Maximizing Efficiency with Predictive Maintenance for Vacuum Pumps
Learn how predictive maintenance enhances vacuum pump performance and saves costs.
In today's rapidly evolving industrial landscape, the efficiency and reliability of equipment play a pivotal role in ensuring seamless operations. Among the critical components of various industries, vacuum pumps stand out as indispensable workhorses. From manufacturing to healthcare, vacuum pumps are used to perform a wide array of tasks. To optimize their performance and reduce operational costs, predictive maintenance has emerged as a game-changer. In this article, we'll delve into the world of predictive maintenance for vacuum pumps, exploring how this proactive approach can revolutionize your operations.
Enhancing Performance Through Proactivity:
Vacuum pumps, like any other machinery, are subject to wear and tear over time. Unplanned breakdowns can result in downtime, loss of production, and increased repair costs. Predictive maintenance leverages advanced technologies such as IoT sensors, data analytics, and machine learning algorithms to monitor the health of vacuum pumps in real time. By continuously collecting and analyzing data, this approach can predict potential issues before they escalate into major problems. This allows maintenance teams to intervene at the right time, preventing unexpected downtime and ensuring optimal performance.
Cost Savings at Your Fingertips:
One of the most significant benefits of predictive maintenance for vacuum pumps is its potential for cost savings. Traditional maintenance approaches often involve scheduled check-ups and replacements, which might lead to unnecessary part replacements and downtime. With predictive maintenance, maintenance activities are performed based on the actual condition of the equipment. This means you replace components when they truly need it, reducing the costs associated with premature replacements.
Seamless Implementation:
Implementing predictive maintenance for vacuum pumps is more accessible than ever. IoT-enabled sensors can be retrofitted onto existing equipment to start collecting data immediately. This data is then transmitted to a central system for analysis. Machine learning algorithms identify patterns and anomalies, providing actionable insights to maintenance teams. This proactive approach allows you to schedule maintenance activities during planned downtime, minimizing disruptions to your operations.
Conclusion:
In the age of industrial advancement, predictive maintenance has emerged as a beacon of efficiency and cost-effectiveness. Vacuum pumps, as integral components of numerous industries, can greatly benefit from this proactive approach. By embracing predictive maintenance, you not only enhance the performance of your vacuum pumps but also optimize your operations by reducing costs and downtime. Stay ahead of the curve - harness the power of predictive maintenance for vacuum pumps and propel your business into a future of seamless productivity.
Featured Product
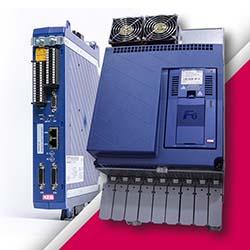