EOS and AM Solutions announce partnership
EOS, one of the world's leading technology providers for industrial 3D printing, and AM Solutions - 3D post processing technology, one of the world's leading experts for industrial post-processing solutions, have recently combined their expertise and officially announced their partnership.
EOS, one of the world's leading technology providers for industrial 3D printing, and AM Solutions - 3D post processing technology, one of the world's leading experts for industrial post-processing solutions, have recently combined their expertise and officially announced their partnership. Both companies are united by the goal of optimizing the process chain in the field of 3D printing and thus further paving the way to series production.
EOS and AM Solutions - 3D post processing technology, two leading companies known for innovation and expertise in their respective fields, have joined forces to focus on advancing the entire additive manufacturing process chain. In order to make the leap to mass production, the individual steps leading to the finished product must become increasingly automated and significantly more economical. There is a lot of potential in the interfaces. "In order to truly scale AM production, all steps within the value chain - including post-processing - must work in concert, providing a complete solution for our customers. With AM Solutions, we have found a partner with the capabilities to reach the next level in automating the AM process chain", says Virginia Palacios, Chief Business Officer Polymer at EOS. "We share the same goal and enrich each other with our different competencies and decades of experience on both sides".
"Our companies are united by the same high quality standards, the pursuit of the best customer solution in each case, and the goal of establishing 3D printing as a whole economically, efficiently, and at the highest level of quality", adds David Soldan, Head of AM Solutions - 3D post processing technology. In addition, both companies are owner-managed, develop and produce their machines in Germany and embody the values of successful, medium-sized German companies. "Our technology's ability to provide quality and reliability while performing at peak production levels is why we are the market leader and why we chose AM Solutions as our partner", says Virginia Palacios.
Scalable solutions without compromises
Above all, EOS and AM Solutions are working to take SLS printing to the next level on an industrial scale. The higher the output, the more reliable, faster and more efficient the subsequent steps, such as depowdering, have to be. The key to this lies in automated, economical and highly efficient post-processing. In this way, quantities can be scaled up as required - without compromising quality and reproducibility. Increased automation is also an important factor in addressing the growing shortage of skilled labor.
Sustainability and occupational safety are also key considerations. "Our depowdering solutions are always designed to recycle as much material as possible. This saves valuable resources and, ultimately, money," explains David Soldan. As part of its Responsible Manufacturing mission, EOS places great emphasis on sustainability. The fully automated finishing processes also replace manual processing, ensuring greater safety and a much better working environment for employees by significantly reducing the operator's direct contact with the powder.
Featured Product
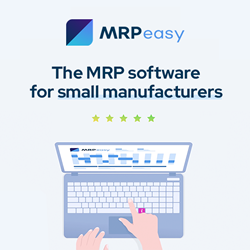