Running High-Pressure Molds in a Low-Pressure Machine Can Improve Your Bottom Line
You can now replace that foaming agent with an inexpensive nitrogen gas inserted into the melt in a machine designed to foam (reduce density) plastic parts.
Some molders currently add expensive foaming agents to a high-pressure mold and part to reduce its density or pay a royalty to add gas to their high-pressure machine. If this, is you, structural foam molding may be the right solution.
You can now replace that foaming agent with an inexpensive nitrogen gas inserted into the melt in a machine designed to foam (reduce density) plastic parts. A Low-Pressure Structural Foam Machine is a good solution for stress free parts, with no warping or part distortion after cooling.
About Low-Pressure Structural Foam Machines:
Low Pressure Structural Foam machines are large platen machines with multiple nozzles capable of being arranged to fill several high-pressure molds at the same time. Platen sizes can range from 54" x 54" to 108" x 186".
With the low cavity pressures associated with short shooting a mold with gas you put multiple high-pressure molds on a large platen and get multiple parts with each cycle.
The parts don't have to be the same size, weight, or shape. Imagine the savings when you run 4 high pressure molds at the same time with one structural foam machine. Plus, you reduce the need for extra floor space, lower labor cost with only one operator, trim your utility cost, and perform less maintenance.
Structural Foam machines can also run hot runner, gas assist, gas counter pressure, cold runner, stack, over molding, and molds of all sizes. Also, by utilizing Wilmington Machinery's Versafil you can sequentially fill each mold independently with various shot sizes. The best candidates for low pressure injection molding are parts with a thicker cross section .1875" or thicker.
Wilmington Machinery offers injection pressures from 6,000 - 10,000 PSI and clamping forces from 500 to 2500 tons. The clamping force may not sound like a lot but are more than adequate when you consider mold cavity pressures of only 300 +/-psi during the fill.
In addition, with a 30:1 L/D feed screw and mixing sections the WM design is excellent for 100% recycled materials and compounding additives in the mix. A two-stage screw and plastic accumulator allow for low shot sizes up to 300 lbs. or more. The secondary accumulator gives you faster injection speeds than a high-pressure machine.
Wilmington Machinery builds machines to last. With 50 years' experience in designing and building superior equipment you can expect your well-maintained Wilmington machine to last for decades (20-30 years).
Featured Product
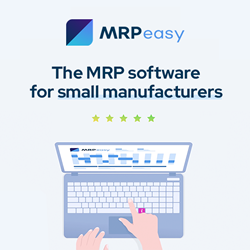
MRPeasy - ERP for Small Manufacturers That Delivers Results
Always know what you have in stock and what you'll need to fulfill orders. Never forget to order parts on time or fail to notice a late delivery from your vendor. Easily create manufacturing orders and schedule them automatically according to resource availability or delivery deadline. Generate accurate cost and lead time estimates and provide customers with quick quotes. Receive notifications when orders are late or inventory levels reach a critical point. Ensure seamless communication between sales, production, warehousing, procurement, administration, and finance. Integrate with popular accounting, CRM, and e-commerce apps. MRPeasy is an ERP software for small manufacturers that gives you all that and more. Our users report a 54% average improvement in the overall performance of their business and a 42% increase in on-time deliveries. Try for free, no credit card needed.