How to Select the Perfect PCB Coating Machine Line
Choosing the optimal equipment for your PCB coating line is pivotal for operational success. This guide navigates through the integral components of a standard PCB coating machine line and their efficacy in addressing common challenges. We delve into the composition of the line, encompassing the elevator, transfer station, coating machine, inspection station, curing oven, and the cohesive system facilitated by a return conveyor.
How to Select the Perfect PCB Coating Machine Line
Choosing the optimal equipment for your PCB coating line is pivotal for operational success. This guide navigates through the integral components of a standard PCB coating machine line and their efficacy in addressing common challenges. We delve into the composition of the line, encompassing the elevator, transfer station, coating machine, inspection station, curing oven, and the cohesive system facilitated by a return conveyor.
Components Of A PCB Coating Machine Line:
1. Elevator:
Initiating the PCB coating line, the elevator efficiently transports PCB boards to the subsequent processing stage.
2. Transfer Station:
Following the elevator, boards are directed to the transfer station, where they undergo preparation for coating.
3. Coating Machine:
At the core of the PCB coating line lies the coating machine, offering various models such as I.C.T-T550, I.C.T-T550U, I.C.T-T600, and I.C.T-T650.
4. Inspection Conveyor:
Post-coating, boards progress to the inspection station. Enhanced with LED lights and a blue glass cover, this station facilitates close scrutiny of coating quality, ensuring consistency and purity, free from dust contaminants.
5. Curing Oven:
For UV-curable adhesives, our UV curing oven effectively solidifies the adhesive, ensuring robust bonding.
6. Return Conveyor:
Underpinning the entire line is a return conveyor, seamlessly connected to the elevator. This system streamlines operations by automating the transportation of PCBs, minimizing manual handling.
Advantages Of The PCB Coating Line Design:
- Accessibility:
Strategically positioned beside the coating machine, the operator's station facilitates easy access for setup and adjustments.
- Efficiency:
Integration of the return conveyor optimizes workflow by eliminating the necessity for manual transport.
- Quality Control:
The inspection station equipped with a blue glass cover enables meticulous examination of coatings, ensuring high quality and cleanliness.
- Dust Prevention:
The blue glass cover serves as a protective barrier, preventing dust contamination on freshly coated PCBs.
Learn More:
Detailed Specifications:
Explore our article "Exploring Our PCB Coating Machine Models" for in-depth insights into our coating machines' specifications.
Coating Valve Selection:
Refer to our dedicated article "Selecting the Ideal Coating Valve" for guidance on choosing the appropriate coating valve for your adhesive.
Visual Understanding:
Watch our video demonstration to grasp a comprehensive overview of how the elevator, transfer stations, and return conveyor synergize.
Compliance With European Safety Standards:
Our PCB coating machine line complies rigorously with European safety standards, underscored by the CE certification. This certification guarantees adherence to the safety, health, and environmental protection requisites mandated by the European Union. Rest assured, our equipment aligns with international standards, ensuring safety and reliability in your operations.
Conclusion:
Selecting the right PCB coating machine line is pivotal for enhancing production efficiency and product quality. Our comprehensive solution, comprising elevators, transfer stations, coating machines, inspection stations, curing ovens, and return conveyors, is tailored to meet your needs. For further inquiries or personalized guidance, feel free to explore our related resources or reach out to the I.C.T team.
Featured Product
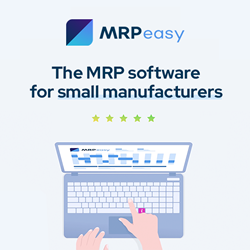
MRPeasy - ERP for Small Manufacturers That Delivers Results
Always know what you have in stock and what you'll need to fulfill orders. Never forget to order parts on time or fail to notice a late delivery from your vendor. Easily create manufacturing orders and schedule them automatically according to resource availability or delivery deadline. Generate accurate cost and lead time estimates and provide customers with quick quotes. Receive notifications when orders are late or inventory levels reach a critical point. Ensure seamless communication between sales, production, warehousing, procurement, administration, and finance. Integrate with popular accounting, CRM, and e-commerce apps. MRPeasy is an ERP software for small manufacturers that gives you all that and more. Our users report a 54% average improvement in the overall performance of their business and a 42% increase in on-time deliveries. Try for free, no credit card needed.