While the global covid19 pandemic seems to be fading into the annals of history, the next crisis loomed large before the last one could begin to fade away into obscurity. What do these two most recent crises in the US demonstrate to the manufacturing world?
Physical Manufacturing, Outsourcing and the Digital Age of Crisis
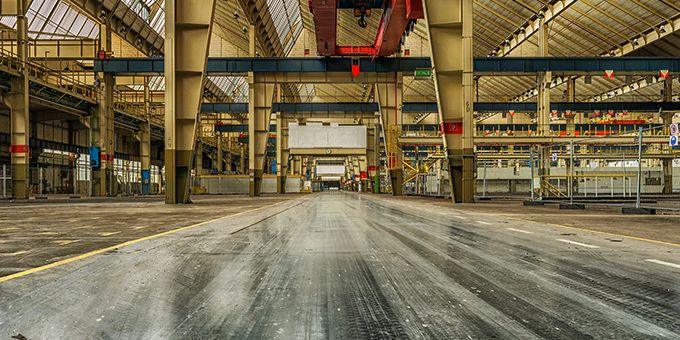
Article from | Ofer Tirosh
Figure 1: Image Source: Markets and Markets Website
While the global covid19 pandemic seems to be fading into the annals of history, the next crisis loomed large before the last one could begin to fade away into obscurity. What do these two most recent crises in the US demonstrate to the manufacturing world? There will always be disruptions to industry.
So how do industrial manufacturers minimize risk and mitigate losses even during such tumultuous times? The most effective answer seems to be moving as many operations as possible into remote positions, either through work-from-home employees or other remote service providers? These days, even much of the manufacturing can be outsourced. So what are the benefits and detriments of the digital age on industrial manufacturing?
The concept of Global Value Chains are not lost on the manufacturing industry. Business process outsourcing has led to an increasingly difficult to manage supply chain that relies heavily on logistical support in order to remain competitive. The World Economic Forum has struggled to keep up with all of the recent changes, though no matter how many times they go over the numbers, the outlook is not good for the manufacturing industry.
“Over the past four decades, much of manufacturing production world-wide has been organized in what has become known as global value chains (GVCs). Raw materials and intermediate goods are shipped around the globe multiple times and then assembled in yet another location. The final output is re-exported to final consumers located in both developed and developing markets.”
Can modern technology in “the new normal” and in the digital age now be used to reverse the complexities of the global value chains through the same process of business process outsourcing?
Figure SEQ Figure * ARABIC2: Image Source: Economics RaboBank website – Industrial production and manufacturing drop drastically in a post covid economy. Can the same business process outsourcing (or BPO) be used in order to streamline production and industry?
The Role of Business Process Outsourcing in Global Value Chains
What is business process outsourcing? It is the process by which largely non-essential business functions are outsourced to third party, often remote service providers. In the case of business process outsourcing as part of the global value chains, it often includes essential materials and operations necessary to complete a finished product ready to be sold on the retail markets.
Among the greatest challenges when implementing business process outsourcing, can be the issue of language and communications in a more global market. Fortunately there are translation companies that specialize in business services and with the associated legal process. Outsourcing to foreign nations may require things like import and export licenses and documents to be translated into numerous languages. Business process outsourcing, when properly implemented, should make business operations more effective, not complicate matters. Thus, the services of the translation company that has all of the respective business services in place can be more efficient and even inexpensive in some cases.
The importance of a translation company becomes even more readily apparent when the manufacturing taking place will be outsourced to many different nations. Each nation will have different laws and requirements for both manufacturing imports and exports. Legal documents will have to be translated as will any labels and warnings as may be required. The means of communications can also be more easily facilitated through the use of remote video interpreters that can serve as a sort of liaison between the different phases of manufacturing operations from start to finish.
The Negative Aspects of Business Process Outsourcing for Manufacturing
There are considerations that must be given to business process outsourcing, especially when it involves many of the primary means of manufacturing and product development. These should have been considered within the constraints of a feasibility study before the BPO policies were implemented, but such may not have been the case.
There should definitely be considerations made regarding the security of both networks and computer systems, and also in regards to sensitive information. Such systems may be subject to hacking or other means that may compromise proprietary materials and trade secrets. These are absolutely concerns that need to be factored into the decision of whether or not to establish business process outsourcing as part of the manufacturing process.
Even Investopedia notes that among the concerns for business process outsourcing is in terms of communication, noting that “While there are many advantages of BPO, there are also disadvantages. A business that outsources its business processes may be prone to data breaches or have communication issues that delay project completion, and such businesses may underestimate the running costs of BPO providers.”
This simply reinforces the need for finding a well-established translation company that can provide the necessary business translation services at any time, day or night. There are many different aspects to the use of a translation company that should also be considered.
Pricing from the translation company will likely be very consistent. The translation services should be largely guaranteed to an extent. The translation company that specializes in business services will also be able to provide the legal document translations necessary for import and export and also all of the requisite paperwork including instruction manuals, warning labels and other similar documentation for the manufactured goods.
In this same article from Investopedia, it also notes that off-shoring can potentially be a problem, but there are different understandings of the term at the same time. “BPO is deemed ‘offshore outsourcing’ if the contract is sent to another country where there is political stability, lower labor costs, and/or tax savings.”
Among the most pressing concerns is the ability to ensure a consistency of quality assurance programs. One potential means of alleviating this process for the manufacturing industry is to consider the potential for off-shoring as opposed to outsourcing. This, whether or not the manufacturing firm retains in full control or ownership of the means of production.
