4 of the Most Important Safety Practices in Automated Factories
The manufacturing sector increasingly relies on factory automation to reach targets and keep quality levels high. However, no matter if a facility is fully or partially automated, there are essential safety practices to follow. Here are some of them.
1. Determine How Each Protocol or Process Supports Safety
People will be more likely to follow safety practices if they recognize the value behind them. Getting feedback from workers about what makes them feel unsafe and why is an important initial step in confirming where room for improvement exists. Many automated processes in factories bring more than safety benefits. However, if leaders focus on why doing things in certain ways keeps people safe, compliance levels should rise or stay at high levels.
One multinational manufacturer of baked goods moved to an automated process for weighing flour and sugar. Workers previously did this manually by pouring up to 220 kilograms of those products into kneaders from 40-kilogram containers. This taxing job led to injuries, measurement inaccuracies and foreign objects entering the ingredients during the transfer. Those issues put workers and customers at risk and sacrificed productivity.
The company has since automated this process by using a closed system where the ingredients come from 75-ton silos fed from tanker trucks. This shields them from environmental exposure or human handling. The update brought a margin of error of less than 1% and kept workers safer by eliminating discomfort and strain.
Before investing in an automated solution or making any process changes, factory leaders should determine whether doing things differently enhances safety. Not all automation does, but it often can if leaders implement it correctly. On the other hand, if automation somehow increases safety risks, it’s important to redesign processes to mitigate them.
2. Base Rules Around Safety Assessment Results
Factory leaders will likely overlook some safety needs without carrying out assessments to see where gaps exist. The early steps of this process concern the applicable parties identifying and ensuring they understand all the regulations and codes associated with their operations.
Checking the existing machine guards is a good next step. The kinds used will vary depending on the type of equipment and what a company does with it. Also, the guards become useless if workers disable or don’t know how to use them.
Any risk assessment aims to identify potential hazards and their severity, then take the correct steps to mitigate them. In many cases, getting rid of the risks is impossible. However, the next best thing is to minimize the time that a threat exists. When examining the potential hazards, people should look at the primary and secondary factors. Doing that gives them a clearer picture of how and when workers could encounter danger.
35% of manufacturing workplace accidents stem
Leaders should also consider how an automated factory’s environment may make it harder to stay safe. Excessive workplace noise can elevate danger by making it harder for people to communicate. Spending too much time in a loud place also poses a hearing loss risk. If a factory has slick floors, posting signs reminding people to walk slowly could help. Adding textured tape, mats or other accessories to improve traction is also advisable.
Decision-makers that evaluate an automated factory’s risks should base safety practices around those threats. They should explain how following the rules will keep them safer and invite workers to come to them with any questions or concerns.
3. Keep Machines Properly Maintained
Staying on top of machine maintenance is a huge part of workplace safety. Decision-makers at some plants choose to put off upkeep until something goes wrong. They believe that approach will help them save money. However, it can also increase the likelihood of dangerous incidents, such as explosions or fires.
Researchers determined that about 35% of manufacturing workplace accidents stem from production equipment malfunctions. Facility managers are more likely to notice something’s wrong before it’s too late if machines are checked on the recommended schedule.
There’s even more potential when people go with predictive maintenance for factory machines. Advanced algorithms detect characteristics humans may miss, such as an elevated temperature or abnormal vibration.
The benefits go beyond safety, too. A study found that factories could save 8%-12% by choosing predictive rather than preventive maintenance. Encouraging all team members to take ownership of machine checks is a great way to build and maintain a strong safety culture.
If a worker believes it’s someone else’s responsibility to handle maintenance, they won’t see the value in going through a machine checklist before using it. However, they should take things more seriously after understanding the shared responsibility of equipment upkeep.
4. Provide the Proper Training and Gear
Workers will only be well-equipped to be safe in automated factories if they have the necessary training to operate various machines. Decision-makers should set aside time for education sessions and realize it’s not sufficient to give someone one hour or day of training and think they’re set for life.
They should also consider that people learn differently. Although some learners prefer highly interactive content, others would rather read from textbooks. Another consideration is that if employees primarily work on the factory floor, many won’t have offices with desks for training. One way to address that could be to create a training station with laptops or tablets that people share and use at designated times.
Safety practices also extend to what people wear when on the job. If possible, workplaces should offer employees options to get approved gear at discounted prices or at least have the amounts deducted from their paychecks. When people perceive they can easily get replacement gear, they’re less likely to keep using items that are too worn out to serve their purpose.
Workplaces that do not provide attire for workers should at least give clear guidance on acceptable versus unacceptable options. That way, people have the information they need to purchase the items most likely to keep them safe.
Automated Factory Safety Requires Forethought and Commitment
An automated factory is not necessarily safe because it’s full of advanced machines that include features to protect workers. Leaders must also take proactive steps to determine the risks and how to minimize them. Following the suggestions here will get them off to a strong start, but they must also realize that maintaining a safe workplace is an ongoing effort.
Comments (0)
This post does not have any comments. Be the first to leave a comment below.
Featured Product
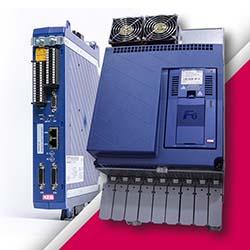