Aufeer Design relies on post processing equipment from AM Solutions
Innovative post processing ensures sustainable success
Since the beginning of 2023 the still relatively young 3D printing department at Aufeer Design in Mladá Boleslav has been utilizing a S1 and M1 Basic from AM Solutions - 3D post processing technology. With this equipment the Aufeer team achieves not only high-quality and consistent post processing results but, thanks to the automated operation, also saves a lot of time and money.
Aufeer Design, located in Prague, the capital of the Czech Republic, is part of the Aufeer group and, as midsize company, offers numerous technical solutions, especially for the automotive industry. In its innovation center the company develops models, mockups and prototypes for customers from all over the world and, in close cooperation with its engineers, develops practical designs and high-value products. Recently, the company established its own 3D printing department creating unique plastic components with the SLS print technology. Tomáš Klepl, manager of additive manufacturing at Aufeer Design, explains: „Our department is still very young, but we expect to grow rapidly. Because it opens completely new business opportunities for us, automated post processing is clearly a key to our success. We become faster, more cost-efficient and achieve high-quality, absolutely consistent post processing results. This creates confidence in additive manufacturing by our customers."
Easy communication
Since the beginning of 2023 Aufeer Design has been operating a S1 and M1 Basic system from AM Solutions - 3D post processing technology. Mr. Klepl continues: „We were impressed by the professional presentation of AM Solutions at the formnext exhibition, where the AM Solutions experts quickly understood what we were looking for. And, of course, with a nearby local partner communication was very easy. All our questions were quickly answered."
Shorter processing times and improved quality
Just a few weeks after the formnext exhibition the S1 and M1 Basic post processing systems were delivered and commissioned at Aufeer Design. Compared to other solutions available in the market, the multi-functional S1system performs the two process stages cleaning and surface finishing in one single machine. This space-saving concept provides not only room for one additional machine, but it also generates cost savings of up to 50 %. Moreover, the process stages cleaning and surface finishing can be performed with one single blast media. Therefore, no media changes are required and the risk of contamination - if two different media were to be used - has been completely eliminated.
The absolutely even and precise rotation of the work pieces in the S1 guarantees gentle processing and highly consistent finishing results. Thanks to the very efficient integrated recycling and cleaning system the polystyrol blast media has a low wear rate. This minimizes the amount of waste and results in a more sustainable process.
The M1 Basic, the cost-effective stand-alone post processing system, is used for surface smoothing and polishing of a variety of components. „While in the past our post processing operations had to be done manually, the S1 and M1 Basic do this work in a fraction of the time. Our colleagues have now a lot more time for more productive activities", concludes Mr. Klepl. „In addition, the surface finishing quality of our AM components is now substantially better. This allows us to offer our customers additional products and services." Based on the positive experience with the S1 and M1 Basic equipment, Aufeer Design plans to install additional post processing systems from AM Solutions.
For further information please click here: www.solutions-for-am.com
Featured Product
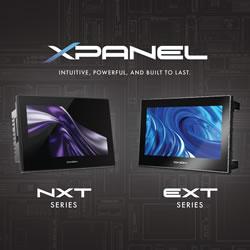
CIMON Xpanel eXT & nXT Series HMI
Introducing the Xpanel eXT and nXT series, advanced industrial HMI solutions that set a new standard for performance and usability. Utilizing our brand new Canvas HMI software for project creation, the Xpanel eXT and nXT series deliver a seamless and efficient user experience. They combine industrial-grade touch technology, powerful embedded OS hardware with a quad-core CPU, and an easy-to-use runtime platform. The Xpanel eXT and nXT series are specifically designed to optimize and streamline industrial operations, enhancing your HMI experience.