HellermannTyton Announces Second-Generation Application Tools
EVO® cable tie application tools get a refresh.
MILWAUKEE - HellermannTyton released updated versions of its handheld cable tie application tools, the EVO 7 and 9. The new models, called the EVO 7i and 9i, offer visual and functional enhancements in line with the company's ongoing strategy to build the best industrial tools for customers that process wire, cable and tubular bundles.
The manufacturer developed its original EVO 7 in 2013. A short time later, an independent study* compared the EVO 7 with its main rivals and rated the HellermannTyton tool best in class. The EVO 7 and its more powerful sibling, the EVO 9, haven't seen significant updates until now.
"We made mechanical enhancements inside and out," said Product Manager Jamison Soya. "The new tools have been tested to one million cycles, which puts them in a class by themselves."
The EVO 7i tensions and cuts cable ties ranging from 18 to 80 pounds. The heavier duty EVO 9i processes 50- to 255-pound ties including wide strap ties. Both tools come in standard or short hand span models to accommodate all users. An additional model, the EVO 9HT, delivers even higher tensions for applications such as heavy equipment manufacturing.
A key feature of the EVO line is HellermannTyton's patented Tension-Lock-Cut (TLC) technology, which freezes the tensioner before the cut is made, eliminating kick-back. That and an improved, ergonomic handle design help reduce repetitive strain injuries.
Each tool is housed in a lightweight composite body that resists drops and is molded in the company's signature dark blue introduced to the tool segment in 2022.
View more information at www.hellermanntyton.us/evo.
* UWM Center for Ergonomics, 2013
Featured Product
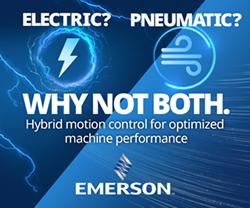
Elevate your manufacturing processes with data-driven insights
Join Emerson at Hannover Messe 2025, Hall 11, Booth C30 and discover how embracing a Floor to Cloud™ strategy can revolutionize your operations. This strategy integrates on-site devices and technologies with cloud analytics, providing the insights needed to enhance manufacturing efficiency, maximize workforce potential, and achieve sustainability targets. Our team of experts have a commitment to innovation and look forward to discussing your challenges to develop a customized solution. Claim your Free Ticket.