Managing the Rising Issue of VOCs in Modern Manufacturing
Volatile organic compounds, or VOCs, are gases that come from particular solids or liquids. The VOCs can cause short- and long-term health issues when inhaled.
Given the industrial nature of their operations, modern manufacturing plants, and the activities performed there, are often significant sources of VOCs. Thus, company leaders must take decisive steps to mitigate the threat.
Know the Main Sources of VOCs
A good starting point is to know which parts of the manufacturing facility have VOCs and which production phases cause them. For example, manufacturers that make dairy products know volatile organic compounds are released during the yogurt fermentation process. Some companies use digital olfaction technology to measure the associated odors and maintain consistent quality control.
The manufacturers of products such as paint, oil-derived compounds and lubricants are also at an above-average risk of emitting VOCs in their plants. VOC emission is not necessarily an issue at every production stage. However, people cannot take meaningful steps to mitigate dangers while remaining unaware of where VOCs originate.
One practical option is to perform a volatile organic compound assessment. It can tell manufacturers which parts of a plant have the most VOCs and which workers are at the highest exposure risks.
One investigation of an oil refinery in Iran categorized VOC threats by cancer and non-cancer risks. The results showed significant air quality differences in the refinery and effluent storage pit areas. Moreover, the levels of some VOCs, such as benzene and toluene, were higher than the limits established by regulators.
That example highlights the necessity of taking samples from various plant areas to see how they differ. Otherwise, people may not get a complete picture of the VOC concerns and concentrations within a factory.
Make Conscious Decisions to Reduce and Monitor VOCs
Manufacturers aren’t the only ones that must stay aware of VOCs and make specific decisions to reduce them. VOC emissions from flooring can be present in all rooms of homes with poor ventilation. Thus, many homeowners and landlords opt to install low-VOC flooring in their properties. Similarly, manufacturers can use low-VOC products in many parts of their processes. Doing that doesn’t eliminate them, but it can reduce concentrations throughout the plant.
Another option is to install gas-detection systems throughout the plant. They continuously monitor the environment and alert people to dangerous levels. Some have LED screens and audible warning systems to ensure threats aren’t missed during the workday.
It’s also important to assess which process changes could make the biggest impacts on VOC emissions levels. It can take anywhere from 20-40 hours for a person to paint their car at home. Thus, many vehicle owners decide to have it professionally done. Automobile manufacturers face many of the same VOC risks as auto body shop workers since they both deal with paints and primers.
However, mitigation steps are easier than people often think. One shop used an alcohol-based surface cleaner to wipe parts before painting them. That resulted in less toxicity, helping to manage VOCs at the business. Another option is to switch to water-based paints from solvents.
Implementing changes takes time and effort, but they often pay off in the long run. Manufacturers can also satisfy regulatory requirements by showing that they’re doing everything necessary to keep VOC levels down.
Switching to specialty products can also often make a meaningful difference. The bonding agents in electronics manufacturing cause more than 80% of VOCs. However, one way to reduce them is to use plasma-based processes that eliminate solvents. Such approaches typically get results comparable to solvent-based methods without the VOC emissions.
Recognize How to Keep Employees Safer
Many employers establish safety protocols for employees without realizing that some practices can endanger workers. One study found that particle-filtering half masks made from polymer fleeces emit VOCs and require special consideration. Those face protectors became especially popular during the COVID-19 pandemic as people investigated the best ways to stay safe. However, people in certain manufacturing roles also rely on them since they filter out specific kinds of dust.
Another study focused on people who self-reported exposure to various workplace hazards, including VOCs. The research concluded that patients diagnosed with amyotrophic lateral sclerosis (ALS) were more likely to report higher levels of work-related exposure to VOCs, metals, particulates and other hazards before their diagnoses than those not around those things.
Employers must take a multipronged approach to reducing risks. They can start by using some of the low- and no-VOC products available on the market. Another preventive measure is to control leaks of products containing VOCs. Making it easy for employees to report issues is a great way to help them feel empowered by and accountable for VOC reductions.
Increased ventilation can help disperse VOCs. Thus, employers should verify which areas of the plant are most likely to give employees the highest exposure rates and act accordingly to increase or maintain ventilation as needed. Local exhaust systems are particularly beneficial for the areas of a manufacturing facility where VOCs are most likely to build up. Periodic medical checkups can also help employers manage exposure by warning them to act before people suffer long-term consequences.
One study checked for VOCs in the blood of workers occasionally exposed to them. They included people involved in tasks such as textile dyeing and using paints, paint thinner and shoe polish. The results showed that approximately 70 of 80 people had VOCs in their blood samples. Moreover, a statistical analysis showed a strong relationship between work experience, working hours and diseases. That suggests VOCs were a factor in some of those ailments.
No Single Best Management Method
Volatile organic compounds are naturally occurring, but the issues begin when their related gases enter the surrounding environment. Many manufacturers have no choice but to use some VOC-containing products in their workflows.
However, as the examples here show, people have plenty of options for exposure reduction. It might entail using products with fewer or no VOCs, switching to other processes or taking various precautions to protect employees.
The main thing to remember is that VOC management must remain a top-of-mind concern. It’s not something leaders should prioritize for a few weeks out of the year before moving on to other things. The effective management of VOCs requires a methodical approach and periodic checks to ensure preventive methods are working as well as expected. If they aren’t, it’s time to make further tweaks to ensure the intended outcomes.
It’s also a good idea to listen to employees. They often have feedback about things leaders hadn’t previously considered because they don’t engage in the same day-to-day tasks as the workers. Employees who feel heard and respected are more likely to play their part in reducing VOC exposure at work.
Comments (0)
This post does not have any comments. Be the first to leave a comment below.
Featured Product
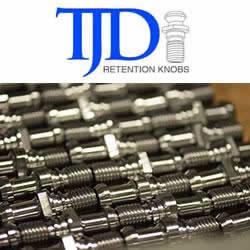