It’s crucial to prioritize data management before jumping into implementing analytics. Because different departments and processes produce different data types, a common data language is a good place to start to help structure the data and break down silos.
The Use of Gearboxes in Warehouse Automation
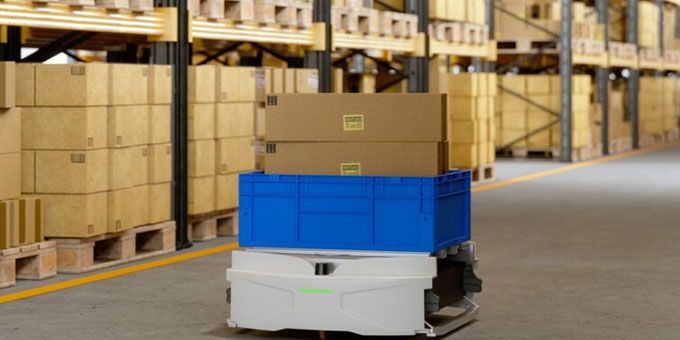
Article from | Parvalux Electric Motors Ltd
In the rapidly advancing world of warehouse automation, smart manufacturing and other intralogistics movements of goods, precision, efficiency, and reliability are paramount. A recent study by Warehouse Automation (2022), has indicated the global market for automation would rise by as much as 19% between 2024 and 2027. Therefore ensuring that automation is carried out efficiently and accurately is key in this environment.
Automated Guided Vehicles (AGVs) and pallet and tray shuttles play a pivotal role in streamlining warehouse operations and enhancing productivity. However, there is one crucial component that drives the smooth functioning of many automation systems: the gearbox.
The gearbox serves as a critical interface between the motor and the driven equipment, enabling torque conversion and speed control. However, it is also essential that the gearbox is quiet, has a high torque density, high precision, high radial load and high rigidity to enable a long-life span for the equipment.
The Importance of Gearboxes in Warehouse Automation
Warehouse automation has revolutionized logistics and supply chain management by introducing precision, speed, and error reduction in various tasks. AGVs and pallet and tray shuttles form the backbone of these automated systems, performing tasks such as material handling, goods transportation, and storage.
To execute these tasks effectively, these machines require controlled power transmission to ensure smooth movements and accurate positioning. This is where gearboxes come into play and they serve two primary purposes.
- Torque Conversion – Gearboxes allow for the conversion of high-speed, low-torque rotational energy from the motor into low-speed, high-torque output suitable for driving heavy loads and overcoming resistance.
- Control – Gearboxes enable precise speed control of the driven equipment. In warehouse automation, where precise positioning and synchronization are essential, the gearbox allows for fine-tuning the movement of AGVs and shuttles, ensuring accurate delivery and storage of goods.
It’s important that the gearboxes chosen have a number of features as standard when being implemented into warehouse automation. These include:
- Fitting within a small space envelope
- Withstanding high torque density
- Having a low backlash
- Demonstrating high rigidity and radial load capacity
- Being designed to be maintenance-free to reduce downtime
Automated Guided Vehicles (AGVs) and Gearboxes
AGVs are autonomous vehicles designed to navigate and transport goods within a warehouse or manufacturing facility without human intervention using opto-guiding systems (lines on the floor), or AMRs (Autonomous Mobile Robots) use electronic systems such as lidar or ultrasonic. Therefore, these vehicles rely on sophisticated systems to navigate through the facility and follow predefined paths, smoothly and safely.
The GB58 gearbox from Parvalux is particularly well-suited for application in AGVs, providing several advantages:
- Compact Design – The GB58 gearbox boasts a compact and lightweight design, making it an ideal choice for AGVs which rely on limited space for mechanical components. The small footprint allows AGVs to carry more payload while maintaining overall efficiency and agility even whilst operating around the clock.
- Customisability – Parvalux’s GB58 gearbox is highly customisable, allowing AGV manufacturers to tailor the gearbox’s gear ratios and mounting options to match the specific requirements of their vehicle. This customisation ensures optimal performance and seamless integration with the AGV’s motor and control system.
- High Efficiency – Efficiency is crucial in AGVs to maximize battery life and reduce operating costs. The GB58 gearbox’s precision engineering and quality materials contribute to high efficiency, minimizing power losses during transmission and enhancing the overall performance of AGVs.
- Reliability – AGVs operate in demanding environments and are subject to frequent starts, stops, and changes in direction. The GB58 gearbox’s robust construction ensures durability and reliability, reducing maintenance requirements and downtime for AGV fleets.
Pallet and Tray Shuttles and Gearboxes
Pallet and tray shuttles are innovative warehouse automation solutions designed to optimize storage and retrieval processes. These automated systems enable efficient utilisation of vertical space within a warehouse by automatically moving and positioning pallets or trays within high-rise storage structures. There are numerous benefits of choosing the Parvalux GB58 within this context including:
- Quiet and Smooth Operation – The GB58 gearbox is engineered to operate with reduced noise levels and low vibration which are key to creating a conducive working environment and causing minimal disturbance to nearby staff.
- Durability for High-Cycle Operations – The GB58 gearbox’s durable construction and high-quality components enable it to withstand the demands of high-cycle operations such as frequent storage and retrieval operations throughout the day, ensuring consistent performance and longevity.
- Integrated Motor Solutions –- Parvalux’s GB58 gearbox can be paired with specially designed motors to create compact and integrated drive solutions. This integration simplifies the design and assembly process, resulting in reduced installation time and system costs.
There are many benefits to warehouse automation ranging from more accuracy, improved employee efficiency, increased warehouse productivity, a reduction in health and safety issues, reduced processing time and a better use of space within the warehouse environment. All of these benefits can in time improve the profitability of the business with reduced operational costs as well as making it easier for your manufacturing operation to grow and to weather economic storms as they arise. However, this is reliant on the equipment that is installed and the choice of gearbox that is used.
If you are looking for a gearbox solution for warehouse automation systems then Parvalux’s GB58, which we pride ourselves on for its versatility and suitability in AGVs and pallet and tray shuttles could be the most appropriate solution for you.
We also have extensive experience designing AGV motors and offer a range of standard motors and gearboxes as well as offering a high degree of customisation if required. To find out more head over to the GB58 product page here.
The content & opinions in this article are the author’s and do not necessarily represent the views of ManufacturingTomorrow
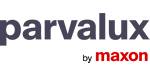
Parvalux Electric Motors Ltd
Parvalux is a leading global manufacturer of geared motor solutions with over 70 years' experience in creating the perfect combination of motor and gearbox to match the customer's application. Whilst we offer thousands of standard options we can easily customize any motor or gearbox to meet your exact requirements at no or minimal extra cost. Our design team can work closely with your own to optimize your solution for your application helping you to secure a genuine competitive advantage in your market. Our products are found in hundreds of applications but we are particularly strong in healthcare, leisure, mobility, transport, and a diverse range of industrial applications.
Other Articles
How Parvalux Is Helping to Develop the Next Generation of Conveyor Systems
The Role of Conveyor Systems in Warehouse Logistics
6S In Manufacturing
More about Parvalux Electric Motors Ltd
Comments (0)
This post does not have any comments. Be the first to leave a comment below.
Featured Product
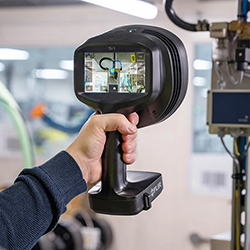