Markforged Introduces FX10, The Most Versatile Tool Designed For The Factory Floor
The fifth-generation print system features built-in automation for quality assurance and print routines designed to deliver strong, accurate parts every print
Markforged Holding Corporation (NYSE: MKFG), the company strengthening manufacturing resiliency by enabling industrial production at the point of need, today unveiled its newest industrial 3D printer, the FX10. Continuing Markforged's heritage of reliable printers that deliver strong, precise parts, the FX10 is designed to supercharge manufacturing line productivity and profitability. The FX10 empowers users to print the right part when and where it is needed, reducing costs and cutting lead times from months to days compared to traditional manufacturing methods.
"We engineered the FX10 to be the best tool for the manufacturing floor," said Shai Terem, CEO of Markforged. "The FX10 allows manufacturers to slash original part replacement costs when compared to traditional methods and keep production lines running without worrying about supply chain issues or spare parts inventory. The FX10 can accelerate the digitization of the manufacturing floor by increasing the adoption of digital inventory to build supply chain resiliency. Our customers now have the potential to save even more capital by reducing physical inventory and boosting production yields while decreasing operating costs."
Designed with flexibility in mind, the printer's modular systems are engineered to be expanded and upgraded with additional capabilities. For example, the FX10 has been designed to incorporate a printhead integrated vision module to capture detailed part images and data to further ensure part quality and optimize printer performance. The 5th Generation Continuous Fiber Reinforcement (CFR) print system delivers high print quality in a heated print chamber allowing for print speeds that are nearly twice as fast and print sizes that are up to twice as large as previous Markforged industrial series printers, enabling the replacement of metal parts with advanced composites.
"The FX10 is another important milestone in our mission to bring industrial production to the point of need. It enables our customers to address even more industrial applications with clear return on investment. Coupled with our Digital Source platform, we are truly starting to bring the vision of distributed manufacturing into reality," said Terem. "The FX10 features a full suite of automation built to simplify the usage of the printer and increase adoption to build resiliency into our customers' production. When a line is down, or a tool is needed, FX10 users can simply Press Print."
The FX10 was designed to ensure easy adoption on the manufacturing floor starting with the first line operator. A simple touchscreen interface combined with new automation and quality assurance technologies enable users to get more parts out of the FX10 with fewer interactions needed by the operator before and during a print than with previous Markforged printers.
The printhead-mounted optical sensors automatically verify the dimensional accuracy of parts during the print to ensure consistency and reliability, while also assessing machine health and performance. The laser micrometer in the FX10 scans parts during printing and assists with the machine's automatic calibration. Inspection software interprets the data from the sensors for dimensional verification, providing users with quality assurance as soon as a print finishes.
The material drawer of the FX10 contains built-in, individually sealed storage bays for up to four 800cc spools. FX10 is able to automatically execute spool changeovers between filament storage bays during a print, and users can reload empty spool bays without disrupting a print.
The Digital Forge is the additive manufacturing platform for modern manufacturers that enables every aspect of the FX10. A complete additive manufacturing platform consisting of printers, cloud-enabled software with process improvement tools and a wide range of industrial materials, The Digital Forge is purpose-built to integrate into existing manufacturing ecosystems. With the Digital Forge, users can share parts across their organization, and monitor fleet performance from a central location.
About Markforged
Markforged (NYSE:MKFG) is enabling more resilient and flexible supply chains by bringing industrial 3D printing right to the factory floor. Our additive manufacturing platform The Digital Forge allows manufacturers to create strong, accurate parts in both metal and advanced composites. With over 10,000 customers in 70+ countries, we're bringing on-demand industrial production to the point of need. We are headquartered in Waltham, Mass where we design the hardware, software and advanced materials that makes The Digital Forge reliable and easy to use. To learn more, visit www.markforged.com.
Featured Product
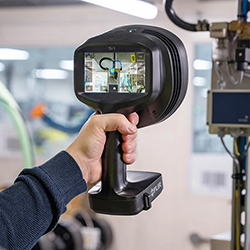