Desktop Metal Introduces All-New Digital Sheet Metal Forming Technology with Figur G15 at IMTS 2022
The Figur G15 uses patent-pending Digital Sheet Forming (DSF) technology in which a software-driven ceramic toolhead on a gantry shapes standard sheet metal into parts with up to 2,000 lbs of force
Desktop Metal, Inc. (NYSE: DM), a global leader in additive manufacturing technologies for mass production, today announced the launch of the Figur G15, the first commercial platform of its kind to shape standard sheet metal on demand directly from a digital design file using all-new, patent-pending Digital Sheet Forming (DSF) technology — no stamping tools, molds, dies, or presses required.
While digital cutting tools are commonly used today and have delivered many benefits to the $300 billion sheet metal forming and fabrication industry, no turnkey digital sheet forming solutions have been widely commercialized. Nearly all solutions for rapid production of sheet metal parts require custom forming tools, molds, or dies, which typically have long lead times and are expensive to produce.
Figur's breakthrough DSF technology maintains high precision with a flexible, incremental forming approach through a proprietary build box design that reduces force distribution across the sheet during the build. This unique solution eliminates high startup costs and long-lead time associated with custom tools, molds, and dies to unlock the benefits of digitization for sheet metal manufacturers, improving their business agility and making sheet metal forming accessible to new applications across a range of volumes.
"After years of development, we're excited to show our Digital Sheet Forming technology to sheet metal fabricators," said Ric Fulop, Founder and CEO of Desktop Metal. "Sheet metal forming with the Figur G15 is accessible, flexible, and cost-effective, even at low volumes. Manufacturers in the automotive, aerospace, appliance and other industries can now produce a fully formed part in less than an hour without a major investment of time or money."
The Figur G15 features a software-driven ceramic toolhead on an XY gantry that progressively forms large metal sheets layer by layer with up to 2,000 lbs of force. With a forming area of 1450 x 1000 mm (57 x 39 in) in X and Y, the Figur G15 can process positive and negative forms up to 400 mm (16 in) in the vertical Z direction. A wide variety of metals and sheet thicknesses can also be processed - including steel up to 2.0 mm thick and aluminum up to 2.5 mm.
A video showing the production of parts on the Figur G15 can be viewed at figur.desktopmetal.com, where manufacturers can also reserve a system.
Additive Manufacturing 2.0 Live at IMTS 2022
Desktop Metal will showcase its breakthrough portfolio of Additive Manufacturing 2.0 technologies — including more than 350 metal, polymer, sand, and wood 3D printed parts — in two booths on Level 3 of the West Building at the International Manufacturing Technology Show.
IMTS, which will take place Sept. 12-17 at McCormick Place in Chicago, is the largest and longest-running industry trade show in the Western Hemisphere.
Among the technology to be on display at the show:
● The Figur G15, will demonstrate its all-new Digital Sheet Forming (DSF) technology for steel, aluminum and more. Live demonstrations to be held two times a day at 10 a.m. and 3 p.m. Booth 432212.
● The Shop System™, now the world's best-selling metal binder jetting system with new configurations for power users, including the Shop System+ and the Shop System Pro. Desktop Metal Booth 433103, and SolidCAM Booth 134502 in the East Building.
● The Production System™ P-1, an industrial manufacturing platform powered by Desktop Metal's Single Pass Jetting™ technology. Booth 433103.
● The Studio System™, an office-friendly, two-step Bound Metal Deposition (BMD) printer, now featuring an industry-leading eight metal materials. SolidCAM Booth 134502.
● The S-Max® Flex, a robotic AM 2.0 system, makes sand 3D printing affordable to foundries worldwide. Designed for turnkey ease of use, S-Max Flex uses SPJ technology to print at high speeds delivering low part costs. Booth 432212.
● The ETEC Xtreme 8K, the world's largest production-grade DLP polymer printer featuring two top-down video projectors, as well as the ETEC Envision One. ETEC systems 3D print a wide range of materials and exclusively offer DuraChain™ photopolymers, such as Elastic ToughRubber™ and FreeFoam™.
About Desktop Metal
Desktop Metal, Inc., based in Burlington, Massachusetts, is accelerating the transformation of manufacturing with an expansive portfolio of 3D printing solutions, from rapid prototyping to mass production. Founded in 2015 by leaders in advanced manufacturing, metallurgy, and robotics, the company is addressing the unmet challenges of speed, cost, and quality to make additive manufacturing an essential tool for engineers and manufacturers around the world. Desktop Metal was selected as one of the world's 30 most promising Technology Pioneers by the World Economic Forum and named to MIT Technology Review's list of 50 Smartest Companies. For more information, visit www.desktopmetal.com.
Featured Product
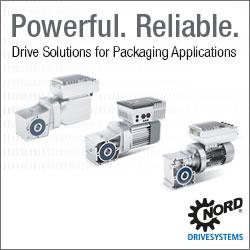