The Role of Off-Shoring as Part of Business Process Outsourcing
Off-shoring can take one of two forms. It can be established as a subsidiary of the parent manufacturing firm or it can be a fully outsourced manufacturing operation to a third-party service provider. The ability to retain control of matters such as management capability, quality assurance and other oversight of the manufacturing process should be a part of the final decision process.
This is one area where off-shoring, or more accurately, the establishment of subsidiary manufacturing operations off-shore may be a substantially more viable option. This may once again present some issues of concern regarding communications, though translation and interpretation services should be sufficient to easily overcome these obstacles.
There may also be added costs as manufacturing operations, facilities, equipment and other purchases must be made. In the case of manufacturing companies that are already established, operations may continue in the original facility. In other cases for newer manufacturing firms, this may be relegated to a delayed commencement of operations with little impact after the delays end.
Such operations however, will allow for key personnel to be placed within the subsidiary and retain full operational control over the entire manufacturing process. When properly planned and implemented, this type of business process outsourcing can also allow for the entire production to be housed in a single facility, less prone to social unrest.
The Age of the Never-Ending Crisis and Business Process Outsourcing
According to the United Nations, China and the United States lead the way in terms of production. As was also previously noted in the second image, and using further statistics from both the United Nations and the World Economic Forum, the industrialized nations will suffer the most in terms of loss of production capacity.
It should be noted that these are also among the most expensive options for business process outsourcing using offshoring. Furthermore, and avoiding the political partisanship here, both of these nations have proven to be largely susceptible to social unrest or unreasonable oppression during times of crisis.
While the United States is certainly “user-centric” in terms of manufacturing operations, there are additional costs, not the least of which is having among the highest corporate tax rates in the world. Likewise China has many limitations that make it susceptible to challenges that can be more easily avoided by establishing offshore manufacturing facilities in developing nations instead.
Many of the developing nations have taken precautions in order to provide protection and security for their employees, but have retained the manufacturing industry as an “essential function”, keeping them in business even during times of crisis. Establishing a subsidiary manufacturing facility in such a nation will allow for manufacturing operations to continue, even during times of potential social unrest. While force majeure may still occur on occasion, such times should be kept to a minimal, as should any disruption of operations.
Digital Work, BPO and Moving Staff Into Remote Work Environments
If there is any major advantage to living in the digital age, crises or not, it is the ability to have a substantial portion of the administrative staff working as remote service providers or “work-from-home” employees. There are substantial savings for both the manufacturing firm and the employees working from a remote location, and further benefits to the environment and local communities.
The transition from the traditional office space to working from home can be challenging for both the manufacturing firm and the remote personnel, though the challenges can also be easily overcome with the proper precautions and steps being taken throughout the transitional period. There are some key points that should be considered and definitive measures put in place for remote employees.
One of the most common benefits that some like to point out is the increased level of productivity from employees who work from home. The statistic people like to focus on is the increased level of productivity from remote service providers. However, it should be noted that the studies generally only indicate an increased level of productivity when specific policies and guidelines are established for work from home employees.
The manufacturing company guidelines for remote employees should cover all aspects of remote work, including the following:
-
Availability – When will the employees be expected to work?
-
Personal Agreements – This will include Non Disclosure, Work For Hire, and other agreements as may be necessary.
-
Eligibility – Which employees are eligible?
-
Equipment – What equipment is required and who is responsible for providing the equipment?
-
Productivity – What is the expected level of work production?
-
Restrictions – What restrictions are in place?
-
Security – Will the employee be allowed to use their personal equipment? What security precautions should the remote employee take?
-
Service Providers – When working with service providers such as remote interpreters or translators, are there specific providers the remote employees should use?
-
Technical Support – Who is responsible for technical support? Especially important in regards to privately owned equipment.
-
Termination – Remote employees may be fired for different reasons, but the reasoning still needs to follow specific guidelines.
-
Supplemental Information Sheet – There should be an added section including supplemental information. Among the information is the inclusion of relevant tax laws that the work from home employee may not be aware of. Will payment be made electronically? Will the employee be responsible for coming in and physically getting their check? Will this interfere with their work schedule? Any additional information should be included in this portion if it does not merit its own section within the remote employee policies and guidelines.
A feasibility study must also be undertaken in order to determine what percentage of employees from each department can work in a remote position without any disruption to operations. The feasibility study should also include a cost-benefit analysis and other relevant data to indicate any potential disruption that may arise in terms of remote employees.
Among the most common jobs within the manufacturing industries that have been successful in remote operations are accounting staff, IT staff, language service providers such as translators and interpreters, and human resources personnel. The actual staff able to work remotely may vary depending on the needs of the individual manufacturing operations however.
As the world becomes increasingly global and digital in nature, it becomes more possible to actively engage in business process outsourcing. At the same time, there needs to be assurances that as much of both the manufacturing process and the administration of operations remains under the full and complete control of the manufacturing firm.
As the technological revolution expands even further, it will soon be time to consider manufacturing and logistics in terms of automation. The digitization of the manufacturing administration and the establishment of manufacturing facilities that are not as prone to social unrest or other crises should also make that transition easier as soon as it becomes a potential reality within the manufacturing industry.
The content & opinions in this article are the author’s and do not necessarily represent the views of ManufacturingTomorrow
Comments (0)
This post does not have any comments. Be the first to leave a comment below.
Featured Product
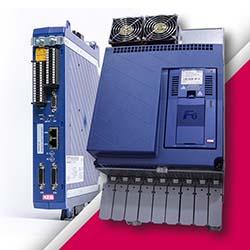