MICROMETAL’S PCE PROCESS TACKLES THE COMPLEXITY CONUNDRUM IN MODERN METAL PART MANUFACTURING
In an environment where product intricacies are not merely an aesthetic choice but a functional requirement, PCE stands out due to its precision and versatility.
(17th April 2024, Muellheim, Germany) micrometal Group's photo-chemical etching (PCE) process has emerged as a formidable solution in the area of precision metal part fabrication, adept at addressing the complexity conundrum that modern-day industries face. In an environment where product intricacies are not merely an aesthetic choice but a functional requirement, PCE stands out due to its precision and versatility.
Micro metal part production today is defined by the creation of components that are not only complex geometrically, but which are also highly precise and often delicate. Jochen Kern, Head of Sales & Marketing at micrometal Group says, "This nuanced combination of complexity and fragility is where our PCE process excels, making it an essential technology in the manufacturing of today's high-precision products. With traditional methods such as stamping or mechanical machining, complexity is a cost multiplier. Each new angle, cut, or curve in a component's design often results in the need for more intricate and thus more expensive tooling. Furthermore, the intricate tooling comes with a heightened risk of failure, adding to the unpredictability and cost. Such methods are also bounded by the significant amount of time required to perfect the tooling to ensure the satisfactory completion of the component."
Conversely, PCE operates within a different paradigm. The complexity of a component's geometry does not exponentially inflate costs or lead times. This is because PCE, at its core, is a subtractive manufacturing process that works by removing metal through controlled corrosion, or etching, facilitated by the application of a photoresist and etchant to the material being shaped. The process starts with a digital, or in some instances, glass tooling that imprints the desired geometry onto the metal surface. This tooling is less costly and more rapidly produced than the hard tooling required for stamping or mechanical machining.
Kern continues, "This digital/glass tooling can be as intricate as the design demands without the usual increase in cost or time. It remains indifferent to the complexity of the part's geometry, which is a game-changer for industries that rely on precision engineering. Moreover, since PCE does not involve contact-based shaping, it is intrinsically gentler on the material, reducing the risk of damage to delicate parts. This aspect of PCE is particularly beneficial for components used in sectors like aerospace, medical devices, and electronics, where the integrity of each piece is paramount."
PCE's unique capabilities have far-reaching implications. The technology empowers designers and engineers to push the boundaries of innovation without the looming concern of whether their designs can be brought to life in a cost-effective and timely manner. It serves as a stimulator of innovation in industry sectors often restrained by the capabilities of traditional manufacturing processes.
Kern concludes, "With its resilience to complexity and its ability to maintain consistency in costs and lead times, micrometal Group's PCE is revolutionising the production landscape. It is not simply an alternative method, it is the bridge to a future where the complexity of design is no longer a barrier but a welcome challenge. As industries continue to evolve and the demand for more sophisticated components rises, our unique PCE process will undoubtedly play a pivotal role in meeting those needs with unmatched precision and efficiency."
Working with the micrometal Group customers can access high volume ultra-precise reel-to-reel stainless steel PCE, enhanced traditional sheet based PCE for a wide variety of sheet thicknesses in a broad range of metals, and a number of allied and complementary technologies. This means the micrometal Group offers a globally unique range of PCE services for its customers, and is able to provide a truly scalable service with a focus on quality, process efficiency, and automation.
www.micrometal.de
Featured Product
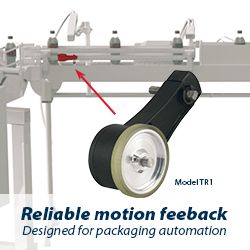