voxeljet Showcases Its Next-Gen 3D Printers VJET X in Action at BMW Group: With 10x Faster Performance, the New 3D Printers Are Integrated Into a Fully Automated Additive Production Line
voxeljet's 3D printers significantly reduce emissions in the additive manufacturing process of metal parts and make new designs possible
voxeljet AG (NASDAQ: VJET) and Loramendi demonstrate the world's first fully automated additive serial 3D production line for sand cores, jointly developed as part of the Industrialization of Core Printing (ICP) cooperation project. A new video released today features the implementation of the first ICP production line at BMW Group's plant in Landshut, Germany. As BMW Group's largest component plant, Landshut has approximately 3,500 employees and supplies all of its vehicle and engine plants worldwide, including for nearly all BMW, MINI and Rolls-Royce vehicles, and for its motorcycle brand, BMW Motorrad.
The customized, low-emissions solution integrates voxeljet's high-speed VX1300-X (VJET-X) 3D printers into a fully automated pre- and post-processing workflow, including industrial microwaves for curing the 3D printed cores. Printing rates were increased by factor ten with the latest generation of VJET-X 3D printers, and the toolless design of the sand cores allowed for variant changes at unprecedented speed without time-consuming tool changes and production downtime. The unused material is 100% recycled and reused in the production process.
"The fully-automated 3D production line at BMW's Landshut plant is a key milestone not only for voxeljet, but for the entire 3D printing and automotive industry," said Dr. Ingo Ederer, founder and CEO of voxeljet. "We believe this customized, near-zero emissions solution achieved in partnership between voxeljet, Loramendi and BMW will become an industry standard."
Together, voxeljet and Loramendi are revolutionizing the industrialization of core printing. The production of inorganic 3D printed cores has enabled BMW Group to advance the design of its engine components. For example, the cylinder head for BMW's B48 engine has been significantly improved by using 3D printing to produce water jacket - outlet combi cores. Additionally, 3D printing allows BMW to produce sand cores in one piece, reducing the complex design of engine components while optimizing the engine's efficiency and fuel consumption. The inorganic 3D production line also significantly reduces the foundry's emissions, as only water steam is produced during the casting process.
voxeljet's powerful next-generation binder jetting 3D printing technology offers the highest additive productivity and throughput to meet the demands of BMW's large-scale production needs. voxeljet's layer-by-layer technology works by using sand and an inorganic binder. A print head selectively bonds layers of sand to create the cores, which are then unpacked, microwave cured, cleaned and inspected before being fed into BMW's established casting process. voxeljet has obtained one patent and has ten patent families with 28 patent applications that protect this proprietary approach across the United States, Europe, and other geographies.
About voxeljet
voxeljet's (NASDAQ: VJET) roots reach back to the year 1995 with the first successful dosing of UV-resins. In the context of a "hidden" project, initial 3D-printing tests are performed at the Technical University Munich. Our company was founded on May 5, 1999 as a spin-off from TUM in Munich with a clear vision in mind: to establish a new manufacturing standard by developing new generative processes for the series-production of complex components using 3D printing. In the beginning, operations are launched with four employees at the TUM. Today, we are a globally acting, leading provider of high-speed, large-format 3D printers and on-demand 3D printed parts to industrial and commercial customers. Components manufactured with the help of our technology are flying in space, make mobility more efficient and the production of new engineering solutions possible. Visit our website www.voxeljet.com, and follow us on Linkedin, or on Twitter.
Featured Product
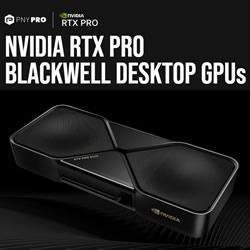