How GE Appliances Built an Innovation Lab to Rapidly Prototype Products
Bharat Kapoor, Kevin Nolan Natarajan (Venkat) Venkatakrishnan for Harvard Business Review: Many large companies yearn to rekindle the innovative magic of entrepreneurship, but very few actually succeed. The reasons have been well documented and include:
- Large, established companies answer to investors who value predictable, consistent financial results, and so are intolerant of the risks inherent in bold innovation.
- Career advancement in mature companies usually demands avoiding conspicuous failures, while entrepreneurs must fail repeatedly to get ahead.
- Large companies serve mainstream customers, while innovative entrepreneurs first serve early adopters.
For these reasons and more, it is generally futile for large companies to ask: “How can we act like a fast, lean, risk-taking startup?” You can’t. Which means that it’s time for a new approach. Large traditional organizations now struggling to adapt to the fast-paced, risk-filled digital age would do well to consider FirstBuild, an experiment at GE Appliances that is showing real promise.
The FirstBuild Experiment
Midway through 2014, GE Appliances launched FirstBuild — a GE-equipped innovation lab and micro-factory — to augment the strengths of a long-established company with those of an entrepreneurial startup. Separation is the key. As a free-standing enterprise operating under its own brand, FirstBuild is decidedly not another attempt to transform a traditional company’s corporate culture. Full Article:
Comments (0)
This post does not have any comments. Be the first to leave a comment below.
Featured Product
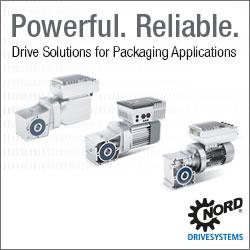