Boy, do Fanuc and Cisco have a deal for your factory
Fanuc and Cisco Systems are set to commercialize a technology this summer that promises glitch- and disruption-free factory operations. The Internet of Things-based system monitors machinery and spots signs of possible abnormalities so that parts can be replaced more smoothly and without affecting operations.
A one-minute suspension at a car factory generally costs around 2 million yen ($16,900). If, for example, a gear breaks and operations are halted for 60 minutes to replace it, the costs would be 120 million yen. Frequent line stoppages could also affect product quality.
The Fanuc-Cisco system uses sensors attached to each robot carrying or welding parts to monitor temperatures, vibration and other conditions. Data streams are sent via the Internet. A computer analyzes the data and decides which parts will likely need fixing and when. The system also places orders for replacements. The accuracy of the system's prediction and analysis functions will increase as data accumulates, representatives from the companies said. Cont'd...
Comments (0)
This post does not have any comments. Be the first to leave a comment below.
Featured Product
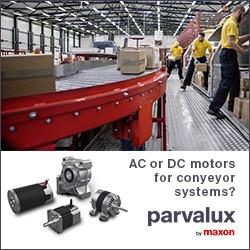