This article gives a detailed thermoset vs thermoplastic comparison. Although there are many similarities between thermoplastic and thermoset, some differences are also present.
Thermoset vs Thermoplastic: Definition, Processes, and Differences
Leon Huang | RapidDirect
The most common plastic polymers for the injection molding process were thermoplastic polymers. However, another type of plastic surfaced in the manufacturing industry – Thermosetting plastics.
The combination of resins and thermosets serves as an alternative to metal and thermoplastics for plastic fabrication processes. There are situations in which the best materials to use are thermoplastics. Likewise, some situations warrant the use of thermosets. Due to their similarities, some manufacturers use the two materials for the same products.
However, the products should determine the suitable material. Thus, it is necessary to understand the differences between thermoplastic and thermosetting plastic. This article will guide you through the differences to aid better decision-making.
A Brief Overview of Thermoset and Thermoplastic
To better understand the difference between thermoplastic and thermosetting plastic polymers, we must first examine their individual characteristics. Therefore, here is a brief look at what each of them is.
What is a Thermoplastic?
A thermoplastic is a resin that is solid at room temperature. However, it becomes soft upon heating and eventually turns fluid due to crystal melting or crossing of the glass transition temperature. When it comes to processing thermoplastics, there is no chemical bonding involved.
You can easily pour these resins into the mold for cooling and solidifying into desired shapes. Before molding, they are available as pellets. Consequently, you can melt these pellets many times, and you can form different shapes each time. These plastics also enable reheating, recycling, and remolding without posing a risk to material properties.
Thus, you will find these materials used for plastic injection molding, extrusion, and thermoforming processes. They generally tend to resist shrinking and offer good strength and elasticity. What’s more, some thermoplastics common to manufacturers are:
- Acrylic
- Nylon
- Acetal Copolymer Polyoxymethylene
- Acetal Homopolymer Polyoxymethylene
- Polycarbonate (PC)
- Polyethylene (PE)
- Polystyrene (PS)
- Polypropylene (PP)
- Polyvinylchloride (PVC)
- Polyethylene terephthalate (PET)
- Teflon
Each of these thermoplastics has different properties, thus, their uses of these materials vary from industry to industry.
What is a Thermosetting Plastic?
Thermoset plastics or thermosetting polymers are liquid resins at room temperature. These polymers harden upon heating or the addition of chemicals. Besides, thermoset plastics are typically produced with resin transfer molding (RTM) or reaction injection molding (RIM). During this process, crosslinking occurs between the polymers in the material and forms an irreversible and unbreakable bond.
After the initial heat forming process, thermosets are highly resistant to corrosion, heat, and mechanical creep. As a result, they are perfect fits for components requiring high strength-to-weight properties, tight tolerances, and heat exposure.
Thus, when you expose the materials to temperature regardless of the degree, melting will not take place. This helps the material retain its shape after heating and forming specific shapes. However, overheating may cause the materials to degrade while still in the solid phase.
Some thermosets common to manufacturers are:
- Phenolics
- Silicone
- Melamine
- Epoxy
- Polyvinylidene fluoride (PVDF)
- Polytetrafluoroethylene (PTFE)
- Polyurethane
- Polyimide
It is also important to note that there is the possibility of a material to be thermoplastic and thermoset. Polyester is a typical example. Additionally, the storage form of thermosets polymer is liquid, and it is in a large container or tank.
The automotive, lighting, appliance, and energy industries also choose this polymer. This is because they have higher structural integrity and resistance to impact and deformation.
What Are the Main Differences Between Thermoplastic vs Thermoset?
Although thermoplastics and Thermosets are similar plastic polymers in some cases, there is some thermosetting and thermoplastic difference. We will discuss these differences under the following headings:
Melting Point
The major difference between thermoplastic and thermosetting plastic is in relation to their behavior after heating. The melting point of thermoplastics is lower than degradation temperatures, while that of thermosets is higher.
After heating thermoplastic and cooling down while forming the desired shape, it is also possible to subject the product to heat again to form another product. However, the form of a product made from thermosetting plastic will not change after subjecting the initial product to heat.
So, when heated after curing, thermoplastics melt, whereas thermosets do not, and they retain a solid shape. Thus, thermoplastics have a lower melting point compared to thermosets. Recyclable materials are made with thermoplastics since they can melt when subjected to heating.
Aesthetics
Thermoplastics are traditionally popular for a high-quality finish. However, the RIM and RTM processes involving the use of thermoset polymers are unique processes. Accordingly, these techniques offer a unique opportunity that ensures superior aesthetics.
Before injecting the thermosetting plastic into the mold, there is an opportunity to spray directly into the mold. Also, the processes allow for in-mold coating and painting. The in-mold painting process creates strong bonds between the paint and the plastic surface. Because of this, they have excellent adhesion, preventing flaking, chipping, cracking, and other injection molding defects.
Thermosets are also suitable for low- and high-gloss finishes out of the mold at more affordable prices. Painted thermosets can also look like finely detailed textures. Since thermosets provide excellent flowability, they allow even the tiniest of aesthetic touches, including the addition of logos.
Corrosion Resistance
Based on estimation, chemical processing plants incurred high expenditure from corrosion which is up to 10% of the capital. Consequently, one has to consider the effects of corrosion on the material before selecting it. Instead of spending a huge amount of money through losing materials to corrosion, it is essential to use materials resistant to corrosion. While both materials are highly corrosion-resistant, thermoplastics are more resistant to chemical attacks than thermosets.
