The Basics of Using Wedge Anchors to Secure Fixtures & Equipment to Concrete
Wedge anchors provide the highest and most consistent holding values of any mechanical type of expansion anchor and consist of two separate pieces that are permanently pre-assembled into a single unit.
The Basics
Wedge anchors provide the highest and most consistent holding values of any mechanical type of expansion anchor and consist of two separate pieces that are permanently pre-assembled into a single unit. The first piece is a carbon steel rod that is threaded for a portion of its length. The opposite/installed end of the anchor has a necked-down diameter, or conical space, that tapers outward back to the rod's full diameter.
The second piece of the wedge anchor is a steel slip or sleeve, that is permanently assembled around the conical section of the rod. Each wedge anchor also requires a nut and washer to complete the installation.
Wedge anchors can be used in numerous applications such as windows and doors, signage, machinery and more, only if the base material is solid concrete. Unlike many other concrete fasteners, the wedge anchor cannot be used in brick or block.
The wedge anchor is simple to use and is available in a wide variety of diameters and lengths. Wedge anchors can be used for both light and heavy-duty applications.
· Available in a wide range of diameters ranging from 1/4" to 1-1/4". The anchor lengths, which depend on the diameter, are from 1-3/4" to 12".
· A 1/4" x 1-3/4" wedge anchor, for instance, would be utilized in a light duty application, while a 1-1/4" x 12" anchor would be used in a situation that requires a heavy-duty anchor.
· Most are available in zinc plated carbon steel for indoor dry applications, hot-dipped galvanized for moist outdoor applications, 304 stainless steel for wet outdoor applications and 316 stainless steel for use in caustic environment.
Technical Specifications:
To ensure safe and proper wedge anchor use, certain technical specifications must be considered. These include length, spacing and installation.
Length:
To determine the length of wedge anchor required, add the thickness of the material to be fastened, plus minimum embedment, plus the thickness of the nut and washer. The sum of these three items equals the minimum wedge anchor length. The Wedge anchor requires no maximum hole depth. The depth of the hole in the base material should be at least the length of the anchor minus the thickness of the material being fastened. This will provide some extra depth to accommodate a minor amount of concrete cuttings which may not be able to be cleaned out of the hole.
Spacing:
The forces on a Wedge Anchor are transferred to the base material in which it is installed. If the anchors are installed to close together, it can cause an interaction of the forces, thus reducing the holding power of the anchor. As a rule of thumb, the expansion anchor industry has established a minimum standard of ten (10) anchor diameters for spacing between anchors and five (5) anchor diameters from an unsupported edge. When vibration or sudden impact is part of the load conditions, the spacing between anchors should be increased.
Technical Information: Ultimate Load Values in 2000 PSI Concrete
Values shown are average ultimate values and are offered only as a guide and are not guaranteed. A safety factor of 4:1 or 25% is generally accepted as a safe working load. Reference should be made to applicable codes for the specific working ratio.
Installation:
Installing wedge anchors can be completed in five easy steps. Wedge anchors can be used in solid concrete applications, are best suited for light to heavy-duty fastening purposes, are available in diameters from 1/4" up to 1-1/4", and are available in standard zinc plated, hot dipped galvanized and stainless steel.
To determine the minimum anchor length for your application, simply add the material thickness to the minimum embedment and add the thickness of the nut & washer.
Installation steps:
1-Hammer wedge anchor into hole deep enough so that threads are below surface of base material. Drill hole 1/2 " deeper than wedge anchor embedment using a carbide tipped bit. (Hole size is wedge anchor size). Tighten nut turning approximately three or four full turns.
2- Drill a hole in the concrete at least 1/2" deeper than the wedge anchor embedment using a hammer drill and a correctly sized carbide tipped bit. (Hole size is wedge anchor size).
3- Clean out the hole of all debris.
4- Place the nut on the end of the wedge anchor (to protect the threads of the wedge anchor during installation).
5- Hammer the wedge anchor into the hole deep enough so that the threads are below the surface of the base material.
Tighten the nut - turning approximately three or four full turns.
To find out, even more, take a look at this detailed article about the Proper Selection and Installation of Wedge Anchors.
https://www.confast.com/products-wedge-confast-zinc-plated/
Featured Product
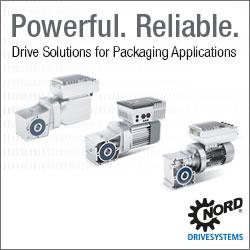
NORD Delivers Powerful, Reliable Drive Solutions for Demanding Packaging Applications
When you need quality, flexibility and high efficiency, NORD has you covered with complete drive solutions for primary and secondary packaging, end-of-line packaging, and higher-level applications. NORD supports you through the entire life cycle of your drive systems with pre-sales engineering support, online tools, and a global service network. Drive systems for both vertically and horizontally networked technology with all the options for sensor incorporation and integration into the higher-level control system.