What Is a Load Bank and Why Do Manufacturers Need Them?
A load bank can be an important asset in a variety of industries. Load banks are stationary or portable tools that mimic the expected electrical load on a power source in a commercial or industrial setting.
As we’ll see, this setup is useful in many fields — including in the manufacturing industry. Manufacturers need a way to make sure their power sources deliver the consistency customers require. Meanwhile, customers in the field need tools to perform ongoing testing of their primary and secondary power sources for peace of mind.
What Are Load Banks?
Load banks mimic the power load — such as the total electricity draw — on a source of power during everyday operations, which involves several steps:
- The load bank develops an electrical load.
- The load bank applies the electrical load to the power source.
- The load bank dissipates the power output safely.
Load banks may be stationary or portable depending on the applications, which we’ll discuss in more detail presently.
Both types include everything needed to replicate and confirm real-world power demands on industrial power systems. That includes load elements plus load protection, control and metering tools, as well as accessories for niche-specific industrial purposes.
Load banks can test power sources ranging from battery systems and wind generators to massive engine generator sets and aircraft or watercraft generators. It’s important to note that the original source still provides the power, but the load bank deploys and dissipates this energy safely while testing the power source under realistic but controlled circumstances.
The question is, why is this useful?
How Are Load Banks Used in Manufacturing?
Electrical engineers could wish to mimic a full power load for a number of reasons. In general, they’re used to test and calibrate the performance and efficiency of an available power source. A more specific application is to ensure the proper functioning of an auxiliary power source before an outage knocks out the primary source.
Uses for load banks in a manufacturing setting include:
- Engine cell testing: Manufacturers use load banks to test the performance of their new engines. Using variable mechanical loads and dynamometers, engineers can fine-tune how the engine functions to ensure it delivers power efficiently no matter the circumstances.
- Generator cell testing: Standby generator manufacturers use load banks in a similar fashion to appraise the stability and resilience of generator power units. In this scenario, the load bank assists with calibrating the generator to bring its performance in line with tolerances.
Whether it’s the original equipment manufacturer performing the testing or one of its customers, load banks are the right tool for appraising, measuring and adjusting the performance and output of a power source.
What Are the Different Types of Load Banks?
Although there are many form factors and industry-specific applications for load cells, there are two primary formats to be aware of. These are resistive and reactive load banks. Some manufacturers may need one type, while others may need the other or both.
Here’s a rundown of the differences between the two types:
- Resistive load banks: These are the more common of the two because they mimic a standard capacitive power load and then draw it from the generator, such as the load created by household appliances and heating or light sources. They do not measure full apparent load, but they do draw a specific load, measured in kW, to help confirm that the engine, exhaust and cooling system all function as expected.
- Reactive load banks: On the other hand, reactive load banks can also simulate inductive loads — those which convert electricity into a magnetic field — as well as capacitive loads. The former is more common in commercial settings and on construction sites. Other places where reactive load banks are useful include hospitals and data centers.
Resistive load banks convert the applied energy into heat. The larger the kW load of the bank, the more likely it is to have its own airflow and cooling apparatus. You’ll typically find self-contained models that range up to 3,000 kW.
Reactive load banks test the full apparent load in kVA (Kilo-volt-amperes) of an asset using a simulated inductive load. This type is common on construction sites or to test backup power sources for business facilities.
To further compare the two, remember that resistive load banks generate a 1.0 power factor at a load of 100%, while reactive load banks have a 0.8 power factor at a 75% load. The power factor and load differences mean resistive loads may result in a generator voltage drop. Consequently, reactive load banks are needed to test systems for their vulnerability to voltage inconsistency.
Load Banks for Manufacturers and Beyond
As you can probably tell, load banks serve an important function in industry today. Above all, they provide peace of mind. Knowing that a facility can continue meeting its needs and productivity goals, even during a power outage, can be priceless.
Comments (0)
This post does not have any comments. Be the first to leave a comment below.
Featured Product
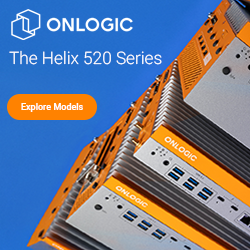