By investing in ERP technology, companies can not only survive but thrive in the face of a shrinking labor pool. As the Deloitte report suggests, "Rethinking work models is essential to predict the unpredictable,"
Bridging the Gap: Leveraging an ERP/MIS to Mitigate Skilled Labor Shortages
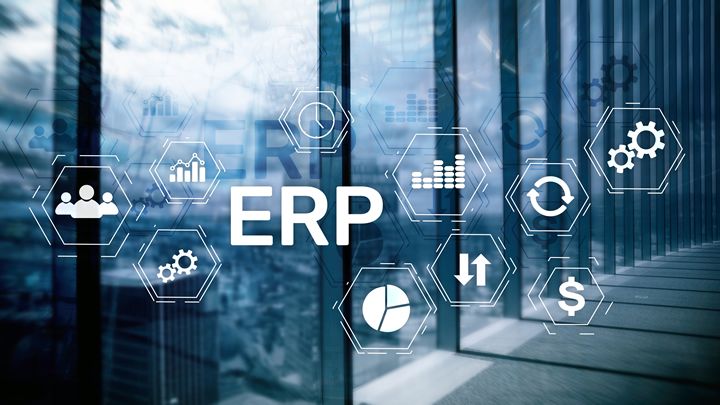
Article from | HiFlow Solutions
The skilled labor shortage has become a significant challenge across various industries, with sectors like manufacturing, logistics, and packaging feeling the impact most acutely. As the demand for skilled labor continues to outpace supply, organizations are increasingly turning to technology to fill the gap. Among the technological solutions, software systems such as ERP/MIS have emerged as a powerful tool to address these challenges. This article delves into how implementing these systems can mitigate the skilled labor shortage, enhance workforce efficiency, and future-proof businesses.
Understanding the Skilled Labor Shortage
The skilled labor shortage is not a new phenomenon but has intensified in recent years. According to a report by Deloitte, the manufacturing sector alone could face a shortage of 2.1 million skilled jobs by 2030, resulting in a potential economic loss of $1 trillion if the gap is not addressed. This shortage is driven by multiple factors, including an aging workforce, a lack of interest in trades among younger generations, and the rapid pace of technological change outpacing skill development.
The Role of ERP Systems in Addressing Labor Challenges
ERP/MIS systems offer a comprehensive solution to the skilled labor shortage by integrating various business processes into a single, unified system. This integration allows for better resource management, improved decision-making, and enhanced operational efficiency. Here’s how ERP systems can specifically address the labor shortage:
Controlling labor hours by providing real-time visibility
One strategy organizations can use to mitigate labor shortages is to control labor hours and potentially reduce hours. An ERP/MIS can help in a big way by providing real time visibility into a plant’s workforce on the shop floor, in the warehouse.
Real-Time Monitoring: Supervisors can monitor employee attendance and productivity in real time, allowing them to address any issues immediately.
Capacity Planning: The system can assess current workforce capacity against production demands, helping management plan for future hiring or temporary staffing needs.
Direct Labor Cost Tracking: ERPs track labor costs by associating labor hours with specific production jobs or work orders. This helps in calculating the direct labor cost per unit of production and identifying areas where costs may be too high.
Overtime Management: The ERP/MIS system can monitor overtime hours and costs, enabling management to make informed decisions about whether to allocate additional labor or find efficiencies to reduce overtime.
Demand-Based Scheduling: ERP systems can use production forecasts and historical data to optimize labor schedules, ensuring that workers are allocated efficiently based on current demand.
Skill-Based Assignment: ERPs allow for the assignment of tasks to employees based on skill levels, ensuring that the right people are in the right roles, reducing inefficiencies and rework.
Productivity Reports: An ERP/MIS can generate detailed reports on individual and team productivity, showing how many units are produced per hour worked. This helps in identifying top performers and those who may need additional training or support.
Automating Routine Tasks
One of the primary benefits of ERP/MIS systems is their ability to automate routine tasks, reducing the dependency on manual labor. In industries like manufacturing and logistics, where repetitive tasks are common, automation can significantly reduce the need for skilled labor. According to a report by Packaging Impressions, automation not only addresses labor challenges but also improves profitability by streamlining operations .
By automating tasks such as inventory management, order processing, and scheduling, ERP systems free up skilled workers to focus on more complex, value-added activities. This shift not only enhances productivity but also helps retain employees by reducing the monotony of their work.
Managing Shop Floor Workers
ERP systems provide advanced workforce management tools that help companies optimize the allocation of their existing labor force. Modern labor management systems are integrated within ERP platforms, offer real-time insights into workforce performance, allowing managers to adjust workloads, shifts, and assignments dynamically.
ERP systems can help identify which operators, for example, are the most efficient and which may need more training. This proactive approach to skill development ensures that employees are continually evolving alongside technological advancements, making them more valuable to the organization.
In the face of a skilled labor shortage, making informed decisions is crucial. ERP/MIS systems offer robust data analytics capabilities that provide insights into every aspect of the business, from supply chain efficiency to workforce productivity. With access to real-time data, managers can make better decisions regarding labor allocation, process improvements, and investment in new technologies.
More efficiently managing existing personnel
By monitoring key labor KPIs, manufacturers can make informed decisions that optimize labor utilization, improve operational efficiency, and ultimately increase profitability.
By understanding the true cost of labor for each job, companies can make informed decisions that mitigate the impact of labor shortages. This includes prioritizing high-value jobs, optimizing resource allocation, planning for future labor needs, and making strategic decisions about temporary staffing or outsourcing. Ultimately, this proactive approach helps to ensure that production continues smoothly and profitably, even in the face of labor challenges.
In addition, by analyzing job costs and labor utilization, the ERP/MIS system can help identify and minimize periods of idle time. This maximizes the use of available labor, making the most of a potentially limited workforce.
An ERP system also improves key labor KPIs such as:
- Labor Productivity
- Labor Utilization Rate.
- Overtime Percentage
- Absenteeism Rate
- Employee Turnover Rate
Case Studies: ERP Systems in Action
Several companies have successfully leveraged ERP systems to mitigate the skilled labor shortage. These companies saw an increase in productivity and a significant reduction in labor costs.
"We found that staff productivity per capita increased. In addition, staff can see how much the system improves their efficiency and how much time is saved by automating the most time-consuming activities.” describes Dariusz Makowiak, co-owner of a leading paper products packaging company. “Without the implementation of the HiFlow system, we would have had to hire even more people."
Granpak, a folding carton manufacturer, management uses HiFlow’s MIS/ERP to analyze the performance of individual machines and assess the efficiency of operators. The performance data collected supports continuous improvement initiatives and helps identify training needs for operators.
Conclusion
The skilled labor shortage is a complex and multifaceted issue that requires innovative solutions. ERP/MIS systems offer a comprehensive approach to mitigating this challenge by automating routine tasks, enhancing workforce management, and improving Labor KPIs. As industries continue to evolve, the role of ERP/MIS software systems in addressing labor shortages will only become more vital.
By investing in ERP technology, companies can not only survive but thrive in the face of a shrinking labor pool. As the Deloitte report suggests, "Rethinking work models is essential to predict the unpredictable," and ERP systems provide the foundation for this new approach to workforce management.
In conclusion, ERP systems are not just a solution to the current labor shortage—they are a strategic investment in the future of your labor workforce.
The content & opinions in this article are the author’s and do not necessarily represent the views of ManufacturingTomorrow
Comments (1)
Featured Product
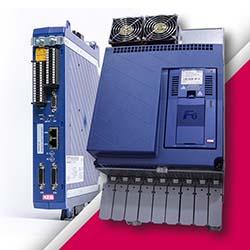