Unshackled by the limitations associated with traditional production processes, AM has made the leap from prototype to end part production and continues to open up exciting opportunities around localised production, digital inventories and on-demand manufacturing.
Automating Post-Production to Scale-Up Additive Manufacturing
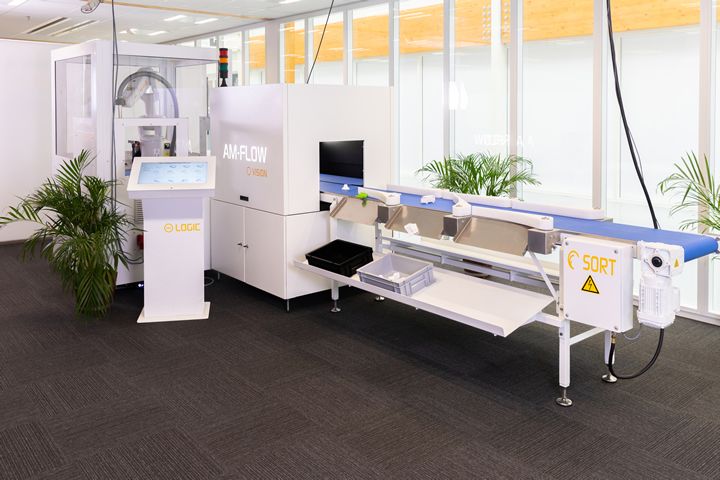
Q&A with Stefan Rink, CEO | AM-Flow
It is no exaggeration to say that additive manufacturing (AM) has revolutionised the way products are designed, manufactured and distributed. Unshackled by the limitations associated with traditional production processes, AM has made the leap from prototype to end part production and continues to open up exciting opportunities around localised production, digital inventories and on-demand manufacturing. Yet, despite the technology’s many advantages, post-production remains a labour-intensive and costly process that presents a major barrier for companies looking to scale-up their AM operations. We caught up with Stefan Rink, CEO of AM-Flow, who explained how advances in post-processing software and hardware mean that this is finally about to change, and how this will, in turn, enable 3D printing to finally become a fully-digital, fully-connected part of the factory of the future.
Can you start by giving our readers a quick overview of who AM-Flow is and what the company does?
We provide an end-to-end digital manufacturing solution that enables 3D print producers to automate AM post-processing. Or to put it another way, we allow companies to create a truly automated 3D printing workflow. 3D printing is a highly automated process – right up until the point when the print leaves the machine. After that, everything else, from picking and sorting to packing, is done manually. That is highly inefficient, expensive and leaves processes vulnerable to human error. Our solutions enable companies to address these challenges and will, we believe, finally enable 3D printing to deliver on its promises of the last decade.
That sounds logical. Yet, many companies have been using 3D printing, whether to produce prototypes or end use parts, for years. Why are they only thinking about post-production now?
Most AM production environments have grown organically. Companies have been focused on the printing technology, adding new printers and expanding their use of materials as required, rather than concentrating on the overall production process. We are expecting that the use of 3D printing is only going to increase, and as it does so, labour costs will rise exponentially. That is simply not viable for companies looking to scale-up 3D print production, and so they must find a way to automate the process. We therefore expect to see companies move away from investing predominantly in printing technology, to investing in the overall production workflow.
What makes post-production in AM such a challenge?
The main advantage of 3D printing is its ability to produce any object, i.e., infinite geometries. However, that is also exactly what makes post-processing so challenging. A single production line may produce hundreds of different geometries, even within a single batch. This poses difficulties in terms of identification, sorting, quality control, handling, transportation and packaging 3D-printed parts. Add to this the pressure to reduce the cost per part for AM and it is clear that things have to change. By applying machine learning and an Industry 4.0 approach from the ground up, AM-Flow is able to deliver modular solutions that, when combined, provide a complete end-to-end workflow solution that overcome the challenges I have outlined.
So, what exactly does the AM-Flow proposition include?
We have developed what we call the AM-Flow ‘stack’, a range of modular solutions that enable users to integrate almost every element of an AM production workflow. The beating heart of the system is AM-VISION, which enables rapid and reliable identification of 3D printed parts based on their geometry. Next comes AM-LOGIC, which is very much the digital brain, nervous system and muscle of the outfit, enabling the operator to view and control the whole post-production workflow via a simple user interface. Of course, once you can identify parts, you can sort them (using AM-SORT), and transport them via use of cobots (AM-ROUTE). We also market AM-PICK, which enables operators to go from batch process to single part process. In addition to these modules, which are already available on the market, we have several more in development, so watch this space!
Who do you see as being a typical customer for your product? Do you have any customers now?
Any company in an AM growth environment. That may be a service provider, or it could be an OEM who is dealing with high-volume, high-mix output from their machines. Typically, they have a minimum of three 3D printers, and anything above that, which may be SLS, MJF, FDM or anything else. Our software works with all types of 3D printing technology and all materials, including metals.
We have several customers who are implementing different elements of the AM-Flow stack into their post-production processes. These include major players from industries as diverse as automotive, aerospace and medical, and include BMW, Midwest Prototyping, Oceanz, Shapeways, Materialise and Marketiger.
All these industries must have different digital environments. How do you cope with that?
To go back to my earlier point, most AM production environments have grown organically over time to meet specific needs or challenges. As a result, the landscape is extremely fragmented – nothing is standardized and there are a lot of proprietary systems in place. Therefore, all AM-Flow modules are designed to ‘plug in’ to whatever is out there. They are compatible with all existing MES and ERP software and can also be integrated with external systems such as cleaning and part quality-enhancing post-processing hardware, enabling a swift and smooth transition to full automation.
With so much information being collected, how do you ensure intellectual property is protected?
That’s a question we get asked a lot, but actually all designs are completely secure. Our analysis is purely on the data sets required to feed identification and our machine learning process, and that data cannot be translated back into a design. It’s just not going to happen.
You mentioned plans to add further modules to the AM-Flow ‘stack’. Is there anything you can tell us about now?
Absolutely. We recently introduced AM-BAGGING, a module that, as its name suggests, provides fully automated bagging and labelling capabilities to AM environments. The new solution perfectly bridges between AM-pick and AM-Route and exemplifies our continued quest to provide a full ‘end-to-end’ post-processing solution to manufacturers and service bureaus. We are now looking forward to introducing a further new addition to our stack early next year.
Finally, can you summarise AM-Flow’s long-term objective in just one or two sentences?
Our goal is to create the full AM end-to-end automated production line, i.e. automate all steps after the printer. We are still quite a long way away from a ‘lights out’ factory but that is definitely the point in the future we are aiming for.
AM-Flow’s ‘stack’, is a range of modular solutions that enable users to integrate almost every element of an AM production workflow
AM-BAGGING provides fully automated bagging and labelling capabilities to AM environments
AM-VISION automates the identification of unique parts, cutting time and labour intensiveness
The content & opinions in this article are the author’s and do not necessarily represent the views of ManufacturingTomorrow
Comments (0)
This post does not have any comments. Be the first to leave a comment below.
Featured Product
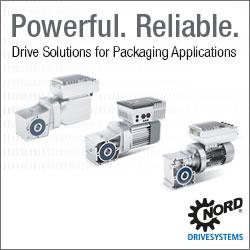