Wilmington Machinery Expediting Delivery of Low-Pressure Structural Foam Machines
While typical lead times for these large machines can range from 9 to 15 months, Wilmington has significantly reduced this wait with in-stock and nearly completed machines available for quick delivery.
Wilmington, NC — Wilmington Machinery, a leader in the design and manufacture of large structural foam machines, is streamlining delivery times for its Low-Pressure Structural Foam machines. While typical lead times for these large machines can range from 9 to 15 months, Wilmington has significantly reduced this wait with in-stock and nearly completed machines available for quick delivery.
Currently available is a 500-ton Low Pressure Structural Foam machine featuring a 50lb shot and a spacious 70" x 80" platen. This machine is ready for shipment within 3-4 weeks of purchase order receipt. In addition, Wilmington is building another 500-ton machine, this one with a larger 100lb shot capacity and an even bigger 96" x 90" platen, which will be available for delivery by May 2025.
Both machines are versatile and can be customized with options such as robotic part removal, gas assist controls, and core pull manifolds, allowing for a tailored solution to fit various production needs.
"By having machines in stock and under construction, we can offer manufacturers a faster path to upgrading their production capabilities," said Jim Boos, VP of Sales & Marketing of Wilmington Machinery. "These machines deliver superior structural foam molding capabilities, and with quick delivery options, we're supporting customers in reducing lead times and getting to market faster."
For more information about Wilmington Machinery's Low Pressure Structural Foam machines or to inquire about customization options, please contact us at wilmingtonmachinery.com.
About Wilmington Machinery Wilmington Machinery has been a trusted name in manufacturing machinery for over 50 years, specializing in plastic processing solutions. Their innovative technology and expertise have provided industries with state-of-the-art machinery for injection molding, extrusion, and structural foam molding.
Featured Product
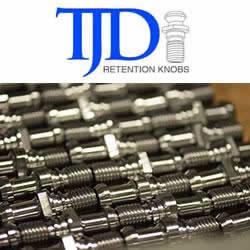