Industrial Control for Process Manufacturing: Optimizing Efficiency and Ensuring Quality
The industrial control for process manufacturing market is experiencing rapid growth as manufacturers increasingly turn to advanced automation, real-time monitoring, and data analytics to optimize production. These sophisticated control systems are revolutionizing how industries manage continuous and batch processes in sectors such as chemicals, food and beverage, pharmaceuticals, and oil and gas. In this post, we explore the market's evolution, key drivers, technological innovations, and future trends shaping this critical segment of the manufacturing industry.
Robust industrial control systems are vital for streamlining process manufacturing. By harnessing advanced automation, real-time monitoring, and sophisticated data analytics, these systems boost production efficiency, ensure consistent quality, and uphold operational safety. In this blog post, we delve into industrial control for process manufacturing, tracing its evolution, outlining its key components and benefits, and examining the trends that are shaping its future.
Industrial control systems (ICS) in process manufacturing are specialized frameworks designed to monitor, manage, and optimize production processes. Unlike traditional manufacturing, process manufacturing involves continuous or batch production methods common in industries such as chemicals, food and beverage, pharmaceuticals, and oil and gas. ICS leverages a combination of technologies—like Distributed Control Systems (DCS), Programmable Logic Controllers (PLCs), and Supervisory Control and Data Acquisition (SCADA)—to maintain precise control over production variables and ensure seamless operations.
The Evolution and Importance of Industrial Control
Over the decades, industrial control systems have transformed the way process manufacturing operates. Initially relying on manual control and basic automation, modern systems now integrate advanced sensors, high-speed data communications, and real-time analytics. This evolution has enabled manufacturers to:
Enhance Operational Efficiency: Automate routine tasks and monitor process variables in real time to minimize waste and optimize resource utilization.
Improve Quality Control: Maintain consistent product quality by automatically adjusting production parameters based on real-time data.
Increase Safety and Compliance: Implement robust safety interlocks and monitoring systems that reduce the risk of accidents and ensure regulatory compliance.
The transformation in industrial control is not only a technological shift but also a strategic imperative for businesses aiming to stay competitive in a rapidly evolving market.
Key Components of Industrial Control Systems
Understanding the core elements of industrial control systems helps in appreciating their role in process manufacturing. Key components include:
Sensors and Actuators: These devices collect real-time data on temperature, pressure, flow, and other critical parameters while actuators execute control commands.
Programmable Logic Controllers (PLCs): Robust and flexible controllers that execute automation tasks and manage process operations.
Distributed Control Systems (DCS): Centralized systems that provide comprehensive control over multiple processes across large-scale manufacturing environments.
SCADA Systems: Enable real-time monitoring and control by collecting data from remote devices, displaying it to operators, and allowing centralized command over distributed processes.
Human-Machine Interfaces (HMI): Graphical interfaces that provide operators with real-time insights and control capabilities, ensuring efficient decision-making.
Together, these components form an integrated ecosystem that supports continuous improvement and operational excellence.
Advantages of Implementing Industrial Control in Process Manufacturing
Adopting modern industrial control systems offers numerous benefits to process manufacturing, including:
Enhanced Efficiency: Automation reduces manual intervention, minimizes downtime, and improves overall productivity.
Improved Product Quality: Real-time adjustments and consistent monitoring lead to uniform product quality and reduced variability.
Cost Reduction: Efficient resource management and predictive maintenance reduce operational costs and prevent costly equipment failures.
Increased Safety: Automated safety protocols and continuous monitoring help prevent accidents and ensure a secure working environment.
Regulatory Compliance: Streamlined data logging and reporting support adherence to industry regulations and standards.
These advantages collectively contribute to a more agile, cost-effective, and competitive manufacturing operation.
Real-World Applications
Industrial control systems are widely implemented across various process manufacturing sectors, such as:
Chemical Processing: Managing complex chemical reactions and ensuring precise control of process variables.
Food and Beverage: Maintaining product consistency and safety through real-time monitoring of production lines.
Pharmaceuticals: Ensuring stringent quality control and regulatory compliance in drug manufacturing.
Oil and Gas: Controlling drilling, refining, and distribution processes to maximize efficiency and safety.
Each of these applications demonstrates how industrial control systems serve as the backbone for modern process manufacturing.
Getting Started with Industrial Control Systems
For businesses looking to adopt industrial control technologies, several steps can help ease the transition:
Assessment and Planning: Evaluate current processes to identify areas where automation and control improvements are needed.
System Integration: Choose the right combination of PLCs, DCS, and SCADA systems that fit your operational requirements.
Staff Training: Invest in training for your team to effectively operate and maintain advanced control systems.
Continuous Improvement: Implement regular system reviews and updates to ensure the control infrastructure evolves with emerging technologies and business needs.
These steps lay a strong foundation for successful industrial control integration, leading to long-term operational benefits.
SEO-Friendly Content Tips for Industrial Control
If you're creating content around industrial control for process manufacturing, consider these SEO strategies:
Target Relevant Keywords: Use phrases such as "industrial control systems," "process manufacturing automation," "DCS in process manufacturing," and "PLCs and SCADA solutions."
Develop In-Depth Guides: Create comprehensive tutorials and case studies that highlight how industrial control systems can optimize production.
Share Success Stories: Use real-world examples and testimonials to demonstrate the impact of industrial control on efficiency and quality.
Engage Industry Experts: Collaborate with industry leaders to produce authoritative content that enhances credibility and drives backlinks.
Leveraging these strategies can help position your content as a trusted resource within the industrial control domain.
The Future of Industrial Control in Process Manufacturing
Looking ahead, the future of industrial control is closely tied to broader technological advancements and industry trends:
Integration with IIoT: The Industrial Internet of Things (IIoT) will further connect devices, enabling more granular data collection and smarter process control.
Advanced Analytics and AI: Incorporating AI and machine learning will enhance predictive maintenance, process optimization, and decision-making capabilities.
Cloud-Based Control Systems: Transitioning to cloud solutions will enable scalable, real-time data processing and remote management.
Enhanced Cybersecurity: As connectivity increases, robust cybersecurity measures will become essential to protect critical infrastructure.
These trends will continue to drive innovation in process manufacturing, ensuring that industrial control systems remain at the forefront of operational excellence.
Industrial control systems are transforming process manufacturing by enhancing efficiency, improving product quality, and ensuring operational safety. With advanced automation technologies, real-time data analytics, and a focus on continuous improvement, these systems provide a competitive edge in today's dynamic manufacturing landscape.
Whether you're modernizing an existing facility or embarking on a new process manufacturing project, embracing industrial control technologies is key to optimizing performance and achieving long-term success. Stay ahead of the curve by leveraging the latest innovations and joining the revolution in industrial control for process manufacturing.
Featured Product
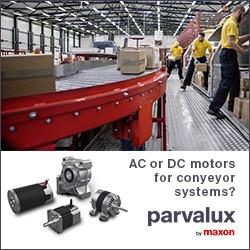