Building raw material and semi-finished inventory is a typical management response to help ensure supply chains can deliver customer orders on time, but it doesn’t always provide the relief needed and carries a lot of inventory costs with it.
Crushing the Bullwhip Effect in Your Supply Chain with Inventory Optimization
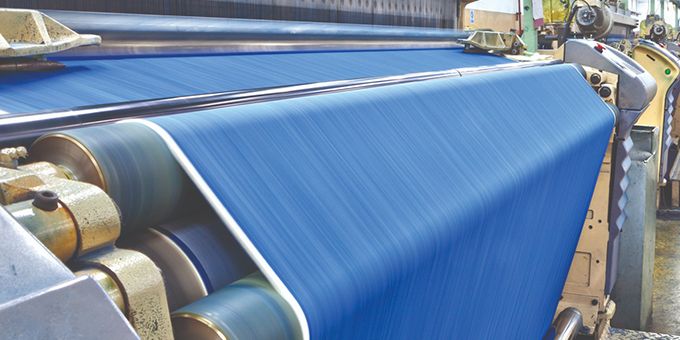
Pete Hock | Performance Solutions by Milliken
A few flicks of the wrist can cause the far end of a bullwhip to flail widely and rapidly. The bullwhip effect can also be seen in extended supply chains where changes in customer demand become amplified as they are transmitted upstream. This often happens when product lines offer many customer choices – colors, textures, sizes and components. An integrated carpet manufacturing supply chain provides a good case study. The key conversion steps in this supply chain are yarn twisting, tufting, and finishing.
In yarn twisting, single fibers are twisted together to make thicker, stronger yarn suitable for carpeting. Twisted yarns can be made with a single fiber color, or with mixed colors to create a tweed effect. Twisted yarn may be treated further with chemicals or heat to enhance performance. A small twisting plant may stock 50 different single fibers and produce 100+ different twisted yarns.
At the next plant, tufting machines hook and knot the twisted yarn into tufts (loops) on a non-woven carrying fabric called the scrim. Tufting is a custom process. Options include type of yarn, color and carpet texture. Texture is determined by loop size and density. Plush carpet is made by cutting the outer end of the loops. A medium-sized tufting plant may utilize 300 twisted yarns and a variety of scrims to produce 500+ different types of raw carpet.
Finishing is a custom process as well. It involves bonding the raw carpet to a strong backing and coating the upper surface for durability and dirt resistance. A finishing plant may produce up to 1,000 different finished carpets.
In this supply chain, the bullwhip effect takes shape when a customer order for a special color finished carpet results in a schedule change at the tufting plant. This results in a spike in demand for a particular twisted yarn. If you multiply that by 100+ orders per day, the result is a boom-or-bust scheduling problem at the twisting and tufting plants.
Implementing a lean replenishment strategy
Prior to implementing a lean replenishment strategy, twisting and tufting plants felt the business impact of the bullwhip effect with:
- excess labor costs
- productivity losses
- missed deliveries
Building raw material and semi-finished inventory is a typical management response to help ensure supply chains can deliver customer orders on time, but it doesn’t always provide the relief needed and carries a lot of inventory costs with it. Supply Chain managers end up with too much of the wrong things on hand, and too little time to meet the next order coming up.
A far more effective strategy is to use lean principles to work smarter, not harder, and eliminate waste. Starting at the yarn twisting plant, the top of the integrated supply chain, the process ran as follows:
Improve flexibility through Rapid Changeover
Unless the economic run quantity (ERQ) is examined using lean tools, it is usually determined by productivity goals. Managers will target longer run quantities to make up for long changeover times. However, this results in a loss of scheduling flexibility, which usually leads to missed deliveries. To illustrate, each time a twisting machine changes product, it involves a series of manual tasks. Workers must doff the finished bundles, doff the single fibers, clean the equipment, load in new single fiber bundles, and then prime them for twisting.
A lean improvement process called Rapid Changeover (RC) can bring NASCAR-like pit-crew speed and organization to the changeover process. At the twisting plant, this involved creating a flow-to-the-work crewing plan that brought additional hands to the machine that needed changing. RC processes typically deliver 30%+ reduction in changeover time. While this may bring additional production hours each day, managers are usually better off reinvesting this time in more changeovers, enabling greater scheduling flexibility and better inventory management.
Analyzing Product Demand
Using recent customer order data, the twisting plant prioritized the SKUs it produces. The lean team found that 20 SKUs make up over 80% of the order bookings. These were designated to be the “A” SKUs. An additional 20 SKUs make up the next 10% of bookings, known as the “B” SKUs. The remaining 60 “C” SKUs make up only 10% of total bookings. The lean team then analyzed the “A” and “B” SKUS for average order size and frequency, and standard deviation of the same. These data enabled the team to devise a replenishment strategy that ensures delivery while minimizing inventory.
Creating a Product Replenishment Strategy
This step begins with a rule of thumb: Run the A SKUs every week, the B SKUs biweekly, and the C SKUs only when an order is posted to the books. Each A and B SKU demand is then analyzed to determine the economic run quantity and target inventory levels. This analysis takes into account raw material lead times, production rates, and delivery lead time. It also makes allowance for variations in demand, productivity and raw material supply.
Coordinating Raw Material Sourcing
Creating a new production schedule based on lean ERQs offers the opportunity to re-tune raw material order quantities for better fit. The twisting plant worked with the singles supplier to reduce single fiber inventories by 25%.
Coordinating Storage and Delivery
Lean tools such as Kanban lanes and supermarkets with visual indicators provide simple and effective means to manage inventory at both upstream and downstream operations. The twisting plant established a supermarket from which the tufting plant could draw on at will. This insulated the twisting plant schedule from spikes in demand, enabling a 28% reduction in labor overtime premiums.
Monitoring, Adjusting & Reapplying the Process
Since the ERQs and replenishment targets were based on past order patterns, twisting and tufting established a weekly review and response process to ensure ongoing communication and alignment. Unusual demand spikes continued to occur, but the communication process enabled the teams to contain any spillover and avoid new rounds of boom-or-bust scheduling. ERQ targets were reviewed anew every 3 months and replenishment targets were adjusted to take into account expected seasonal upswings or downswings. The twisting plant’s new replenishment strategy provided remarkable improvements in under 3 months. The lean replenishment strategy delivered:
- labor overtime savings
- raw material inventory reductions
- freeing over $1.5 million in cash
- while improving supply reliability to the tufting plant
Leaning Out the Extended Supply Chain
The twisting plant demonstrated the value of a lean replenishment inventory strategy to the carpet manufacturing division. Division management embarked on a plan to realize comparable gains in tufting and finishing, while managing inventory more efficiently. The tufting lean project is currently in progress. Although the product mix is more complex than twisting, the 80-20 principle and lean tools apply just the same. The tufting lean team has isolated the “noise” in the demand signals and are focusing on improved delivery and reduced inventory levels for their most important SKUs. Ultimately, division management expect to double, then triple the gains realized so far.
The content & opinions in this article are the author’s and do not necessarily represent the views of ManufacturingTomorrow
Comments (0)
This post does not have any comments. Be the first to leave a comment below.
Featured Product
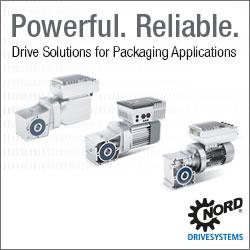