The necessity of skill building in the manufacturing industry
Thanks to advancements in robotics, the manufacturing industry is undergoing a significant transformation, and workers need to adapt quickly to keep pace. But there’s an ever-growing skills gap that’s posing problems. Skilled workers are exceeding supply, forcing every US organisation surveyed by Visual Components to offer higher salaries to attract in-demand talent.
The shortage of skilled labor is a major hurdle for companies aiming to enhance their automation processes through superior design and execution. The resulting delays and errors can incur unnecessary costs and loss of flexibility. But with Industry 5.0 centered around humans, it’s essential to address the skills shortfall.
Manufacturers can no longer depend on a reliable intake of readymade skilled workers. Instead, they need to focus on their current workforce and building their capabilities, allowing them to leverage advanced automation and robotics. Alternative approaches, such as intuitive simulation software can pave the way for operational excellence, encourage productivity improvements and enable business objectives to be met.
Not yet ready to access Industry 5.0 opportunities
The skills shortages facing the industry have been significant and long-lasting. Even when considering Industry 4.0 initiatives, Deloitte estimates the US manufacturing sector alone will face 2.1 million unfilled jobs by 2030. But this is at odds with the ambitions of Industry 5.0. While 4.0 focused on automation and IoT, 5.0 upholds the values of sustainability, resilience and human productivity. Resilience in all its forms has become a priority in the face of higher levels of volatility in global politics, supply chains, disease and weather patterns.
Skills are a centerpiece of Industry 5.0. Instead of regarding staff purely as costs, employers should maximize the return they make from each employee. This is where robotics, cobots (collaborative robots), virtual and augmented reality and exoskeletons all have a role, along with data analytics and artificial intelligence.
Combining emerging technologies such as edge computing infrastructure and SaaS innovation with robotics can encourage strategies that match the values of Industry 5.0. Manufacturers can create digital twins that mimic every detail of complex processes to run many different production scenarios in virtual form, or to plan for supply chain disruptions and other possibilities.
3D simulation software essentially offers a virtual sandbox that allows an unlimited number of refinements to be made to production or process ideas, avoiding any complex major resource requirements or upheavals. When it comes to designing new facilities, simulation software reconfigures layouts to optimize the use of floor space.
Skills shortages as the stumbling block
Many organizations remain unable to access the benefits of Industry 5.0 due to insufficient skills among the current workforce. Research findings by Visual Components discovers that only 41% of US organizations are training employees in the use of new technologies. Utilization rates of robotic equipment is also a key issue, with an average of 34% reported among respondents.
This leads to hindered progress, particularly with implementations. Mistakes lead to reduced resilience and higher costs which could have been otherwise avoided. 17% of US manufacturers are wasting between $31,751 - $63,500 due to errors when deploying robots.
Moving towards simulation technology
Companies must adopt more sophisticated training methods, including simulation. Instead of having employees practice and train with robotic applications directly on the factory floor, offline programming software (OLP) offers a viable alternative. OLP provides a precise digital replica of the robot and its work environment, simulating its motions and operations via simulation. This approach leads to well-planned, fully optimized deployments that are more adaptable and flexible, easily adjusting to new requirements, opportunities or limitations.
Cobots significantly impact factory operations, yet they require human intervention for programming and maintenance. Traditional manual programming of these robots can be a lengthy process, often taking weeks to get the robot operational. However, with OLP, manufacturers can streamline the process of fine-tuning the movements and workflows of cobots for automation, reducing the time taken with manual programming.
Instantly accessible features in the software can enable education of workers on programming and managing cobot deployments, thereby enhancing their skills in emerging technologies. Instead of supplanting human professionals, these platforms serve to augment their expertise and address the talent shortage, a critical aspect of Industry 5.0. By embedding precise and consistent knowledge within the software, manufacturers can mitigate the risk of specialized skills and knowledge being concentrated in a handful of seasoned experts, who might take it with them upon departure or retirement.
If manufacturers are to fully capitalize on the advantages of robotic implementation and process automation, it’s essential they have access to technologies that enhance the skills of their workforce, preparing them for a new era marked by productivity, efficiency and resilience. The most successful and profitable path forward depends on the right blend of human talent and advanced technology.
Comments (0)
This post does not have any comments. Be the first to leave a comment below.
Featured Product
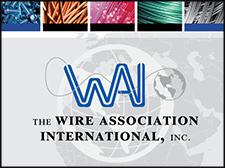