crane falls because an old chain breaks, you replace the chain.
A preventive action is proactive, to ensure the incident, and those like it, don’t happen in the future. In our example, you could create a standard operating procedure to inspect all chains in the facility at regular intervals.
So how do you decide which CAPAs to assign to the identified root causes? Of course, the specific actions you choose to take will be based on your specific needs, but CAPAs will fall within the hierarchy of hazard control.
Here is a breakdown of the hierarchy of hazard controls, from most effective to least effective:
- Elimination consists of physically removing the hazard. For instance, if employees are working high above the ground, move the piece they are working on to ground level.
- Substitution replaces something that produces a hazard with something that does not. A common example is the use of titanium dioxide instead of lead-based paint.
- Engineering controls isolate people from hazards but do not eliminate the hazards themselves, such as adding guard rails rather than invest in fall arrest systems.
- Administrative controls change how people work in order to limit exposure to hazards. This ranges from installing warning signs to implementing procedural changes.
- Personal protective equipment (PPE) reduces exposure to hazards when engineering and administrative controls are not feasible or effective. PPE is needed whenever there are hazards present.
Despite being at the bottom of this hierarchy, personal protective equipment is often much easier to implement than other controls and various types of PPE can be easily utilized in a number of workplace scenarios.
After the Investigation
Once you have completed a full investigation, identified what went wrong and determined how to proceed in the future, be sure you communicate your findings and decisions. After all, if not everyone is aware of the CAPAs put in place, there is still a risk of the same incident occurring again.
Also remember that safety training is, in many instances, a viable and very effective preventive action. Employees can be trained on the uses of PPE, how to safely operate machinery, the risks of working with electricity, and hundreds of other topics.
Contact SafetySkills today to see how we can help your organization prepare for the inevitable day you need to deal with an on-site incident.
The content & opinions in this article are the author’s and do not necessarily represent the views of ManufacturingTomorrow
Comments (0)
This post does not have any comments. Be the first to leave a comment below.
Featured Product
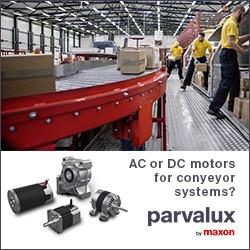