Palletizing Robot Accelerates the Adoption of Unmanned Factories in the Food Industry
With the rapid advancement of artificial intelligence and automation technology, "unmanned factories" are being widely implemented across various industries, further driving the demand for Industrial Robot solutions. Among them, the Palletizing Robot has become a key automation solution in the food industry, offering high efficiency, reliability, and low energy consumption.
With the rapid advancement of artificial intelligence and automation technology, "unmanned factories" are being widely implemented across various industries, further driving the demand for Industrial Robot solutions. As the core force behind unmanned production, Industrial Robots play a crucial role in manufacturing enterprises' intelligent upgrades. By integrating artificial intelligence and computer-controlled systems, these robots can autonomously perform repetitive, high-risk, and labor-intensive tasks, significantly improving operational efficiency and standardization. Among them, the Palletizing Robot has become a key automation solution in the food industry, offering high efficiency, reliability, and low energy consumption.
Palletizing Robot Enhances Efficiency in Food Processing
A Palletizing Robot is primarily composed of a flattening conveyor, buffer conveyor, positioning conveyor, pallet warehouse, pallet conveyor, grouping machine, pushing device, palletizing mechanism, and pallet discharge system. Its optimized design ensures smooth and reliable operation, with a fully automated palletizing process that requires no human intervention during normal operations. This enables widespread application in food packaging, logistics, and warehouse automation.
Advantages of Palletizing Robots in Food Production
1. Simple Structure & Low Failure Rate - Fewer mechanical components lead to reduced maintenance costs.
2. High-Speed & High-Output - Meets the demands of food production lines with consistent performance.
3. Multi-Box Handling Capability - Can grab and stack two to six boxes simultaneously, improving efficiency.
4. Hygienic & Safe Operations - Eliminates manual labor, reducing contamination risks. Automatic wrapping and waterproofing ensure food safety.
5. Compact Footprint - Requires minimal space, maximizing storage capacity.
6. Versatile & Adjustable - Can be customized based on packaging size, weight, and pallet dimensions.
7. Energy Efficient - Low power consumption reduces operational costs, and user-friendly controls simplify operations.
Expanding the Scope of Industrial Robots in the Food Industry
In addition to Palletizing Robots, Material Handling Robots, and Cooperative Robots are transforming the food industry by optimizing logistics, packaging, and warehouse operations. Material Handling Robots automate the transportation of goods, reducing manual handling risks, while Cooperative Robots work alongside human operators to enhance flexibility and precision.
As China transitions from a manufacturing powerhouse to an advanced manufacturing leader, the widespread adoption of Industrial Robots in the food industry underscores the immense growth potential of automation technology. With over a decade of expertise in robotic solutions, our company provides a comprehensive range of automation equipment, including palletizers, automatic loading machines, depalletizers, conveyor systems, steam recovery units, steam generators, and fully automated packaging lines. Our solutions are widely applied in the grain, food, beverage, pharmaceutical, chemical, fertilizer, cement, glass, steel, and building materials industries, driving the next phase of smart manufacturing.
Featured Product
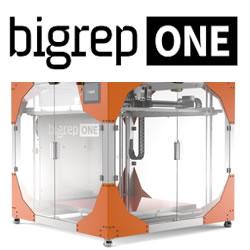