HUBER+SUHNER launches lightest and most compact cable yet, revolutionising offshore connectivity
HUBER+SUHNER has today launched its fire-resistant RADOX® OFL cable solution
HUBER+SUHNER, leading manufacturer of components and system solutions for electrical and optical connectivity, has today launched its fire-resistant RADOX® OFL (Oil & Gas Flexible Lightweight) cable solution - providing the offshore industry with a safe way to reduce platform weight.
Featuring a lightweight and compact design, the RADOX OFL cables reduce weight and space by up to 60% when compared to other cables on the market. The cable's small bend radius and thin wall - which is half the size of standard cables - reduces stripping time by 60%, making installation easier and quicker. This has the potential to save industrial and offshore facilities several hundred thousands of dollars in structural design by overcoming space and weight restrictions.
The RADOX OFL cable is highly fire-resistant and low smoke halogen free (LSFH), which provides exceptional performance in harsh outdoor environments and offshore industrial applications. Core cables do not melt or drip in the event of a short circuit, ultimately minimising emergency repairs and the potential for hazardous fume inhalation. The RADOX OFL cable is also oil, mud and hydraulic oil resistant according to the highest standard NEK606 Cat. a-d.
In addition, the RADOX technology offers a 120°C sheath and 145°C core temperature threshold, giving the cable an expected lifetime which is eight times longer than standard 90°C offshore cables. With RADOX technology, the polymers in the insulation of the wires and in the cable sheath are cross-linked using electron beams. This transformation provides the cables with extreme resistance to mechanical, chemical, temperature and weather influences.
Frank Thorn, Head of Market Unit Industry, Low Frequency division of HUBER+SUHNER said: "The offshore industry presents challenging conditions, including high temperatures, oil, chemicals and UV radiation. This means cables have to be robust and stand the test of time. The latest RADOX OFL cable does exactly this, while also reducing installation time and reducing weight, making it a valuable investment that can future-proof offshore connectivity."
As a result of the RADOX OFL cable's smaller 3D diameter, smaller cable accessories such as connectors and trays can also be used, further reducing space, weight and cost. The cable is ideal for monitoring and control, as well as sensor applications on offshore platforms.
Thorn added: "Offshore applications require durable, flexible and reliable cables that can operate seamlessly and withstand harsh environments to avoid deterioration. We developed the RADOX OFL cable with weight, space and cost in mind, creating a solution which is resilient, cost-effective and quick to install. As a result, the RADOX OFL cables will show no sign of any brittle breakage even after 10 to 12 years, unlike conventional rubber cables."
HUBER+SUHNER has used RADOX technology successfully since the 1970s to achieve notable improvements in the thermal, mechanical and chemical properties of the cable insulation material. The technology has been used in offshore, railway and other industrial applications and has made significant strides in setting new standards of high-quality connectivity performance in various industries worldwide.
The RADOX OFL cable is now widely available and can be found online along with the full specifications here: https://www.hubersuhner.com/en/onepager-minimicrosites/radox-ofl-instrumentation-cable.
For more information about the HUBER+SUHNER RADOX® technology, please visit: hubersuhner.com.
Featured Product
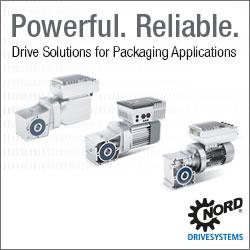
NORD Delivers Powerful, Reliable Drive Solutions for Demanding Packaging Applications
When you need quality, flexibility and high efficiency, NORD has you covered with complete drive solutions for primary and secondary packaging, end-of-line packaging, and higher-level applications. NORD supports you through the entire life cycle of your drive systems with pre-sales engineering support, online tools, and a global service network. Drive systems for both vertically and horizontally networked technology with all the options for sensor incorporation and integration into the higher-level control system.