UltraFlex demonstrating efficient induction brazing for aluminum assemblies
The demo had been requested by a manufacturer of electrical vehicle batteries looking to improve their current induction brazing process for an aluminum assembly, by using a more efficient induction power supply.
A recent demo by UltraFlex power technologies showed the efficiency of using UltraFlex induction heaters for an automotive brazing application. The demo had been requested by a manufacturer of electrical vehicle batteries looking to improve their current induction brazing process for an aluminum assembly, by using a more efficient induction power supply.
UltraFlex is a leading provider of advanced, digitally controlled induction heaters and as such is able to respond to most customer induction heating requirements. In this customer case, the parts to be brazed were an aluminum base and 2 aluminum tubes. The customer required that the brazed assembly be in horizontal position and both tubes brazed simultaneously, at maximum heat temperature of 650°C or less. Under these conditions, the customer was looking to achieve the shortest possible heating cycle.
UltraFlex engineers considered a 15 kW induction heater from the UltraFlex UltraHeat W series as most appropriate for this heating scenario. UltraHeat W are advanced, cost-effective 5-15 kW Induction heating systems utilizing the latest switching power supply technology. They feature adaptive digital phase control providing very efficient operation in a wide frequency range.
At power output of only 10 kW out of the available 15 kW, and separate brazing for each tube, the brazing for the entire aluminum assembly was completed within 60 seconds. Thanks to the even heat distribution, there was good alloy flow and the brazing was completed without melting any assembly pieces. The resulting joints were strong and reliable. By using a custom-designed induction coil, the induction brazing could be accomplished for both tubes simultaneously.
This induction brazing demo confirmed that by using a 15 kW UltraFlex induction heater and a custom-designed induction coil, the customer would be able to considerably increase the efficiency of his brazing process. He would achieve reliable and consistent results, independent of the operator skills.
Find out more at:
https://ultraflexpower.com/
Contact us at:
+1.631.467.6814
uptnews@ultraflexpower.com
About UltraFlex Power Technologies:
UltraFlex Power Technologies (ultraflexpower.com) offers the most advanced and innovative digitally controlled induction heating equipment in the industry. Its compact modular and flexible systems are used for a wide variety of induction heating, casting and melting applications.
Featured Product
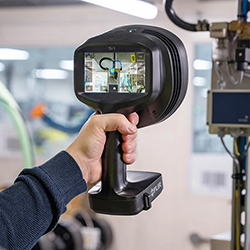