The implementation of MES has paved the way for a more agile, cost-effective, and sustainable future for the architectural millwork and metal fabrication sector.
How MES Software Drives Digital Transformation in Your Manufacturing Operations
Milind Patel, Director of Digital Products and Engineering Services | HitechDigital
Introduction/Overview
The adoption of Manufacturing Execution Systems (MES) has revolutionized the architectural millwork and metal fabrication industry, deeply impacting its efficiency and productivity. MES enables real-time monitoring of production processes, streamlining workflows, and optimizing resource allocation.
This integration of technology has led to enhanced precision, reduced material wastage, and improved quality control in millwork and fabrication workshops.
With MES, manufacturers can easily adapt to changing demands and market trends, staying competitive in a rapidly evolving landscape. The implementation of MES has paved the way for a more agile, cost-effective, and sustainable future for the architectural millwork and metal fabrication sector.
An effective Manufacturing Execution System (MES) is a key step in the digital journey of architectural millwork manufacturers and metal fabricators. It helps optimize production efficiency and enables visualization of the entire value chain with an integrated approach to data management.
Impact of MES on Custom Architectural Millwork Manufacturing and Metal Fabrication Industries
From production planning, order tracking, and quality management to order dispatch, MES streamlines the entire production value chain. Various modules of MES work together to deliver a streamlined production workflow to drive higher efficiencies and better control over operations.
Some major benefits of MES realized by custom millworkers and metal fabricators include:
-
Improved planning, scheduling and dispatching
-
Optimized resource management
-
Higher accuracy in cut lists and material estimation
-
Real-time job tracking
-
Lean inventory management
-
Enhanced quality management
-
Compliance tracking
But first, you should assess how mature is your shop floor and your business processes to adopt the digital transformation that MES drives.
Driving Digital Transformation with MES in architectural millwork manufacturing and metal fabrication
Real-time visibility and control over manufacturing operations:
Real-time visibility and control over manufacturing operations are the defining pillars of a healthy MES. By leveraging advanced data collection across key production metrics, MES provides instant access to critical production data, enabling stakeholders to monitor and analyze processes as they unfold on the shop floor. This real-time insight empowers decision-makers to proactively identify bottlenecks, track production progress, and optimize resource allocation for improved efficiency.
Additionally, MES facilitates rapid response to changing demands, ensuring better coordination between different departments and enhancing overall production agility. With the ability to proactively address issues and make data-driven decisions, manufacturers can achieve higher levels of productivity, quality, and customer satisfaction while staying ahead in today's competitive landscape.
Optimization of production processes and resource allocation
MES play a crucial role in the optimization of production scheduling and resource allocation within the manufacturing industry. Through real-time data collection, analysis, and monitoring, MES enables a comprehensive understanding of production workflows. This valuable insight allows for the identification of inefficiencies and bottlenecks, leading to targeted process improvements and increased productivity.
Furthermore, MES facilitates intelligent resource allocation, ensuring that materials, equipment, and labor are utilized optimally to meet production demands. The ability to dynamically adjust resources based on real-time data enhances responsiveness to changing market conditions, reducing costs and lead times while maintaining high-quality output. By streamlining operations and maximizing resource utilization, MES empowers manufacturers to achieve heightened operational efficiency, competitiveness, and overall success in a rapidly evolving business landscape.
Quality management and traceability enhancement
One of the most important benefits of Manufacturing Execution Systems (MES) is the enhancement of quality management and traceability. By leveraging advanced data tracking and collection capabilities, MES allows manufacturers to maintain meticulous records of production processes, materials, and components used in each product. This end-to-end traceability empowers companies to swiftly and accurately identify the source of any defects or issues, facilitating rapid corrective actions and preventing potential recalls.
Moreover, MES enables real-time monitoring and analysis of quality metrics, ensuring compliance with industry standards and customer requirements. With the ability to trace and monitor product quality from raw materials to finished goods, manufacturers can uphold superior product quality, boost customer satisfaction, and build a reputation for reliability in the market.
Integration of data across the manufacturing ecosystem
Integration of data across the manufacturing ecosystem is a critical aspect of a robust MES. MES serves as a central hub that seamlessly connects various systems, departments, and processes within a manufacturing facility. ERP, PLM, CRM, supply chain software, accounts payable, are some of the many business systems with which an ideal MES is can be integrated.
Through efficient data integration, MES enables real-time information flow, allowing stakeholders to access accurate and up-to-date data from different stages of production. This interconnectedness not only enhances collaboration and communication between teams but also provides a holistic view of the entire manufacturing process.
By breaking down data silos, MES optimizes decision-making, streamlines workflows, and promotes agile responses to production challenges. Ultimately, the integration of data across the manufacturing ecosystem empowers companies to make data-driven decisions, improve overall operational efficiency, and drive continuous improvement throughout the manufacturing value chain.
Facilitating collaboration and communication
For millworkers and metal fabricators, Manufacturing Execution Systems (MES) play a vital role in fostering collaboration and communication within their unique manufacturing environment. With diverse processes and skilled personnel involved in both sectors, MES serves as a centralized platform that connects these teams, enabling seamless information sharing and real-time data access.
Such interconnectedness promotes better coordination between millworkers and metal fabricators, leading to smoother project execution and reduced errors. Collaboration across design, fabrication, and installation teams becomes more efficient, resulting in streamlined workflows and enhanced productivity.
