5 Amazing Ways Automation Benefits Fabrication
Most sheet metal fabricators seek ways to improve productivity and become more efficient to stay competitive. Automation has evolved significantly in the past few years, and a growing number of solutions can provide significant value to companies.
These are five of the most important ways automation benefits fabrication and how shops can use it to their advantage.
1. Improving Worker Safety
Any automated solution can help reduce the number of tasks workers need to complete — potentially making a workplace much safer.
People face several threats in a metal fabrication shop. Critical tasks like welding, brazing and cutting are inherently dangerous, and the heavy equipment necessary to move and pack raw materials can also generate safety hazards. Risky, dull and repetitive tasks are often great candidates for automation, which will help keep workers safe.
Staff in fabrication plants face significant safety risks — including heavy equipment and repetitive motions that can lead to musculoskeletal injuries (MSIs). Most fabrication automation solutions will reduce the amount of dangerous or repetitious work these employees need to perform.
For example, one business could use a six-axis picking robot that can repeatedly bend or stretch to move materials around a metal fabrication plant. Another company may use a collaborative robot (cobot) capable of machine tending or supporting a worker performing tasks like setting up metalworking machinery or making measurements.
These robots won’t get bored or tired over the course of a shift, reducing the risk that fatigue may lead to a safety incident or injury.
Even if an automation solution doesn’t entirely eliminate a task or replace a worker, it can still help protect people from some safety threats that come with metal fabrication work.
2. Reducing Labor Costs
Metal fabrication faces a tight labor market, like many other manufacturing sectors. Hiring cycles are taking longer as a result, and the average cost of labor is steadily increasing. Additionally, increased labor costs in India and China are making overseas costly and therefore less attractive. Reshoring operations and investing in more robotic equipment can help reduce labor costs.
In the same way automation can keep workers safe by handling tasks that typically require human labor, it also reduces the overall cost of fabricating metal products. A robotic welder could reduce the amount of work necessary to complete welding tasks. This could drive down overall production costs and make the shop more flexible.
The machine doesn’t need regular breaks and is available at all times — with a few exceptions, like downtime for maintenance — so scheduling and timing work may be easier.
Whether they replace or support human workers, robots and automated systems can make sheet metal fabrication much more cost-effective. As the price of labor continues to rise, along with the cost of resources like necessary raw materials, reducing expenses will become even more of an important benefit of automation for fabricators.
3. Minimizing Waste
When properly set up and programmed, robotic automation will always produce parts or products within the right tolerances. The system can automatically notify site staff if the process veers toward upper or lower tolerance limits, allowing them to take quick action to keep fabrication on track.
Some tools, like 3D printers for metal manufacturing, can also leverage the unique powers of additive manufacturing to drive down waste. These tools only use the materials necessary to create a new part, so they can minimize the generation of scrap metal, shavings and other items a shop would normally need to repurpose.
At the business level, robotic process automation, AI analysis and other automated tools can improve administrative processes to cut down on waste. These trends, along with robots, can help streamline plant operations significantly.
A business process automation solution can help managers bring together the company’s information systems. These tools can also automate repetitive digital tasks — like invoice generation, quote estimation, and the organization of important files or emails.
Managers can leverage this technology to streamline administrative work and reduce the risk of administrative errors. This helps cut down on waste that can come from mistakes like overstocking on raw materials or miscommunications with clients.
4. Improving Product Quality
Automation solutions can improve the overall product quality of a shop. Automated metal fabrication machines are extremely consistent. Proper oversight and management allow them to operate for multiple shifts without decreasing productivity or consistency. As a result, workers can count on the equipment to produce the same results every time they use it.
By contrast, it’s normal for product quality fabricated through manual processes to vary somewhat, as worker fatigue, shift changes and varying skill levels impact process consistency. Over the course of a day, workers may become tired, make mistakes and allow errors to slip through the production process.
Automated fabrication and quality control solutions may make fewer mistakes. The ones they do make are often more consistent, allowing process errors that lead to a lower product quality to be identified and hammered out more easily than those made intermittently.
Fabricators that need to improve the quality and consistency of their products can benefit significantly from the right automation solution.
5. Reducing Lead Times
Most fabricators face growing pressure from clients to create products faster and with less advance notice. However, driving down cycle and lead times can be challenging, especially as supply chain instability makes it more difficult to rush-order or stock up on essential raw materials.
Automation makes it much easier to drive down shop lead times. It can reduce delays due to tasks that normally must be completed manually — like picking and placing, generating invoices and ordering raw materials.
Even if workers aren’t available to handle certain tasks, like moving materials, automation can ensure production will continue. The right solution can be an invaluable investment for businesses that need to decrease cycle or lead times.
Automated Fabrication Shops Are More Efficient
Changing market conditions, a labor shortage and ongoing supply chain disruptions have forced metal fabrication plants to adapt fast.
Automation is often a powerful tool for businesses that need to reinvent or optimize their workflows. The right solution can help fabricators make their work safer, more economical and less wasteful.
More sophisticated automation technology is becoming available due to technology like AI. Investing in these solutions now will allow fabricators to take full advantage of these innovations as they become more accessible.
Comments (0)
This post does not have any comments. Be the first to leave a comment below.
Featured Product
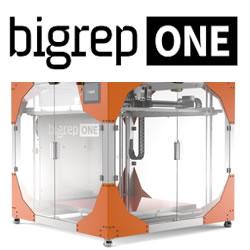