Replique Announces Public Launch of 3D Printing Material Hub
-
Mannheim, Germany, March 21, 2024 - Replique, provider of a decentralized 3D printing platform for the secure and reliable production of industrial-grade parts, announces the public launch of its comprehensive Material Hub for 3D printing. After a successful beta release that received overwhelmingly positive feedback, Replique is now excited to introduce the database to the broader community.
The Material Hub, openly accessible via www.replique.io/material-hub/ now contains an impressive collection of more than 400 polymer materials, compiled in collaboration with more than 25 material providers. This marks a substantial increase, more than doubling the number of materials available since its initial introduction Formnext in November 2023.
Already in the beta phase, the hub helped numerous companies, institutions, and partners to access and filter for the right 3D printing materials in seconds. Mathilde Lepilliez, Innovation Manager and 3D Printing Engineer at Alstom, shared her experience: "Replique's Material Hub significantly accelerates the material selection process. Just recently we have searched for a material that fulfills our high flame retardancy requirements as part of a new 3D printing project. Thanks to Replique's support we were able to find the right material fast and efficiently. This Material Hub will become a part of our daily-basis tools to help us to develop 3D printing."
Replique's Material Hub offers a multitude of benefits and features to engineers, purchasers and R&D. Users can easily navigate the hub thanks to technical filtering options to find the ideal materials for their specific applications, saving time and costs associated with manual research. Detailed technical specifications, industry standards, and application fields are provided for each material, ensuring informed decision-making. Additionally, printer manufacturers, service providers, and other stakeholders can benefit from the collective knowledge within the database, fostering collaboration and innovation within the 3D printing community.
With the public launch, Replique has incorporated performance improvements based on user feedback, including an optimized search function. This allows users to either search on a detailed level, e.g. direction-dependent mechanical properties, or on a more beginner-friendly level. Thus, also allowing less-experienced users to use the tool efficiently and get a head-start on their adoption of additive manufacturing. Once a suitable material is identified, users can now also directly request a quote to get their parts produced through Replique or reach out to the material provider to clarify further details.
Dr. Max Siebert, CEO, and Co-Founder of Replique, commented on the milestone: "We are thrilled with the positive reception of our Material Hub during the beta phase. The public launch marks an important step in our mission to democratize access to additive manufacturing. We are committed to continuously enhancing the platform to meet the evolving needs of our users."
Looking to the future, Replique is expanding the capabilities of the Material Hub with more features and materials. While the current focus is on polymers, adding metal materials is already planned. Thus, responding to the rising demand for metal 3D printing within multiple industry sectors. Material providers interested in showcasing their materials are encouraged to reach out to Replique directly.
To experience Replique's Material Hub firsthand, users can register to the database for free via www.replique.io/material-hub/. Moreover, they are welcome to visit Replique's booth at Hannover Messe in hall 2, stand E 38, where the database will be showcased alongside further features of Replique's on-demand 3D printing platform.
Featured Product
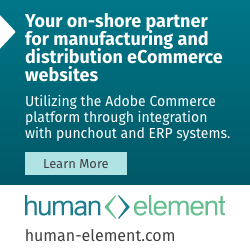
eCommerce For Manufacturers - How To Do It Right The First Time
With Human Element, you will build a strategic partnership with experienced on-shore strategists and developers who understand the pain points unique to manufacturers and distributors. Using Agile methodologies and proven eCommerce website development strategies, our team positions clients for success.