While PLCs control mechanisms, electronics, and other low-level devices, HMIs empower operators with visualization and touch controls. Together, HMIs and PLCs pave the way for efficient and flexible industrial workflows.
Why Combining Your HMI & PLC Is the Smarter Move
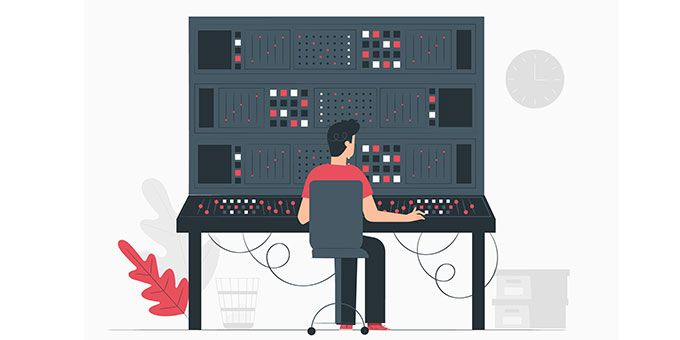
Article from | CIMON Inc.
In previous articles, we talked about two tools—PLCs (programmable logic controllers) and HMIs (human machine interfaces)—that are essential for modern automation. While PLCs control mechanisms, electronics, and other low-level devices, HMIs empower operators with visualization and touch controls. Together, HMIs and PLCs pave the way for efficient and flexible industrial workflows. Each serves a unique purpose, and both are needed for optimal performance.
The problem is that every piece of equipment requires additional time, space, and money to implement. Fortunately, these two tools can be combined into a single physical device, often called a hybrid HMI + PLC, or just hybrid for short. This offers a broad set of improvements without sacrificing on cost or convenience. Although some situations do call for standalone PLCs or HMIs, a hybrid is the clear choice for many small- to medium-scale applications.
BOTH IS BETTER
First, let’s talk about why HMIs and PLCs are both necessary. Even a simple automation solution can involve many different kinds of processes, devices, and desired behavior. Because all of this happens at different levels of abstraction, different kinds of control devices are needed.
For any time-sensitive or high-precision work, a PLC is indispensable. The clearly-defined, step-based logic they use is ideal for assembly lines. PLCs are also the industry standard for handling physical inputs and outputs, controlling electrical relays, and communicating with industrial sensors like thermocouples or proximity detectors.
For physical ON/OFF switches, a PLC is perfect, because each bit can be tied to a specific routine. But for more context-dependent settings—like selecting objects, entering text, or defining a user schedule—a graphical interface is much simpler to program and use. This is where HMIs come in. Rather than having one hard-wired mechanism control one variable, an HMI can display a dynamic interface that changes based on user inputs, device values, and custom programming.
User and device data can then be exchanged in a collaborative fashion. Inputs can be used to control the physical workflow, and results can be displayed and analyzed as needed. A properly designed control system will treat the operator as an integral part of the process, while still letting the PLC automate the low-level tasks. Because HMIs and PLCs work together so closely, putting them into a single product was the natural next step for manufacturers.
ALL IN ONE AND ONE FOR ALL
Perhaps the most obvious advantage of combining two things into one is only having one thing to deal with. A hybrid HMI + PLC is no exception, offering a smaller size, simpler layout, and fewer wires. Changing the wiring for an automation system can be challenging, but eliminating parts can simplify the job. Cost is also a major factor; a single hybrid setup can easily save a hundred dollars or more.
For someone installing dozens of such setups, the advantage is multiplied. Hooking up one extra HMI or PLC might not be an issue, but doing this hundreds of times can be a sizable task. A hybrid also has a reduced footprint, meaning the external control panel can be smaller (and cheaper). In some cases, using a hybrid means an entire power supply, terminal block, or other unit can be excluded, thus providing further savings.
With industrial hardware, issues often arise from the connections between devices, rather than from the devices themselves. A hybrid can make a system more reliable and easier to troubleshoot because its primary PLC-HMI connection is self-contained. Inventory management is also simplified since orders, maintenance, and repairs can all be based on a single part number. This benefit extends to any additional wires or components that would have been needed for a non-hybrid solution.
More generally, using the same company for multiple products can help streamline project creation. This is especially important for HMI-PLC applications, where changes to the user interface can require changes to the program logic and vice-versa. Most manufacturers support proprietary features and protocols for their hardware, including special options for hybrids. Typically, this means a project’s tags and communication will require less configuration, especially when first getting started. It is also easier to receive customer support when all components come from the same vendor.
THE CIMON XPANEL HYBRID
The exact features of a hybrid vary from manufacturer to manufacturer. To give an example, we’ll consider the CIMON Xpanel Hybrid, which combines a 7” Xpanel HMI with a PLC-S PLC. While some hybrids use a single CPU, CIMON Hybrids have separate processors for the HMI and PLC, ensuring maximum reliability and consistency. In the event of an HMI failure, the critical PLC logic will continue to operate.
Any project designed for a standalone Xpanel or PLC-S can be run on a Hybrid; transitioning is as simple as checking a checkbox. There is no need to learn additional editing software; just use CIMON’s established XpanelDesigner HMI software and CICON PLC programming software. Both projects can be edited independently, but still downloaded using a single USB connection, or over Ethernet. This also means the HMI project can be updated without affecting the PLC operation, and vice-versa. You can even remote into the HMI and PLC simultaneously and edit the ladder logic in real time.
The Xpanel Hybrid has sink, source, and relay options for embedded I/O, as well as RS-232C and RS-485 serial ports for both the Xpanel and PLC. All PLC-S expansion modules are also supported, with options for digital and analog I/O, temperature reading, and additional communication. Combined with the Xpanel’s diverse library of protocols, this allows the Hybrid to handle a wide range of problems and work with a variety of other devices.
IN SUMMARY
In short, a hybrid has clear advantages for the most frequent use cases. The accompanying compactness, simplicity, and lower price are difficult to beat. While there is almost always more than one way to tackle an automation problem, hybrids are in general a flexible and cost-effective option.
Nevertheless, when a project calls for a large number of I/O points, larger HMI screen sizes, or redundancy, you may need to opt for standalone solutions. Fortunately, CIMON also offers a variety of HMIs, PLCs, and IPCs suited for all kinds of applications. If you are working with multiple Hybrids, you may also want to consider upgrading your project with an integrated SCADA system. Last but not least, when you choose CIMON, technical support is always free and easily available. Get in touch with CIMON today to find out more!
The content & opinions in this article are the author’s and do not necessarily represent the views of ManufacturingTomorrow
Comments (0)
This post does not have any comments. Be the first to leave a comment below.
Featured Product
