Omron gave preference to EtherCAT over DeviceNet because the latter is a slower CAN-based protocol designed for sensors and it uses screw-type connections that can be difficult to install and maintain.
Omron Helps Life Sciences Company Upgrade Prototype with Cutting-edge Technology and Cut Costs by 30% With Solution Using NX-I/O
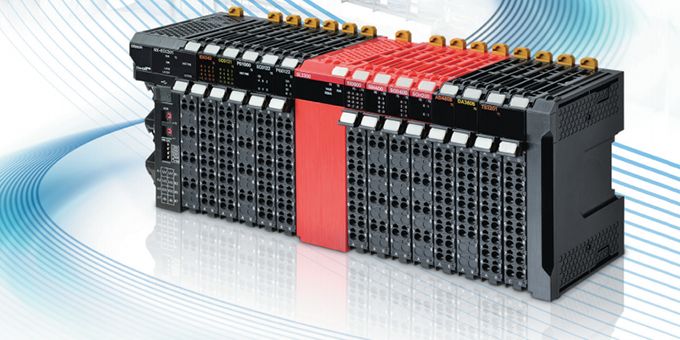
Case Study from | Omron
A leading provider of research and development services for engineering and life sciences companies sought to improve upon the design of an initial prototype for its production machinery. The company initially wanted to implement a solution using DeviceNet and contacted Omron for assistance.
Omron found that it would be more effective to introduce EtherCAT technology by means of the NX Series I/O System. This ultimately led to a demonstration of the Sysmac platform and subsequently a bill of materials proving that the NJ Series Machine Automation Controller and NX-Series I/O System would save 30% of costs compared with the previous design.
Omron gave preference to EtherCAT over DeviceNet because the latter is a slower CAN-based protocol designed for sensors and it uses screw-type connections that can be difficult to install and maintain. EtherCAT, an Ethernet-based control protocol with RJ45 connectivity, is easier to implement in large part because customers can leverage their understanding of Ethernet.
Although it was too late to convert from using a different supplier for prototype production, Omron secured the remote I/O and began to actively work on transitioning the R&D company to a full Sysmac solution. The company was so impressed with the new solution’s potential that they paid for a threeday, on-site training event for their engineering staff. Omron worked with the customer to develop a complete plug-and-play solution that worked within its timeline.
The need
The customer had a four-month timeline for putting together a plug-and-play solution for its remote I/O that would employ the most cutting-edge automation technologies. One of the main goals of the redesign was to improve the efficiency of the production machinery. Most importantly, the customer needed to reduce hardware costs and installation time.
Without a decrease in hardware and labor costs, it would be difficult for the customer to convince investors to support a transition from the initial prototype to Generation 1 and Generation 2 production. The original solution used technologies from a different supplier, so significant changes were needed.
It was necessary to focus on making the solution as economical as possible. In particular, the customer needed to significantly improve the system’s temperature control in order to ensure that the reactor would run as efficiently as possible.
The technology
The solution that Omron proposed involved implementing an NX-Series I/O System on each machine. Part of the powerful Sysmac solution, the NX-I/O is the premier I/O system for Omron’s NX and NJ controller families. With over 130 individual I/O slice types, the NX Series I/O System expands machine functionality and adds value by replacing older, troublesome I/O systems.
The NX-I/O is platform agnostic, so it works well not only with the full range of Omron controllers, but also with most Ethernet/ IP and EtherCAT systems from other PLC manufacturers. This is because Omron made sure to follow the global standards for these networks in the design of the NX-I/O.
A local Omron distributor set up the interface between the NX-I/O slaves and a master from the original automation supplier. The customer purchased three NJ Series controllers for internal testing and started working on converting to an Omron master for Generation 3 production. Omron provided a three-day training on the Sysmac platform and the NJ controller family.
Business need
A leading provider of green research and development services for engineering and life sciences companies needed a plug-and-play automation solution to improve its Generation 1 machine that converted flare gas to methane for the oil and gas industry.
Unique solution
Omron proposed an EtherCAT-based solution employing the NX-Series I/O System for the customer’s remote I/O needs along with temperature control and machine automation controllers from the NJ family.
Customer benefits
The solution cut costs by 30% and boosted machine performance, and the NX temperature control allowed the customer to scale up the design from a 250kW reactor to a 1mW reactor in their Generation 3 machine.
The outcome
The integrated EtherCAT system significantly improved machine performance and temperature control and enabled the customer to successfully reconfigure the entire I/O package within the four-month time frame. The complete plug-and-play solution resulted in cost savings of 30% on remote I/O, in line with what Omron had initially projected.
The customer deployed its first six prototype machines for on-site testing and worked closely with Omron to reconfigure the NXI/O system for the Generation 2 prototype production of approximately 50 machines.
The design eventually allowed the customer to scale up from a 250kW reactor to a 1mW reactor in the Generation 3 machine, in large part thanks to the system’s support for EtherCAT and the NX-TS temperature input slice module.
The content & opinions in this article are the author’s and do not necessarily represent the views of ManufacturingTomorrow
Comments (0)
This post does not have any comments. Be the first to leave a comment below.
Featured Product
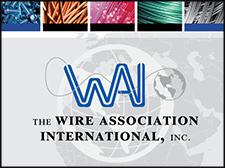