PTC secures industry first with Onshape Vision App for Apple Vision Pro
It works in sync with the Onshape cloud native CAD and PDM system on the iPad, enabling any changes in the product model to be updated in real time with the infinite canvas of Apple Vision Pro.
One of the UK's leading digital transformation experts has launched a new engineering app for the groundbreaking Apple Vision Pro.
The Onshape Vision App transforms flat computer screen models into virtual life-size products that team members can hold, pull apart and inspect as if they were physical components.
It works in sync with the Onshape cloud native CAD and PDM system on the iPad, enabling any changes in the product model to be updated in real time with the infinite canvas of Apple Vision Pro.
Backed by a long-term investment strategy in spatial computing technologies, PTC's new offering provides an enormous opportunity for industry to improve the way dispersed product development teams collaborate and conduct design reviews.
When brainstorming and sharing feedback with colleagues, participants from locations around the world can see realistic 3D images of their products in the same virtual meeting space, making interacting with technology more natural than ever.
"We are the first CAD and PLM company to launch a dedicated app for Apple Vision Pro and this move extends our commitment to the Apple community," explained David Katzman, General Manager Onshape at PTC.
"When viewing your product designs through this new technology, there are no limits to your workspace. You can tinker with your CAD model floating on an infinite canvas in front of you or move it around the room to anywhere you like."
He continued: "You can walk on the factory floor and see your new industrial machinery at full scale before committing to production or shrink it to fit on a tabletop to get a better grasp of the overall design.
"Viewing your product model at different scales can encourage new perspectives and help identify potential improvements. It's a much different experience than zooming in or out on a part on a flat screen. You can grab the CAD model with your hands, bring it closer to your face, and let your curiosity lead the way, delivering a more streamlined and performance rich solution in the process."
PTC believes that the earlier a hardware development team gets feedback on a design concept, the more likely they will be able to deliver products that their customers truly need and want.
Expanding the pool of stakeholders as soon as you can in the review process also leads to more design iterations and exploration.
Another advantage of completing design reviews with Onshape Vision is that it is extremely welcoming and intuitive for non-CAD users such as executives, sales and marketing professionals and customers.
David went on to add: "It's worth a reminder that most people in your business circles are not familiar or comfortable navigating CAD software. While wearing the Apple Vision Pro, it is easy for them to reach out and grab a digital part or assembly and point out their areas of interest.
"The Onshape Vision app makes it much easier for customers and suppliers to customise product options and configurations. Sales teams can now share purchase options in a more dynamic presentation, and get more timely feedback, ensuring better customer satisfaction."
PTC has been committed to advancing spatial computing and associated technologies for the manufacturing industry, primarily through the innovative work of its Vuforia software team and its dedicated Reality Lab.
For further information, please visit www.ptc.com or follow @ptc on twitter
Featured Product
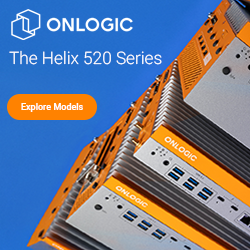
OnLogic's Helix 520 Series of Scalable Fanless Computers
The Helix 520 series utilizes the latest Intel Core Ultra processors with integrated edge AI capabilities to deliver exceptional performance and industrial-grade reliability for demanding applications in automation, robotics, machine vision, and more. Its unique modular design allows for flexible scaling of CPU and GPU performance, while robust connectivity and expansion options ensure seamless integration.