As hybrids boast both a conventional engine and electric battery power, drivers get the best of both worlds. However, many aren’t aware that the hybrid concept also extends to composite materials.
Hybrid Composites Help Manufacturers Get the Best of Both Materials
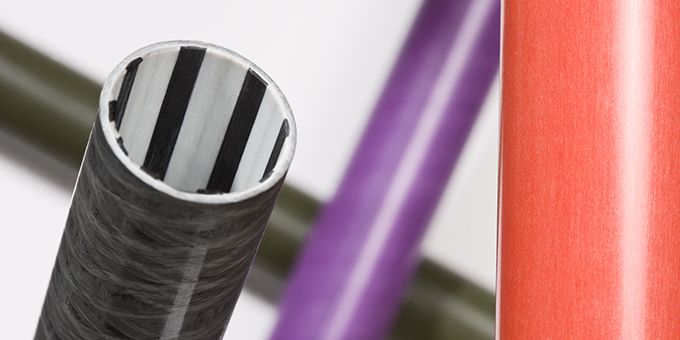
Patrick Loock | Exel Composites
By definition, a hybrid is achieved by combining two different items together so that the end result contains qualities relating to both of them. If we also think about defining composites, resin and fiber are combined to form a material that is better than the two original materials.
Hybrid composites take this one step further by combining two or more reinforcement fibres. Carbon fiber and fiberglass are commonly used, although it is possible to produce a hybrid using a variety of other fibers — such as natural ones. By using a hybrid structure, the optimum ratio of both materials’ mechanical properties can be reached to cater for the needs of an individual application.
Bringing the benefits
Hybrid composites have many advantages. Using a hybrid of fibers makes it possible to combine the benefits of multiple fiber types while simultaneously reducing their weaknesses. It is thanks to these benefits that hybrids can be used across a range of industries and for a variety of products.
Perhaps the most obvious boon of using a hybrid is its economic value. Composite materials aren’t particularly known for their modest budget and it’s rare to see, for example, a car made with using mostly carbon fiber due to its steep price. Hybrid composites can offer a cost-cutting solution to customers, as combining carbon fiber with a less expensive fiber reduces the amount of expensive product but still allows end users to reap its benefits.
Combining those fibers into a composite solution would undeniably enhance its robustness and create a more durable material. It is also favoured for its light weight, so combining carbon fiber with fiberglass would provide customers with an ideal option for applications where low density is an essential design consideration, such as in aerospace.
However, one of the drawbacks of carbon fiber is that it is brittle and breaks more easily upon impact. By combining carbon fiber with a more flexible fiber, such as fiberglass, manufacturers can improve the rigidity of the material and increase its impact resistance. Furthermore, carbon fiber conducts electricity — a quality that can be viewed as both an advantage and a limitation, depending on where it is applied.
Fiberglass composites, on the other hand, are insulators and can resist the flow of electric charge. It’s a case of opposites attract — more carbon fiber can be applied to increase the electrical conductivity of the finished product, while more fiberglass can help insulate it for applications such as electrical enclosures, where conducting currents could damage equipment.
The where and how
The fibers in hybrid composites can be arranged in multiple ways, depending on the desired outcome. At Exel, we manufacture a range of hybrid composites using continuous processes to provide customers with an outcome that is tailored to their requirements. We would select the type of fiber that would fit to your final expectation in terms of properties. Using the pultrusion method to permeate the fibers with a thermoset resin and pull them through a heated die for curing, we can manufacture hybrids in several different ways — depending on how and where customers want to use their benefits.
For example, different fibers can be mixed together so that they are evenly blended throughout the composite. We can also create hybrid profiles and tubes that are primarily made using fiberglass, with carbon fibers strategically weaved throughout the product for added strength. Another strength-enhancing option would be to manufacture a product using one type of fiber on the inside and with a strong carbon fiber outer shell. On the contrary, we can place pigmented fiberglass on the outside of the product to vary the composite’s colour and switch up its aesthetics.
While all these methods are possible, an understanding of the best solution for the end requirements is essential. When developing a hybrid composite, both the mechanical needs of the product and the economical limits of the customer must be considered.
Hybrids are gaining traction in industries beyond automotive because they give customers the option to enjoy new characteristics. We’re often told that we cannot have the best of both worlds, but composites make it possible. Blending two materials together to form a hybrid composite doesn’t only mean that we can enjoy the benefits of each material, but a combination of different fibers that creates a whole new set of qualities that cannot be achieved using just one type of fiber or one specific material.
If you like this article you may like "Quick Guide to Metal Additive Manufacturing for Industrial Components"
The content & opinions in this article are the author’s and do not necessarily represent the views of ManufacturingTomorrow
Comments (0)
This post does not have any comments. Be the first to leave a comment below.
Featured Product
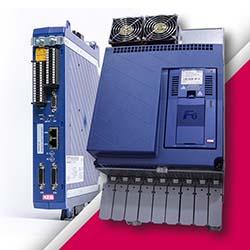