Durability
Durability and heat resistance are important for products like electrical appliances and cars. This is why these kinds of products are made with materials such as rubbers, polyurethanes, and epoxies which are examples of Thermosets. Thermoset plastics are more durable than thermoplastics.
However, the major setback is the inability to recycle or break down the products after usage. It results from the bond between the polymers of thermosets being stronger than the one of thermoplastics. Thermoplastics melt and lose their shape when heated, but thermosets do not melt.
Moreover, thermosets are lightweight and flexible while adding strength, impact resistance, and toughness. They also support further strengthening with reinforcing materials like carbon and fiberglass. As a result, their dimensional stability and excellent structural advantages make them more durable than thermoplastics.
Applications
The usefulness of thermoplastics varies from one industry to another. They are good substitutes for metals since they are resistant to chemical attacks such as corrosion. Because of this, they are used in various industries such as the medical and biomedical, chemical, plumbing, automotive, food and beverage, electronics, and construction industries. Some thermoplastic applications include:
- Industrial machine components
- Electrical encapsulation and insulating materials
- Laboratory equipment
- Non-stick cookware
- Gas tanks
- Piping systems
Also, several industries choose thermosets since they are more economical and meet product specifications. Easy formation of complex geometric shapes and the ability to withstand high temperature is among the reasons for the choice. Thus, these plastics are ideal in situations involving heat. Such applications include the following:
- Electronic housings
- Chemical processing equipment such as pipes, cell covers, and fittings
- Panels, housings, and doors
- Medical components
- Components and parts for vehicles
Cost
Thermoplastics often present lower prices than thermoset plastics when it comes to manufacturing costs. While this is true to some degree, thermosets offer more benefits than their thermoplastic counterpart.
Several factors affect the overall cost of manufacturing plastic parts with either of these materials. These factors include the material itself, the tooling, production time, finishing options, and labor cost. Suppose budget is a concern for your manufacturing process. In that case, you need to first consider upfront tooling costs, performance, and surface finish before choosing the material.
Comparison Table of Thermoplastic vs Thermoset
Properties | Thermosets | Thermoplastics |
Molecular Structure | Network polymers. There is a high level of crosslinking together with strong molecular bonds. | Linear polymers. The molecular bonds are weak and are in a straight chain. |
Melting Point | The melting point is higher than the degradation temperature. | The melting point is lower than the degradation temperature. |
Microstructure | They are comprised of resin and reinforcing fibers in a solid state. | They are comprised of elastic amorphous and hard crystalline regions in the solid state. |
Mechanical | Brittle and inelastic. Rigid and strong. Thermoset strength comes from crosslinking. | Flexible and elastic with increased resistance to impact. Thermoplastic has its strength from crystallinity. |
Recyclability | Non-recyclable. | Recyclable and reusable. |
Chemical Resistance | Chemical and heat resistant. | Highly chemical resistant. |
Solubility | Do not dissolve in organic solvents. | Can dissolve in organic solvents. |
Thermoset vs Thermoplastic: Pros and Cons of These Polymers
Here, we will examine the pros and cons of thermoplastic and thermosetting plastic so help you make the best choice for your project.
Pros and Cons of Thermoset
Pros | Cons |
Resist corrosion | Inability to reshape or remold |
Good electrical insulation properties | Unrecyclable |
Resist water | |
Strong dimensional stability | |
Resist heat at high temperatures | |
Allows for flexible product designs | |
Low thermal conductivity | |
High strength-to-weight ratio |
Pros and Cons of Thermoplastics
Pros | Cons |
Resist corrosion | Not suited to all applications due to softening when heated |
It can be remolded and reshaped | Typically more expensive than thermosetting polymers |
Can be recycled | |
High-quality aesthetic finish | |
High impact resistance | |
Resist Chipping | |
Superb electrical insulation | |
Enhanced anti-slip properties |
Thermoset vs Thermoplastic: Which One is Best for Your Project?
There is a couple of difference between thermoplastic and thermosetting plastic. These polymers come in a wide range of material options and serve different applications. There is no limit to the purposes these materials can serve and under good working conditions. Therefore, both thermoplastic and thermosetting plastic materials are excellent choices for your products.
However, the type of plastic used depends on the products required. If you require a product that should be able to withstand high temperatures, then Thermoset plastics are suitable. However, if you require a product that can withstand corrosion, then thermoplastics are suitable.
The materials have incredible features that make them stand out among material options for injection molding. Real-world applications will require you to select the best materials. This is why you need the help of professionals.
RapidDirect Plastic Injection Molding Services
Whenever you hit a roadblock while selecting plastics for your products, RapidDirect is always ready to bail you out. We boast highly skilled engineers who will analyze your design and help you determine which material is best. Therefore, you can be rest-assured of getting the best services from the most experienced hands.
Besides, our facility has the most advanced machines to make the process seamless and reduce cycle times. You will get our top-notch injection molding services at competitive pricing. If you need high-quality injection molded parts, contact RapidDirect today!
The content & opinions in this article are the author’s and do not necessarily represent the views of ManufacturingTomorrow
Comments (0)
This post does not have any comments. Be the first to leave a comment below.
Featured Product
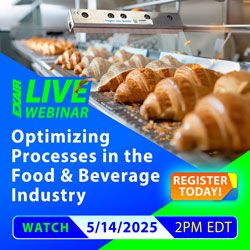