Greene Tweed Highlights Product Portfolio for the Hydrogen Market at the 2023 Hydrogen & Fuel Cell Seminar
Visit Booth 115 To See High-Performance Products That Address Key Challenges of Hydrogen Applications
Lansdale, PA - Greene Tweed, a leading global manufacturer of high-performance sealing
Greene Tweed's wide-ranging portfolio of elastomer, thermoplastic, and thermoplastic composite materials/products are capable of operating in the most chemically aggressive media. With a focus on addressing the major pain points in the hydrogen market, Greene Tweed has successfully developed a complete portfolio of solutions to enable valves, compressors, electrolysers, fuel cells, and other equipment ready to handle hydrogen's key technical challenges, such as high permeation and low lubricity.
Greene Tweed will showcase its Fusion® 938 o-rings, made from high-performance FKM material offering exceptional resistance to hydrogen exposure. It will also feature Fusion®665 o-rings, made of ultra-low-temperature and chemical-resistant FKM elastomer. Also on display will be MSE® range of metal spring energized lip seals, built to withstand extreme temperatures, high pressure, and corrosive chemicals. Visitors can also see compressor piston rings, rider bands and valve plates made of our cross-linked PEEK Arlon 3000XT®, PFA composite WR®600, and modified PTFE Avalon®56.
In addition, Kerry Drake, Ph.D., the R&D Technology Manager at Greene Tweed will present a paper ‘‘Materials Engineering for Hydrogen Service: Arlon 3000XT® Crosslinked PEEK Properties and Performance' at the Technical Track Sessions of the Seminar. He will outline that better electrical, chemical, and mechanical properties of the patented Arlon 3000XT® can improve the performance of fuel cell and electrolyser applications. The presentation is part of the Second Session on Material Advances, Room 101-B, scheduled to start at 3:45 pm, Thursday, February 9th.
Greene Tweed products for the hydrogen market are designed to handle technical challenges like sealing issues, Rapid Gas Decompression resistance, low temperatures and fugitive emissions, metal embrittlement, constant wear/friction, and the risk of gas contamination.
Featured Product
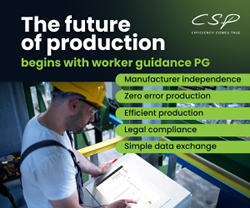
Quality assurance in the manufacturing industry
Efficiency and precision with CSP software. In the highly competitive world of manufacturing, quality assurance is a critical factor for success. CSP offers you state-of-the-art software solutions specifically designed to ensure the highest standards of quality assurance in the manufacturing industry.