Kane Robotics Launches Sanding, Grinding, Finishing Cobot to Fill Job Vacancies and Improve Productivity in Manufacturing
Kane Robotics launched its collaborative robot solution, GRIT, that dramatically improves productivity, reduces health risks and solves labor shortage issues on manufacturing shop floors. The first cobot solution innovated specifically to solve challenges in composites sanding and weld grinding, Kane's GRIT cobot works alongside humans to perform sanding, grinding, polishing, deburring and other labor-intensive material removal for any size manufacturer in a variety of industries.
Austin, Tex., March 2023 - Kane Robotics launched a collaborative robot (cobot) solution that dramatically improves productivity, reduces health risks and solves labor shortage issues on manufacturing shop floors.
The first cobot solution innovated specifically to solve challenges in composites sanding and weld grinding, Kane's GRIT cobot works alongside humans to perform sanding, grinding, polishing, deburring and other labor-intensive material removal for any size manufacturer in a variety of industries.
The GRIT has helped composites manufacturers complete jobs such as:
● sanding primer from machine components
● removing coating and sanding surfaces for paint
preparation or repairs on helicopter main rotor blades
● polishing fighter jet canopies after thermoforming to remove orange peel and achieve optical clarity
● deburring and weld grinding metal castings and other parts
Manufacturers in aerospace and other industries have seen impressive results from employing GRIT in their operations:
● Exponentially increased productivity. A 12-hour sanding job can turn into 3.5 hours when done by a GRIT cobot. Moreover, cobot sanding is precise and uniform, minimizing the need for further detail work before starting second-phase operations.
● Reduced health risks. Kane's GRIT cobot reduces repetitive injuries to wrists, elbows and shoulders as well as respiratory and ocular illness caused by airborne particles. In short, cobots help manufacturers keep their people — and keep them healthy. And, companies report significant savings in health care costs.
● Filling job vacancies. U.S. manufacturers are having difficulty attracting new workers, especially for taxing work like sanding. GRIT cobots can help fill those roles, plus lessen the need to replace retiring workers as the manufacturing workforce ages. A GRIT cobot can free veteran workers to do what they do best - operations that require higher-order reasoning and decision-making.
Unlike traditional industrial automation, GRIT solutions are reconfigurable for different tasks and, with three sizes, the cobots can accommodate a wide variety of jobs. They are accessible even for smaller manufacturers; a GRIT system requires an average investment of just $100,000, with 100% return on investment after as little as six months.
GRIT solutions are designed for ease of use and require no specialized expertise to install, operate or program. The practical system is compact and mobile and plugs into 110V electrical outlets. It can be operated by almost any manufacturing technician and be up and running in almost any manufacturing facility within hours or days rather than months or years. Because GRIT solutions are quick to set up and operationalize, they realize near-immediate ROI.
"Manufacturers require extremely precise sanding, grinding, polishing and finishing work to ensure parts meet regulatory requirements and achieve top performance. Kane Robotics' GRIT cobot solutions provide the highest quality work, plus save teams from injuries and illness by filling those repetitive, labor-intensive jobs that humans don't want to do," says Kane CEO John Spruce.
"With GRIT, manufacturing teams can simultaneously improve their productivity and solve safety and labor shortage challenges."
Contact Kane for more information at https://kanerobotics.com/contact/.
Featured Product
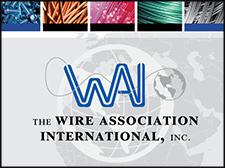