Velo3D Introduces New Rapid Production Solutions - Significantly Expands Addressable Market to Meet Growing Demand for High-Quality Production Parts
-Latest Offering Enables Additive Manufacturing at Unpresented Scale and Speed -Rapid Production Solutions Expected to Account for Up to 40% of Revenue in 2026
Velo3D, Inc. (OTC: VLDX) - a leader in additive manufacturing (AM) technology known for transforming aerospace and defense supply chains through world-class metal AM, is proud to unveil its latest offering, Rapid Production Solutions (RPS). Customers can now leverage Velo3D's production cells for surge capacity, enabling rapid scaling without significant capital investment. This solution is designed to meet the growing demand for scalable, high-quality production parts. RPS enables customers to build U.S. based, resilient supply chains for production parts across industries, including aerospace, defense, energy, and others.
Making AM More Accessible, Affordable and Scalable
The introduction of RPS is a direct response to the industry's need for flexible, efficient, and repeatable production solutions. With RPS, Velo3D is empowering customers—whether OEMs, contract manufacturers, or primes—with a clear, reliable path from concept to production, backed by Velo3D's deep engineering expertise, cutting-edge technology and a fleet of Sapphire XC large-format metal 3D printers.
Arun Jeldi, CEO of Velo3D, shared his perspective:
"At Velo3D, we are committed to enabling our customers to scale with confidence. Rapid Production Solutions are designed to accelerate the adoption of additive manufacturing by providing flexible, high-quality solutions that are rapidly tailored to each customer's unique production needs. This capability seamlessly compliments our success in supplying metal AM hardware systems to today's leading OEM's, accelerating AM adoption. By combining our technology, deep expertise, and robust ecosystem, we're not just meeting industry demand—we're helping shape the future of manufacturing quickly."
RPS: Meeting Customer Demands with Innovation and Flexibility
Accelerating the Path to Production: Velo3D works hand-in-hand with customers to develop application-specific solutions, enabling rapid innovation in production-ready manufacturing. With a focus on aerospace, defense, energy and other industries - companies can shorten design cycles and reach production qualification faster.
Ensuring Consistent, High-Quality Parts: Reliability and consistency are critical for customers seeking to scale production. RPS integrates metrology, software, process control tools, and data-driven solutions, ensuring predictable output and rapid qualification across diverse industries.
Flexible Production Supply Chains: Understanding that each customer has unique needs, RPS offers multiple production pathways:
Vertically integrate AM production within the customer's own operations.
Partner with contract manufacturers to expand capacity without significant capital investment.
Leverage Velo3D's production cells for scalable surge capacity, allowing rapid scaling without significant capital investment.
Success in Action
"Velo3D's RPS achieved more in four months than we were able to accomplish in the previous four years—building 11 large-format proof-of-concept parts across three materials, moving 2 of 11 parts into the production pipeline, and making substantial progress on IN718 material qualification. This was made possible by Velo3D's unique combination of in-house expertise, production cells and patented technological capabilities," said a Supply Chain Executive from a leading aerospace engine manufacturer.
About Velo3D
Velo3D is a leading US based metal 3D printing technology company. 3D printing—also known as additive manufacturing (AM)—has a unique ability to improve the way high-value metal parts are built. However, legacy metal AM has been greatly limited in its capabilities since its invention almost 30 years ago. This has prevented the technology from being used to create the most valuable and impactful parts, restricting its use to specific niches where the limitations were acceptable.
Velo3D has overcome these limitations so engineers can design and print the parts they want. The company's solution unlocks a wide breadth of design freedom and enables customers in space exploration, aviation, power generation, energy, and semiconductor to innovate the future in their respective industries. Using Velo3D, these customers can now build mission-critical metal parts that were previously impossible to manufacture. The fully integrated solution includes the Flow print preparation software, the Sapphire family of printers, and the Assure quality control system—all of which are powered by Velo3D's Intelligent Fusion manufacturing process. The company delivered its first Sapphire system in 2018 and has been a strategic partner to innovators such as SpaceX, Aerojet Rocketdyne, Lockheed Martin, Avio, and General Motors. Velo3D was named as one of Fast Company's Most Innovative Companies for 2023. For more information, please visit Velo3D.com, or follow the company on LinkedIn or Twitter.
Featured Product
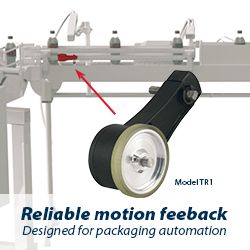