New Emerson Valves Deliver Proportional Flow Control Performance in Exacting Applications
ASCO Series 209 proportional valves offer superior precision, flow and power consumption for medical devices, hydrogen fuel pumps, food equipment and more
Emerson today introduced the ASCO™ Series 209 proportional flow control valves, which offer the highest standards of precision, pressure ratings, flow characteristics and energy efficiency available in a purpose-built, compact architecture. With this combination of size and performance, Series 209 valves allow users to precisely regulate the flow of fluid in a wide range of devices that require exacting performance, like those found in the medical equipment, food and beverage, and heating, ventilation and air conditioning (HVAC) industries.
Accuracy, response time and repeatability are critical in high-precision flow control applications, such as controlling tool speed in dental chairs, the flow of steam in coffee makers, water flow in cooling systems and hydrogen flow in fuel cells. Series 209 valves have low hysteresis (less than or equal to 5%), excellent repeatability (less than or equal to 1%) and high sensitivity (less than or equal to 0.2%) that contribute to their precision.
"Proportional valves are key components that can significantly impact equipment performance and efficiency," said Shivam Chauhan, commercial product marketing manager, Europe, the Middle East and Africa at Emerson's discrete automation business. "We designed the ASCO Series 209 valves to deliver the highest level of performance in a small footprint, giving our customers the flexibility and confidence to engineer products that drive innovation, foster sustainability, lower costs and improve people's lives."
The low power consumption and fast response time (less than or equal to 15 milliseconds) of Series 209 can extend battery life in devices powered by them and optimize system performance and efficiency. An improved internal design prevents metal-on-metal contact that causes clicking, which allows valves to operate at extremely low sound levels that are crucial for occupant comfort and well-being in medical, commercial building and food service and hospitality environments.
Series 209 valves meet global approvals, including Underwriters' Laboratories (UL), United Kingdom Conformity Assessed (UKCA) and European Conformity (CE) and include a range of options that tailor valves for specific applications. For instance, Series 209 valves can be cleaned for critical applications like oxygen therapy devices and come in different coil configurations that add flexibility and simplify installation. And a selection of elastomers ensures compatibility with various media, including elastomers free of silicone that can withstand alcohol and sulfur in demanding applications like painting and powder coating as well as elastomers approved by the United States Food and Drug Association (FDA) for food and beverage applications.
Series 209 valves join Emerson's comprehensive offering of industry-leading proportional valve technology. For more about Emerson's ASCO Series 209 proportional flow control valves, please visit www.Emerson.com/Proportional.
https://www.emerson.com/en-us/news/automation/22-12-new-asco-series-209-proportional-flow-control-valves
Featured Product
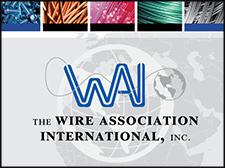