MES also facilitates clear communication between shop floor workers, supervisors, and management, ensuring that all stakeholders are well-informed and empowered to make timely decisions. By promoting effective collaboration and communication, MES empowers millworkers and metal fabricators to optimize their production processes, meet project deadlines, and deliver high-quality results, bolstering their competitiveness in the industry.
Steps to effectively implement MES software in your operations
Steps to effectively implement MES software in millwork and metal fabrication operations can be divided into three essential phases: pre-implementation, implementation, and post-implementation.
Pre-implementation
This phase involves identifying the unique needs and challenges of millworkers and metal fabricators and setting clear goals for the MES implementation. Conduct a thorough assessment of existing processes, workflow bottlenecks, and areas for improvement. Involve key stakeholders from all levels of the organization to gain valuable insights and support. Define specific objectives, such as increasing production efficiency, reducing lead times, and improving quality control. Establish a well-defined roadmap for the implementation process, outlining timelines, budgets, and resource requirements.
Implementation
The next crucial step is selecting the right MES system that aligns with the specific requirements of millwork and metal fabrication operations. Evaluate different software options, considering factors like scalability, customization, and integration capabilities with existing systems. Involve end-users in the selection process to ensure their needs are met and gain their buy-in.
Once the system is chosen, provide comprehensive training to employees, covering all aspects of the software and its functionalities. Encourage open communication and a collaborative learning environment to promote smooth adoption. HitechDigital team ensures that your MES is up and running within 90 days.
Post-implementation
After the MES system is set up and is operational, conduct a thorough assessment of its impact on millwork and metal fabrication operations. Measure KPIs related to productivity, quality, and resource utilization. Analyze the data to identify any areas of improvement or potential challenges. Seek feedback from employees and stakeholders to understand their experience with the new system and address any concerns. Based on the evaluation, make necessary adjustments and optimizations to ensure the MES continues to deliver impactful results and aligns with evolving business needs.
Future of Manufacturing: MES Software and Beyond
The future of manufacturing lies in the transformative power of MES, connected with Industrial Internet of Things (IIoT) and Digital Twins. As industries evolve and technology continues to advance, this convergence will transform modern manufacturing.
With MES's real-time data integration and IIoT's interconnected network of devices, manufacturers achieve high visibility and granular control over their production processes. This promotes seamless collaboration, optimized workflows and better resource allocation. Moreover, the integration of Digital Twins, virtual replicas of physical assets digitally interconnected to the asset systems, empowers manufacturers to simulate and optimize processes, predict maintenance needs, and detect potential issues before they occur.
As MES, IIoT, and Digital Twins evolve further, they will enable manufacturers to drive even greater efficiencies, predictive maintenance, and smarter decision-making. By embracing these cutting-edge technologies, manufacturers can embark on a path towards sustainable growth, agility, and unmatched competitiveness in the dynamic and ever-evolving world of manufacturing.
Where Are You in Your Digital Transformation Journey
At the Exploring level, end user organizations possess basic, yet often isolated MES applications with limited data integration. As they progress to the Limited level, these organizations establish basic MES functionality, now with limited visualization, in one or two plants. With improved data integration, they experience fewer data and functional silos, leading to enhanced interoperability between applications.
Moving towards the significant MES implementation level, MES functionality expands across entire plants, and sometimes multiple plants within the enterprise are interconnected. This level sees extensive integration of MES solutions with manufacturing-related data sources, granting heightened visibility into production and supply chain processes.
Advancing to the Proficient level, organizations bolster their visualization capabilities and integrate newer, advanced digital features like AI, ML, digital twins, robotics, and cutting-edge digital sensors. These capabilities may be deployed on premise, in the Cloud, or at the edge, as deemed suitable. Best in Class organizations push the boundaries further by refining and expanding these capabilities to enable enterprise-wide visibility and collaboration. In terms of MES, this signifies a highly mature stage of digital transformation.
Final Word
MES software is the driving force behind the digital transformation in architectural millwork and metal fabrication operations. Throughout this article, we've seen how MES brings numerous benefits to these industries. It optimizes production processes, improves resource allocation, and enhances quality management and traceability.
From the exploring to the proficient level, MES takes millworkers and metal fabricators on a journey towards increased maturity and competitiveness. Looking ahead, the future of MES is even more promising with the integration of IIoT and Digital Twins, providing efficiency and predictive capabilities like never before. So, if you're in architectural millwork or metal fabrication, embracing MES is a must for sustainable growth and success in today's rapidly evolving manufacturing landscape. Embrace MES now and thrive in the era of digital transformation.
About Milind Patel
Milind Patel is the Director of Digital Products and Engineering Services at HitechDigital. He has 23 years of experience in leading managed services, global delivery, and program management. He has a thorough understanding of software development lifecycles, and has expertly executed many projects, from planning to delivery. Proficient in waterfall and agile methodologies, he is recognized as a go-to digital transformation expert for a broad range of industries.
The content & opinions in this article are the author’s and do not necessarily represent the views of ManufacturingTomorrow
Comments (0)
This post does not have any comments. Be the first to leave a comment below.
Featured Product
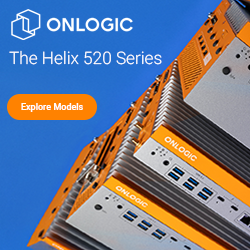