Application story: UltraFlex's Time-Efficient Induction Brazing for Stainless Steel Tubes
This application story proved that UltraFlex's advanced induction heaters are an ideal solution for time-efficient induction brazing of stainless steel assembly, ensuring precision, uniformity, and environmental safety.
The time-efficient induction brazing process for a stainless steel assembly made of low-carbon tubing and fittings has been demonstrated by UltraFlex Power Technologies. UltraFlex is a leading manufacturer of digitally controlled, advanced induction heaters and is frequently setting up demo applications for potential customers looking to evaluate the usage of induction heating for their manufacturing processes.
In this customer scenario, a manufacturer from the automotive industry was looking to replace their existing induction heating equipment with UltraFlex one and needed to evaluate the heating parameters for a major induction brazing process. The parts to be brazed in the process were a tube with 0.78" (1.98 cm) outside diameter and 0.07" (0.18 cm) wall and fitting with 0.78" (1.98 cm) internal diameter.
UltraFlex engineers recommended the usage of an induction heater from the UltraFlex SOLO series as most appropriate for this customer heating scenario. The UltraFlex SOLO Systems are a breakthrough innovation in induction heating technology, featuring a unique Direct Digital Step™ control algorithm.
To ensure optimal results in this customer scenario, UltraFlex tested the performance of two types of induction coils - a helical induction coil with 2 turns and a C-shape induction coil with 3 turns. At power supply of 5 kW, using the helical coil, it took 13 seconds to reach the brazing temperature and complete the brazing process. At power of 13 kW and using a C-shape induction coil, the heating cycle time achieved was the same.
The test application performed by UltraFlex confirmed the high energy efficiency of UltraFlex induction brazing for the specific customer case and helped identify the most efficient induction heating setup. In addition, the digital control of the UltraFlex induction heating solutions ensures precision and uniformity of the brazing results, with no risk for errors or dependency on the operator skills. Going for an UltraFlex induction heater also ensures an environmentally safe and clean process, thanks to the lack of open flame and noxious emissions.
In summary, UltraFlex's advanced induction heaters are an ideal solution for time-efficient induction brazing of stainless steel assembly, ensuring precision, uniformity, and environmental safety. Contact UltraFlex today to learn more about their breakthrough innovation in induction heating technology.
Find out more at:
https://ultraflexpower.com/
Contact us at:
+1.631.467.6814
uptnews@ultraflexpower.com
About UltraFlex Power Technologies:
UltraFlex Power Technologies (ultraflexpower.com) offers the most advanced and innovative digitally controlled induction heating equipment in the industry. Its compact modular and flexible systems are used for a wide variety of induction heating, casting and melting applications.
Featured Product
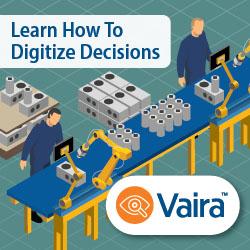