Ultimation Industries Shares Five Industry Trends Shaping Material Handling in 2024
Economy and labor shortages are among the factors driving the need for more productivity and efficiency
Economic conditions and other factors are driving manufacturers and distributors to look for creative ways to gain more efficiency and productivity from their material handling operations, according to Ultimation Industries.
"Warehouses and distribution centers are evolving based on the changing demands faced by modern supply chains," said Kali Wahrman, general manager for Ultimation. "In 2024, we expect the growth of e-commerce and continuing economic uncertainty to influence the way manufacturers and distributors address productivity challenges in their facilities."
"Warehouses and distribution centers are evolving based on the changing demands faced by modern supply chains."
Ultimation, an MCE company, is the leading direct-to-consumer conveyor manufacturer, specializing in solving productivity challenges with fast-to-deploy solutions for a broad range of end-markets, including energy, automotive, logistics and vertical farming.
Based on interactions with customers, Ultimation has identified these five industry trends that it believes will shape material handling decision-making for warehouses and distributors in 2024:
Rising cost of square footage. The price of goods and services is rising, but so is the cost of commercial construction. Simply adding onto a manufacturing facility or distribution warehouse to meet growing demand is out of reach for many small and medium-sized businesses. That's why many are looking to maximize the space they have through conveyors and other material handling systems that make the most of small footprints or utilize otherwise unused vertical space. Lifters and overhead conveyor systems are an affordable, effective solution that can be deployed relatively quickly, moving totes, cartons and pallets from one level to another with carriers designed to handle multiple load weights and sizes.
Worker shortage. Manufacturers and distributors are increasingly turning to automated systems and robotics to meet production schedules in the face of worker shortages. While some are making longer-term capital investments in new technologies, others are adopting flexible solutions that can be deployed quickly without reconfiguring production lines or factory footprints. One example is Autonomous Mobile Robots (AMR) or warehouse robots that move materials within a facility. Unlike automated guided vehicle (AGV) or cart (AGC) systems which require a path or track to navigate or use wires or lasers, warehouse robots use integrated sensors to read their environment. Companies are also looking for more "smart" systems such as barcoding technologies that integrate with their existing Enterprise Resource Planning (ERP) and inventory systems to streamline processes and gain efficiencies.
Growth of e-commerce. A few short years ago, shopping for conveyors or other material handling equipment online was unthinkable, according to Wahrman. Today, the same companies that are trying to keep up with the pace of e-commerce are using it themselves to outfit their facilities with conveyors and other material handling solutions that can be deployed quickly and inexpensively. Supply chain procurement managers can now compare costs and shop for a growing variety of warehouse and distribution center products and parts with the click of a button.
Faster delivery times. It's not just consumers who want it now. Today's supply chains are scaling fast and there's rarely time to wait for expensive, custom-designed systems. Lead times for many material handling solutions have improved since 2020, but are not yet back to pre-pandemic levels, according to Wahrman. She adds that off-the-shelf, quick-ship conveyor solutions that can be configured almost overnight for their specific requirements are helping supply chains keep pace.
Energy-efficiency. Reducing energy consumption is gaining a greater sense of urgency as overall operating costs continue to rise. Replacing legacy conveyor systems with alternatives that only use electricity when they are actively moving cargo can be an important part of an overall energy-efficiency strategy. Conveyors equipped with motorized driven roller (MDR) systems, for example, operate with 24-volt DC power and run on demand. Wahrman estimates that replacing a typical 5-foot Chain Driven Live Roller conveyor system using approximately 0.75kWh of energy for operation could save up to 81% in energy usage by replacing it with a same-size MDR system.
Today's conveyor systems offer so many innovations that increase material handling efficiency that it's worth the time to rethink your current systems. Visit the Ultimation website at https://www.ultimationinc.com/ for more information.
About Ultimation, an MCE company
Ultimation Industries, LLC is the leading direct-to-consumer conveyor manufacturer serving the automotive, food processing, vertical farming, heavy equipment, warehousing, fulfillment and delivery industries. The company offers a line of proprietary automation systems and is also the largest integrator of Jervis Webb Conveyor Systems. Ultimation's e-commerce channel sells Ultimation, Interroll, Itoh Denki, Jervis Webb, and a wide range of other conveyor equipment. Ultimation became part of the Motion & Control Enterprises (MCE) family of companies in August 2023. Visit https://www.ultimationinc.com/ for the latest product information and news about Ultimation.
Featured Product
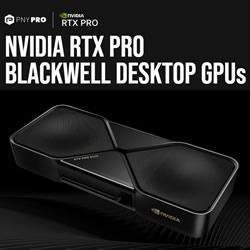
NVIDIA RTX PRO™ BLACKWELL DESKTOP GPUs N
NVIDIA RTX PRO™ - Built for Professionals - NVIDIA RTX PRO Blackwell Desktop GPUs feature the latest breakthroughs in AI, ray tracing, and neural rendering technology to power the most innovative workflows in design, engineering, and beyond.