Smart Manufacturing – A Layered Approach to Digital Transformation
According to the Plastics Industry Association, the average utilization percentage of a plastic injection molding machine is only about 40%. This is the percentage of the total times when the machine is used to produce products that can be used or sold. Other times are just overhead or simply wasted – e.g., setup, waiting for raw materials, etc. The same kind of machine utilization, or lack thereof, is likely to be found in other industries as well. But for a company to be a world-class manufacturer, machine utilization should be around 85%, which is often considered the gold standard. This is a huge gap. If companies can achieve this utilization rate, they would double their productivity without investing in any extra resources or time.
Smart manufacturing, sometimes synonymous with the “connected factory,” or Industry 4.0, aims to achieve optimal efficiency in manufacturing by digitally transforming operations. One of the main goals of digital transformation is to transform the shop floor into smart manufacturing to help manufacturers to manage their core production operations digitally to maximize the production by minimizing machine downtime and quality losses.
But smart manufacturing includes different layers. Starting with the hardware systems like machines and sensors, having automation tools and PLC systems and then having a Manufacturing Execution System (MES) or Manufacturing Operations Management (MOM) system to complete the journey. MES/MOM helps manufacturers to collect real-time data from hardware and automations tools, and then be integrated with their Enterprise Resource Planning (ERP) systems. This integration allows ERP systems to have the complete visibility at the enterprise level to manage inventories, resources, procurements, financing, work order planning, and more.
Often, we hear about Overall Equipment Effectiveness (OEE) as it is the gold standard for measuring manufacturing productivity. But what is OEE?
- OEE = Availability x Performance x Quality
- Availability = (Total Hours Planned - Lost Time) / Total Hours Planned
- Availability, for example, can tell you why a line has not run continuously during a shift.
- Performance Rate (efficiency) = Actual Machine Speed / Design Machine Speed
- Performance is measured by calculating ‘Performance Loss’, which accounts for anything that causes the manufacturing process to run at less than the maximum possible speed. Examples of Performance Losses include machine wear, substandard materials, misfeeds, and jams.
- Quality Rate = Number of Good Products / Total Products Made
- Quality loss accounts for manufactured products that do not meet the required standards, anything that must be scrapped or reworked.
Many experts point out three stages for successful digital transformation and smart manufacturing:
- Monitoring Stage: Getting the data from the machines. Without the data, you cannot do real time management of the shop floor. This step does not require the involvement of operators or technicians. You can collect the data in the background.
- Digital Stage (Improvement Stage): Operators, technicians and supervisors can see the performances of the machines in real time. This stage allows the shop floor to improve upon the data they see. For example, has the machine stopped due to mechanical failure or process failure (i.e., is the setup taking too long)? Are you waiting on the raw material? This step leads to continuous improvement.
- Connected or Digital Manufacturing Stage: Product and work order data become part of these data and are integrated with a manufacturer’s ERP system.
Companies need to focus on having proactive shop floors instead of reactive ones. Reactive manufacturing sees problems as they happen (e.g., machine stops, lack of coordination, etc.) and scrambles to react to the problems. In contrast, proactive manufacturing enables manufacturers to predict the problems and take appropriate measures to prevent them. This increases efficiency on the shop floor – the ultimate goal of smart manufacturing.
Comments (0)
This post does not have any comments. Be the first to leave a comment below.
Featured Product
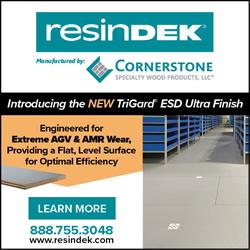