LMI TECHNOLOGIES LAUNCHES NEXT-GENERATION SMART VISION ACCELERATOR TO SUPPORT ITS INDUSTRY-LEADING 3D SMART SENSOR LINEUP
GoMax® NX delivers massive GPU-driven data processing power to any Gocator® 3D smart sensor or multi-sensor network for increased performance in data-heavy inspection applications.
January 20, 2022, Vancouver, BC - LMI Technologies (LMI), the global leader in 3D scanning and inspection, is pleased to announce the official release of our GoMax® NX Smart Vision Accelerator. GoMax® NX is a compact, fanless, high-performance embedded device that allows you to accelerate any Gocator® sensor or multi-sensor network in heavy-duty inspection applications that require increased data processing power.
Benefits of acceleration with GoMax NX:
• Easy to set up, power, and run using the Gocator® web browser interface
• Add GPU-accelerated data processing power to Gocator® 3D laser profilers and snapshot sensors
• Simultaneously accelerate Gocator® multi-sensor networks
• Add multiple GoMax® NX units to scale up sensor network acceleration
GoMax® NX enhances data processing power in real-time, minimizing cycle times and augmenting overall inspection performance so customers can achieve optimal results.
Suitable applications for acceleration with GoMax® NX include:
1 Multi-Sensor Ring Scanning - Gocator laser line profilers in ring layout scanning composite flooring.
2 Robot-Mounted Weld Inspection - Automotive weld inspection using Gocator snapshot sensors mounted on a robot, inspecting various points around the frame of the vehicle.
3 EV Battery Foam Inspection - Volumetric measurement and quality inspection of EV battery protective foam with Gocator snapshot sensors.
"Users can simply connect GoMax® NX to any Gocator® sensor and use the intuitive web browser-based interface to activate sensor acceleration. And, now equipped with the NVIDIA® Jetson® Xavier™ NX system-on-module, this next-generation smart vision accelerator provides more low-latency processing power to your automated inspection applications than ever before", said Robert Uebbing, Technical Product Manager, LMI Technologies.
The GoMax® NX is now available for order at orders@lmi3.com. Write to contact@lmi3d.com for any questions you have regarding this new product.
For additional information on this new vision accelerator, visit the GoMax® NX product page on our website.
About LMI Technologies
As the global leader in 3D scanning and inspection, LMI Technologies works to advance quality and productivity with 3D sensor technology. Our award-winning, FactorySmart® laser, snapshot, and line confocal sensors improve the quality and efficiency of factory production by providing fast, accurate, reliable inspection solutions that leverage smart 3D technologies. Unlike contact-based measurement or 2D vision, our non-contact solutions add 3D shape information that is critical to achieving 100% quality control.
To learn more about how LMI's inspection solutions can benefit your business, we invite you to contact us at contact@lmi3d.com or visit us at www.lmi3d.com to explore the possibilities of smart 3D technology.
Featured Product
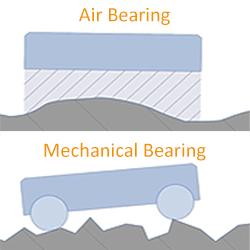