Manufacturers with a digital twin of a prototype can be tested across multiple simulations or designs to reduce the number of physical iterations needed before production or they can be used to analyze product performance.
A Turn Toward Manufacturing Perfection with CNC Digital Twins
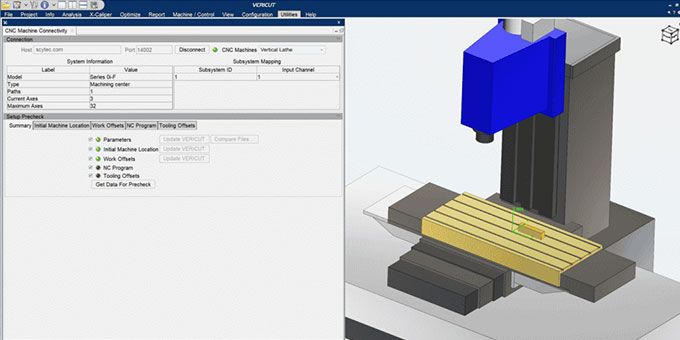
Article from | ShopFloor Automations
The concept of an effective digital twin, or exact replica of your equipment or process on the shop floor, gained notoriety in 2002 despite its early roots in NASA’s space program in the 1960s. Today digital twin creation is happening across manufacturing floors around the world in an effort to speed up and optimize traditional processes. Rather than perform process steps in a particular sequence, manufacturers with digital twins may carry out processes simultaneously for faster results. And there’s plenty of applications for digital twins as well. Manufacturers with a digital twin of a prototype can be tested across multiple simulations or designs to reduce the number of physical iterations needed before production, says the American Society of Mechanical Engineers, or they can be used to analyze product performance, distribution and end-user experience for product design improvements.
Simulating Success
CNC machine simulation software provider CGTech, the makers of VERICUT®, and Scytec, producer of the DataXchange machine monitoring solution, identified another such application for CNC digital twins: quality management. By identifying the presence of variances before production begins on the floor, the partnering companies found that non-conformances and rework can be minimized, if not wholly eliminated. It works like this: CNC machines with modern FANUC oi and 30i series controls are monitored by the DataXchange solution, sending set up information, like main NC programs, subprograms, axis locations, work offsets, and tooling, to compare with VERICUT’s Machine Configuration (VMC) for accuracy verification. Any differences between machine values and simulation values are then updated in the VERICUT simulation to ensure only the intended result. By rerunning the simulation with values from the machine, it’s possible to check that there are no new problems or unexpected errors related to the machine setup.
With this latest DataXchange integration with VERICUT, any differences between actual machine values and simulation values can be updated in the VERICUT simulation to ensure only the intended result.
VERICUT shows material removal at the workpiece level, but it can also simulate entire machine tools as they appear on the shop floor. Its Machine Simulation detects collisions and near-misses between all machine tool components, such as axis slides, heads, turrets, rotary tables, spindles, tool changers, fixtures, work pieces, cutting tools and other user-defined objects. A user can set up near-miss zones around the components to check for close calls, and detect over-travel errors.
Honing Predictive Accuracy
In future releases, the VERICUT integration with DataXchange for CNC Digital Twins is expected to introduce these capabilities:
- Glean post-machining insights to investigate differences between how the part ran on the machine and simulation
- Investigate potential issues that may have caused parts to be out of specification, review any modifications to the NC program subroutines, or feed rates and spindle speeds
- Identify and review any errors or problems that resulted in overrides or emergency stops in real-time
- Compare live cycle times to VERICUT’s predicted run times
Collisions and near-misses between all machine tool components may be recorded in the VERICUT Machine Simulation for refinement opportunities.
The digital twin concept has come a long way since Dr. Michael Grieves first applied it to manufacturing in the early 2000s. But its benefits hold promise, particularly for manufacturers saddled with costly materials, a limited and extended workforce and high customer demands for exceptional quality. To learn more about the VERICUT integration with DataXchange for your manufacturing business, contact a Shop Floor Automations expert today.
The content & opinions in this article are the author’s and do not necessarily represent the views of ManufacturingTomorrow
Comments (0)
This post does not have any comments. Be the first to leave a comment below.
Featured Product
