How to Keep Manufacturing Employees Safe During Coronavirus
For manufacturers, the safety of their employees is always at the forefront of their minds. You want to keep your workers safe at all times, so events like a global pandemic can be troubling. How do you balance productivity while making sure you don't contribute to spreading the virus?
You can find plenty of general health guidelines, but you need to know actionable specifics. OSHA released a list of safety measures for manufacturers, but it doesn't go into much detail. To help clarify, here are 10 specific tips for keeping employees safe during COVID-19 and how to enact them.
1. Identify High-Risk Employees
The first step in creating a safe, healthy workspace is identifying those who are at the greatest danger. COVID-19 disproportionately affects some groups, such as the elderly or those with preexisting health conditions. Identify any high-risk employees at your facility and encourage them to stay home.
If these employees can't afford to miss work, see if you can isolate them. Keep them on a more flexible schedule or place them further away from other workers. If anyone shows symptoms of sickness, require them to self-quarantine for at least two weeks.
2. Enforce Social Distancing
You've doubtlessly heard of social distancing guidelines at this point. Maintaining a six-foot distance from one another reduces the risk of spreading the virus, should someone have it. You should work to enforce these guidelines at your workplace, ensuring employees stay six feet apart.
Create specific lanes so that workers don't come near each other when walking through the facility. In break rooms, limit occupancy to one person per table, and post signage to remind everyone. You may have to rearrange some things to allows people to work six feet apart, but safety is worth the extra labor.
3. Work Remotely Whenever Possible
Some workplaces can transition to remote work, but this isn't always possible for manufacturers. That doesn't mean you can't consider work-from-home opportunities at all, though. If you have any office staff, consider allowing or even requiring them to work from home.
If you need to hold any meetings, host them over video-conferencing software. The more you can have people work from home, the fewer people have to be in the building at once. You may not be able to enable remote work for everyone, but you can do it for some.
4. Restrict Access to the Facility
Limiting the number of people in your facility applies to visitors too. You need to know who's in your building at all times and why they're there. To help in that regard, you may want to consider increasing your perimeter security.
Automated security gates can help you limit access to authorized staff without needing a guard post. If you can afford it, consider installing one or two and issue keycards to essential employees. Now is not the time for hosting tours or visits from outsiders to your facility.
5. Use Medical PPE
Issuing personal protective equipment (PPE) is a standard practice in the manufacturing industry. Given the threats of COVID-19, you should expand the required PPE to include medical equipment. Issue face masks that cover employees' mouths and noses to decrease the risk of spreading the virus.
Gloves can also be a helpful resource, but only if you change them frequently. If you use the same gloves throughout the day, they'll gather the same amount of germs as if you weren't wearing them. In some areas, medical PPE is hard to come by, but try your best to provide it.
6. Restructure Schedules
Another step in maintaining social distance is restructuring employees' schedules to limit occupancy and interaction. If you currently operate on a two-shift schedule, consider moving to a three or four-shift one instead. You can then stagger these shifts so that people only work and break around the same people every day.
You could arrange these schedules so that different crews work on different days. If one person gets sick, you'll limit the number of people they could infect by doing this.
7. Clean Regularly
Make sure you're taking the time to clean all surfaces thoroughly. Require workers to sanitize their stations at the end of their shift to protect incoming employees. Train everyone on the CDC's guidelines for workplace cleanliness to make sure they know how to clean correctly.
You may also want to take one day a week for deep cleaning as well. Set aside time to disinfect the facility more thoroughly when you reorganize your schedule. You may consider using dedicated sanitation staff for these times.
8. Separate Vital Personnel
In every manufacturing facility, there are employees without whom the operation can't run. Identify who your vital personnel are and take measures to separate them from the rest of the workforce. Prohibit anyone from entering the area where they work to ensure they don't get sick.
These key personnel will probably need unique schedules to keep them isolated. It may seem like a lot of work, but their health and the success of your facility depends on it.
9. Consider Automation
Keeping employees distant and requiring at-risk workers to stay home can put more stress on your operation. If you have the means, consider turning to automation to alleviate some of this stress. Cobots can help fill the gaps left by missing workers or help transfer items from one place to another.
Mobile robots can carry products or materials throughout your building, so employees don't have to. That way, you can move packages without needing employees to get close to one another. If you have a smaller staff because of the virus, automation can also help you maintain the same level of productivity.
10. Communicate Continually
The final and one of the most critical steps you can take is communicating with your staff regularly. If any new health and safety guidelines come out, pass them along to your employees. Send frequent updates about local COVID-19 news so they can stay informed about health risks.
In communicating frequently, you'll both reinforce essential practices and help improve morale. The pandemic has created confusing times for everyone, so a consistent source of information can be a relief.
Safety Remains a Chief Concern
If you've been in the industry for any amount of time, employee safety is a chief concern of yours. In this pandemic, that emphasis on health and safety comes in handy. By keeping your employees' best interests at heart, you can find ways to reduce the spread of COVID-19.
Comments (0)
This post does not have any comments. Be the first to leave a comment below.
Featured Product
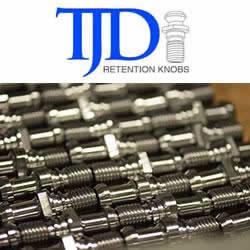