Eplus3D and Paradigm 3D Forge a Transformative Partnership in Metal Additive Manufacturing
This partnership positions Paradigm 3D, a new entrant in the digital manufacturing realm, as a catalyst for global innovation, offering a platform for industries to explore new concepts and drive value-added product innovation.
Recently, Eplus3D announced the installation of the top-notch MPBF machine EP-M300 at Paradigm 3D, marking a significant step in generalizing 3D printing into a competitive manufacturing process, particularly in the production of certified aerospace components. This partnership positions Paradigm 3D, a new entrant in the digital manufacturing realm, as a catalyst for global innovation, offering a platform for industries to explore new concepts and drive value-added product innovation.
Paradigm 3D, in pursuing for cutting-edge capabilities, outlined specific requirements for a 3D printer. EP-M300 from Eplus3D ideally aligns with with these needs, it provides a substantial build volume of 300 × 300 × 450 mm, enabling the brilliant printing of medium and large and complex parts. Additionally, its advanced Metal Powder Bed Fusion (MPBF) technology and precise powder feeding guarantee high material utilization, effectively minimizing waste and reducing overall costs. EP-M300 is engineered to meet the rigorous quality and reliability standards required for aerospace component production, making it a compelling solution for this sector. Furthermore, the multi-laser feature of EP-M300 allows for superior speed and efficiency, ensuring reliable and highly productive printing with a variety of metal powders, thus shortening the manufacturing process hours.
Feedback from Paradigm 3D emphasizes the transformative impact of EP-M300:
1. Research and Development: The open platform and high material utilization rate enable experimentation with various materials and parameters, supporting advanced research and development initiatives .
2. Production of high-precision parts: The advanced laser technology of EP-M300 ensures consistent accuracy and quality, making it ideal for production applications.
Paradigm 3D expressed their commitment to the partnership by stating, "Together, we can make a significant impact in the field of digital manufacturing industry and foster a culture where modern industries recognize and utilize the potential of metal additive manufacturing." The partnership between Eplus3D and Paradigm 3D is expected to bring good prospects, leveraging Eplus3D's expertise in metal additive manufacturing and Paradigm 3D's innovative solutions to drive advances in the aerospace industry and promote the adoption of metal additive manufacturing on a global scale.
About Paradigm 3D
Paradigm 3D is the first digital manufacturing facility in the Middle East capable of producing certified aerospace components. In the ever-evolving landscape of technological innovation, Paradigm 3D emerges as a beacon of progress, passionately committed to advancing two of the world's most critical sectors: aviation and oil & gas.
About Eplus3D
Since founding the first SLS machine in China in 1993, Eplus3D has more than 30 years of AM technology experience and is engaged in research and development of industrial-grade Additive Manufacturing systems and application technologies with MPBF™ (Metal Powder Bed Fusion) and PPBF™ (Polymer Powder Bed Fusion) 3D printing technology.
Eplus3D has four facilities in Beijing, Hangzhou, Stuttgart and Houston, with an annual scientific research investment of more than 20% of the revenue with comprehensive invention patents, utility model patents, software copyrights as well as appearance patents. It has made remarkable achievements in the design, process, software, materials and post-processing development for additive manufacturing.
Featured Product
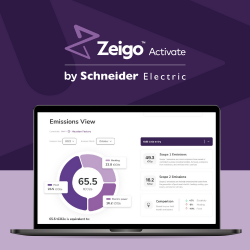