The medical device manufacturing sector faces many challenges with respect to their daily operations such as: data collection and reporting, downtime tracking, real-time visibility and shop floor engagement.
The Importance of Digitization for Medical Device Manufacturers
Article from | RAVEN
Medical Technology Today and The Impact on Medical Device Companies
Manufacturing Pain Points in the Medical Device Sector
The medical device manufacturing sector faces many challenges with respect to their daily operations such as: data collection and reporting, downtime tracking, real-time visibility and shop floor engagement. Let’s take a look at the factors that are causing these challenges to turn into major pains for some manufacturers in this space.
Plant Management and Continuous Improvement Teams
- Lack of real-time visibility into machine and people productivity due to spreadsheets and whiteboards
- Lengthy processes for handling unplanned downtime
- Long changeover times and slow startups dependent on operator training
- Manual data collection processes or inadequate digital solutions leading to incomplete, inaccurate data
- Insufficient reporting to detect, identify and mitigate production and quality-related issues
- Poor decisions due to lack of contextualized data
- Manually tracking downtime reasons, disrupting work and resulting in disengagement with shop floor processes
- None to minimal visibility on operational metrics and lack of real time recognition and feedback on performance
- Inability to make productivity improvements on the fly and hit targets
- Disorganized data collection processes resulting in lack of communication and knowledge sharing between shifts
- Inefficient processes to call for help and alert the supporting teams
- None or minimal access to the right data to understand how plants are performing to boost operational excellence
- Unknown or inaccurate data and losses increasing production costs
- Staying up-to-date and communicating the need to adapt to quality and regulation changes across the organization
If these challenges aren’t prioritized, they can cost medical device manufacturing companies billions in lost revenue. In fact, McKinsey stated that facilities adopting AI and other advanced Industry 4.0 technologies by 2025 can expect a 122% positive cash flow change. Follower companies can expect just 10%, while companies that fail to adopt AI could see a 23% downturn.
Strategies for Increased Productivity and Maximizing ROI
- 30-50% reductions in machine downtime
- 10-30% increases in throughput
- 15-30% improvements in labor productivity
- 85% more accurate forecasting
OEE Software to Drive Productivity Improvements
- Automating downtime labeling so frontline teams can remain focused on hitting targets
- Eliminating manual work for shop floor data collection and reporting
- Offering user-friendly dashboards and easy-to-use functionalities that ensure even a non-technical person can learn it; and
- Enabling confident, data-led decisions for continuous improvement across plants
- Ensuring that every medical appliance designed on the shop floor meets strict regulations
- Ensuring sufficient reporting to detect, identify and mitigate quality-related issues
- Providing real-time visibility into production and losses data, promoting coordination and streamlining interdepartmental relations
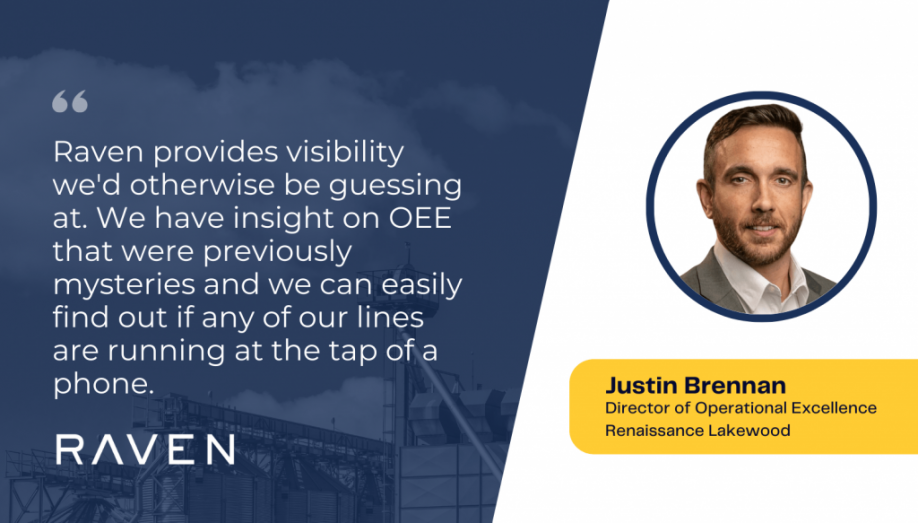
With increasing regulations and objectives in place, it can be overwhelming for medical device companies to know how to optimize their shop floor processes that will lead to productivity improvements. Without clear, contextualized and accurate data, prioritizing their continuous improvement initiatives can seem more challenging than it has to be. By adopting a fully-digitized approach and embracing new tech innovations, medical device companies will increase their ability to adapt to the pressures of producing high-quality, regulatory approved products both safely and efficiently.
The content & opinions in this article are the author’s and do not necessarily represent the views of ManufacturingTomorrow
Comments (0)
This post does not have any comments. Be the first to leave a comment below.
Featured Product
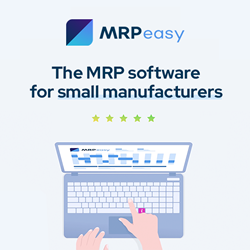